自行车轮辋检测的重要性
作为自行车的关键承载部件,轮辋的性能直接关系到骑行的安全性、稳定性和舒适性。无论是公路车、山地车还是城市通勤车,轮辋在骑行过程中需要承受复杂的动态载荷,包括垂直压力、侧向冲击力以及制动时的摩擦力。随着材料技术的进步,轮辋的材质从传统的钢制发展到铝合金、碳纤维甚至钛合金,但无论材质如何变化,其尺寸精度、结构强度和耐久性始终是核心质量指标。通过系统化的轮辋检测,可以有效预防因轮辋变形、断裂或装配偏差导致的骑行事故,同时延长零部件的使用寿命。
核心检测项目与标准
1. 尺寸精度检测
使用三坐标测量仪或高精度卡尺对轮辋的内径、外径、截面宽度进行测量,确保符合ISO 4210或EN 14764标准。重点检查刹车边平面度公差(通常≤0.3mm)和轮辋接缝处的对接精度,避免安装轮胎时出现漏气或偏摆问题。
2. 动态平衡测试
通过动平衡机模拟骑行状态下的高速旋转(最高达60km/h),检测轮辋的质心偏移量。合格标准要求不平衡量小于5g·cm,超标会导致骑行时车身抖动,长期使用可能加速轴承磨损。
3. 疲劳强度试验
