浮法玻璃检测的重要性与核心项目解析
浮法玻璃作为现代建筑、汽车和家电领域广泛应用的基础材料,其质量直接影响产品的安全性和使用性能。根据2023年行业统计数据显示,浮法玻璃年产量已突破8000万吨,而质量缺陷导致的行业损失占比达2.7%。为确保浮法玻璃达到ASTM C1036、GB 11614等国际/国家标准要求,建立系统化的检测体系成为生产流程中不可或缺的关键环节。
核心检测项目与技术方法
1. 外观质量检测
采用D65标准光源箱配合目视检查,重点检测气泡(直径>0.5mm)、结石(尺寸>0.3mm)、划痕(长度>20mm)等表面缺陷。最新检测设备配备500万像素工业相机,运用机器视觉技术可实现0.01mm级缺陷捕捉,检测速度达10m/min。
2. 厚度均匀性检测
使用β射线测厚仪或激光干涉仪进行在线监测,测量精度可达±0.01mm。根据GB 11614要求,3mm厚度玻璃的厚度公差应控制在±0.2mm以内,6mm玻璃则为±0.3mm。近年兴起的太赫兹成像技术能实现非接触式全幅面厚度测绘。
3. 应力分布检测
通过偏光应力仪进行检测,要求表面压应力值在69-103MPa范围,中心张应力不超过34.5MPa。齐全设备配备数字图像处理系统,可生成彩色应力分布云图,准确识别应力集中区域。
