铝、镁及其合金粉检测的重要性与应用背景
铝、镁及其合金粉作为重要的工业原料,广泛应用于航空航天、汽车制造、化工催化、3D打印及新能源领域。由于这类材料具有高活性、易燃易爆特性,其物理化学性质的精准控制直接影响生产安全与产品质量。因此,针对铝、镁及其合金粉的检测项目需覆盖成分分析、粒度分布、活性指标及安全性评估等多个维度,以确保其符合行业标准和特定工况要求。
核心检测项目及方法
1. 化学成分分析
通过电感耦合等离子体发射光谱法(ICP-OES)或X射线荧光光谱法(XRF)对铝、镁主含量及杂质元素(如Fe、Si、Cu等)进行定量分析,确保杂质含量符合ASTM B928、GB/T 3190等标准。合金成分需重点检测添加元素(如Zn、Mn、Zr等)的实际占比与配比误差。
2. 粒度分布与比表面积检测
采用激光粒度分析仪测定粉末的D10、D50、D90值及分布曲线,同时通过BET法测量比表面积。对于超细粉体(粒径<10μm),需结合动态光散射(DLS)技术,避免团聚现象干扰数据准确性。
3. 氧含量及活性金属测定
使用惰气熔融-红外吸收法测定总氧含量,采用滴定法或电位法分析活性金属(如游离镁)的比例。高氧含量会降低材料反应活性,而活性金属超标可能引发自燃风险,此项目为安全应用的关键指标。