在液压伺服测试机上对轮辋施加周期性径向载荷(一般为骑行负载的1.5倍),进行10万次以上循环测试。试验后轮辋不得出现裂纹或永久变形,碳纤维轮辋还需通过高温(80℃)和低温(-20℃)交变环境下的强度验证。
4. 材料成分分析
采用光谱分析仪检测铝合金轮辋的合金配比(如6061-T6中的镁硅含量),碳纤维轮辋需通过显微CT扫描确认树脂浸渍均匀性。同时通过硬度计测量表面维氏硬度(HV≥70),防止材料虚标导致的早期磨损。
5. 表面处理质量评估
使用涂层测厚仪检查阳极氧化层或烤漆厚度(铝轮标准为10-25μm),进行百格测试验证附着力(脱落面积<5%)。对刹车边需额外进行盐雾试验(72小时无腐蚀)和耐磨测试(500次砂纸摩擦后涂层保留率≥90%)。
智能化检测技术发展
近年来,机器视觉系统开始应用于轮辋在线检测,通过高帧率工业相机捕捉轮辋高速旋转时的轮廓偏差,结合AI算法实时判断缺陷类型。激光位移传感器可精准测量辐条孔位分布角度误差(允许±0.5°偏差),部分高端检测线还能同步生成3D模型进行虚拟装配验证,显著提升检测效率与准确性。
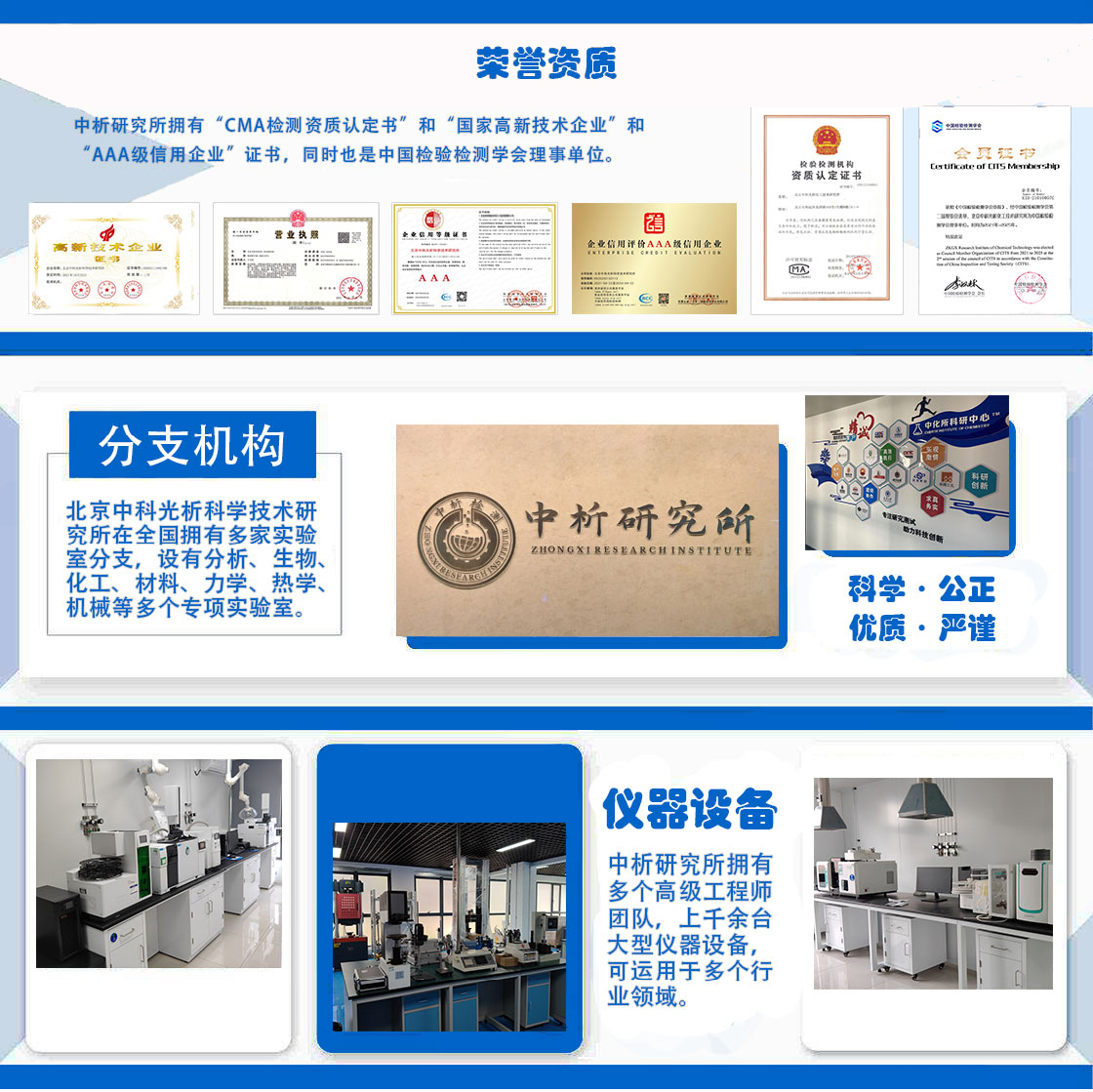
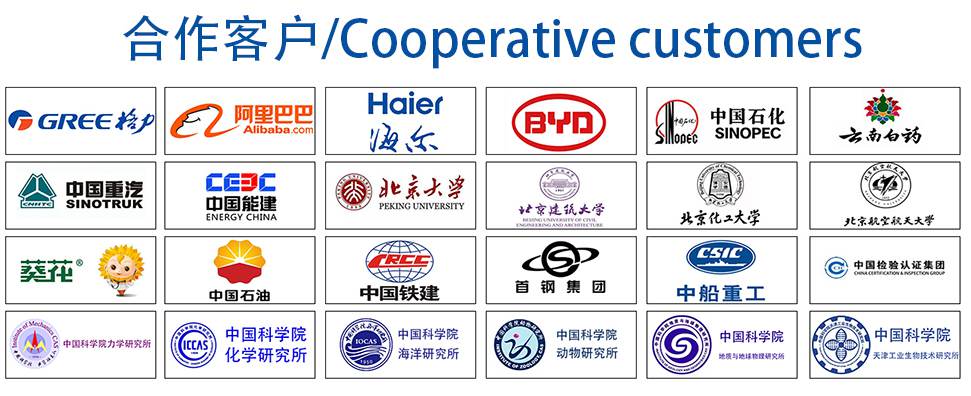