4. 光学性能检测
采用分光光度计测定可见光透射比(通常>89%)、太阳光直接透射比(需符合GB/T 2680规定)和雾度值(≤0.8%)。高端实验室配备积分球系统,可完成0.3-2.5μm全光谱分析。
5. 化学成分检测
运用X射线荧光光谱仪(XRF)进行主要成分分析,要求SiO₂含量72-73%、Na₂O 13-14%、CaO 8-10%。特殊品种需检测Fe₂O₃含量(普通级≤0.15%,超白玻璃≤0.015%)。
智能化检测技术发展趋势
目前行业正推进AI质检系统应用,通过深度学习算法实现缺陷自动分类(准确率>98%),5G技术支持的云平台可实现检测数据实时上传与分析。2024年实施的ISO 1288新标准将引入基于大数据的质量预测模型,推动检测效率提升40%以上。
通过建立涵盖原料、制程、成品的全链条检测体系,配合齐全的检测设备与智能化技术,可有效保障浮法玻璃的平整度、强度及光学性能,为下游应用提供可靠的材料基础。这对于提升建筑节能效果、确保汽车安全玻璃性能和延长家电使用寿命具有重要现实意义。
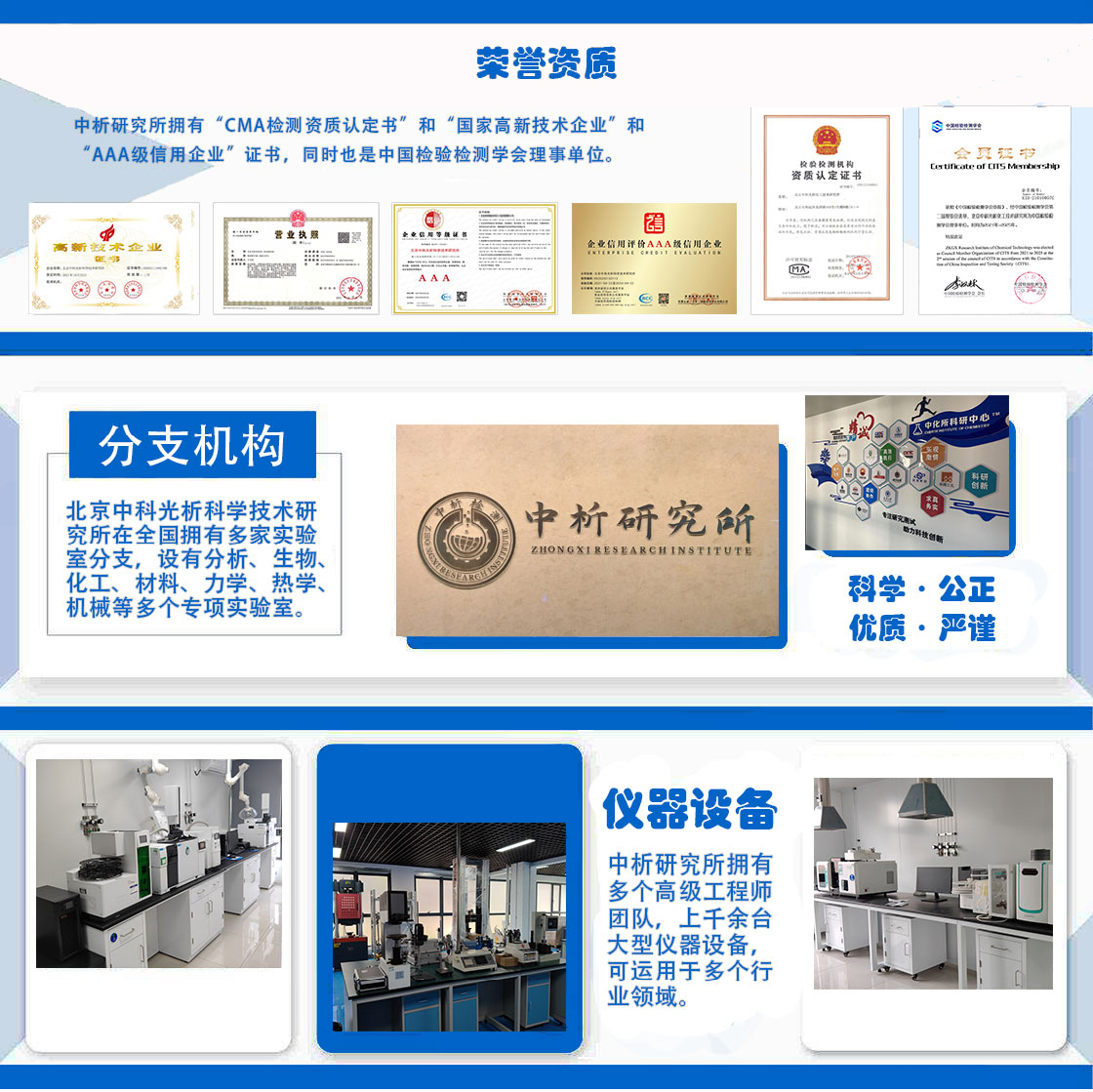
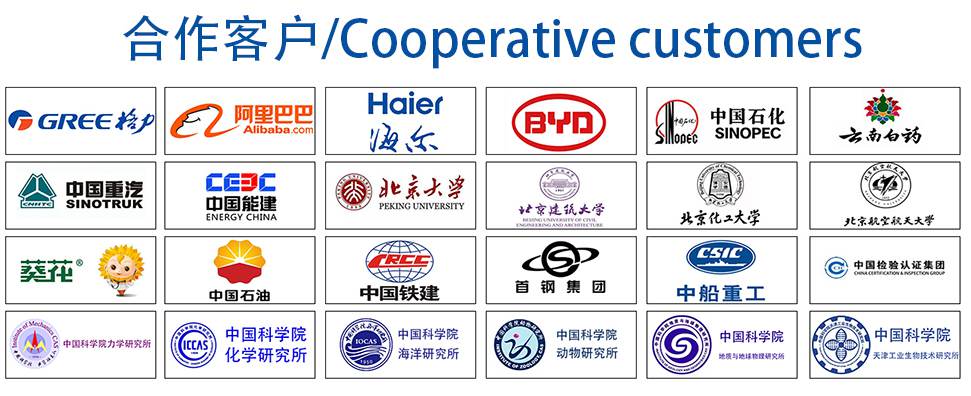