4. 水分及挥发性物质检测
通过卡尔费休法(Karl Fischer)测定水分含量,热重分析仪(TGA)评估挥发性有机物残留。水分超标易导致粉末结块或氢脆现象,而挥发物残留可能影响烧结过程的稳定性。
5. 爆炸性及静电敏感性测试
依据ISO 80079-36标准进行粉尘云最小点火能(MIE)和粉尘层最低着火温度(LIT)测试,结合静电积累实验评估粉末的燃爆风险。镁粉等高风险材料需额外开展密闭空间燃烧速率检测。
6. 微观形貌与晶体结构表征
利用扫描电镜(SEM)观察颗粒形貌及表面缺陷,X射线衍射(XRD)分析相组成与晶体结构。球形度、表面粗糙度等参数直接影响流动性及成型性能,而氧化相的占比反映储存稳定性。
检测标准与质量控制要点
检测过程需严格遵循ISO 12154(金属粉末粒度测定)、GB/T 5158(金属粉末氧含量测定)等国际/国家标准,同时结合生产企业的工艺要求制定内控指标。对于高附加值产品(如增材制造用粉),还需增加流动速率、松装密度等工艺适配性测试,确保粉末满足终端应用的性能需求。
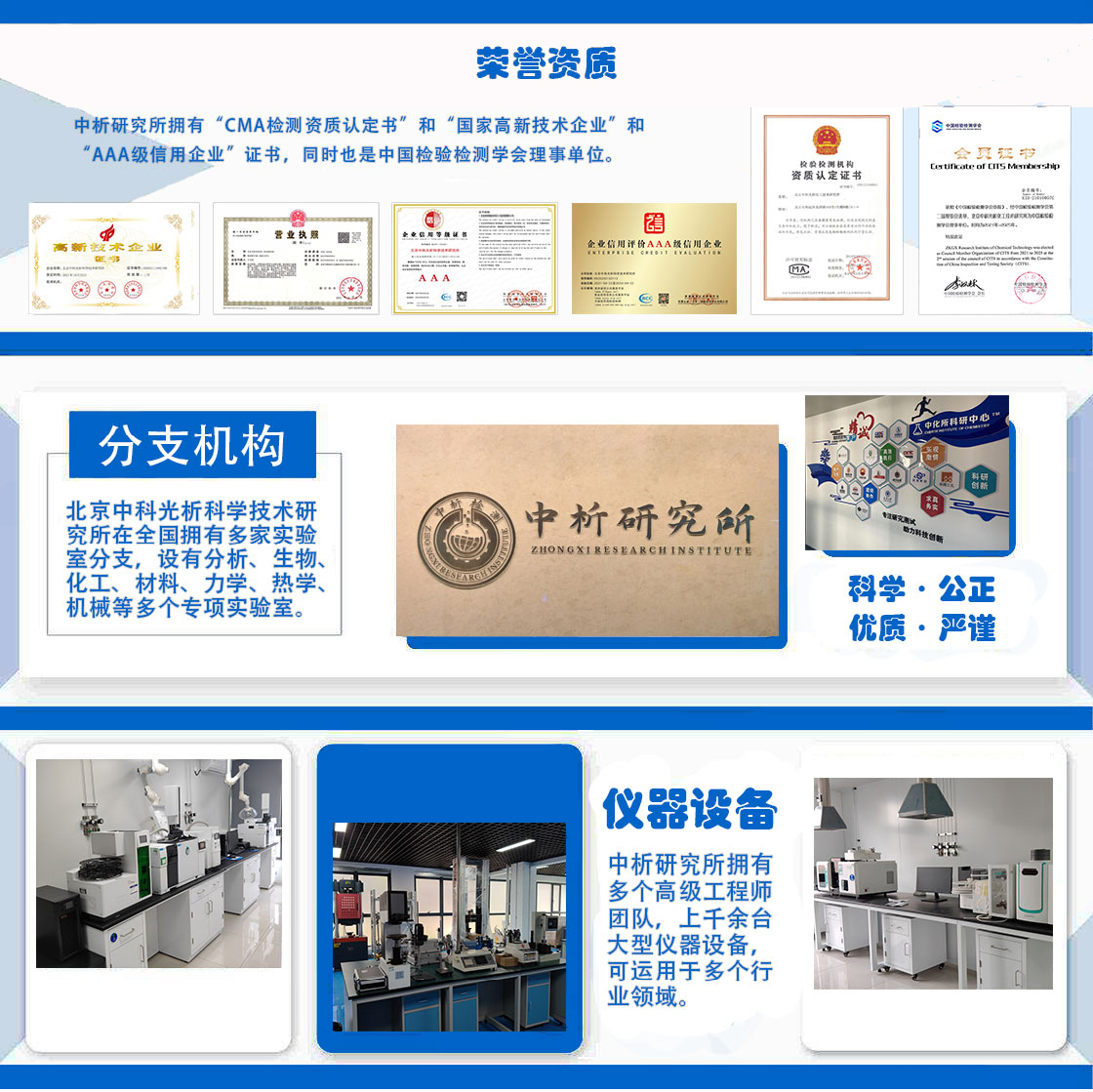
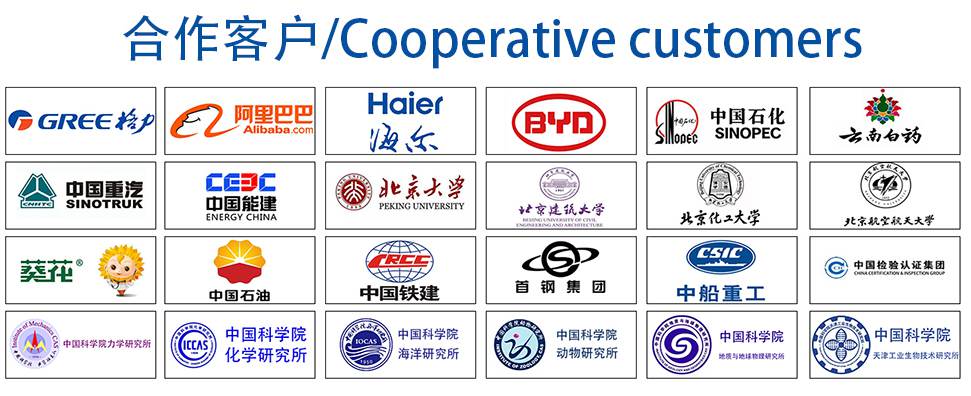