井口装置及采油树检测概述
井口装置及采油树作为油气开采系统的核心设备,承担着控制井内压力、引导流体流向及保障作业安全的关键作用。其长期处于高温、高压、腐蚀等复杂工况下,设备完整性直接影响油田生产安全和经济效益。根据API 6A、SY/T 5127等标准要求,需通过系统性检测评估设备性能状态,预防井喷、泄漏等重大事故。检测工作覆盖材料性能、密封能力、承压强度及功能可靠性四大维度,贯穿设备全生命周期管理。
核心检测项目与技术规范
1. 外观与尺寸检测
采用三维激光扫描与目视检测结合,核查法兰平面度、密封槽尺寸、连接螺纹精度等关键参数。重点检测阀体表面裂纹、腐蚀坑等缺陷,要求表面粗糙度≤Ra3.2μm,法兰平面偏差不超过0.05mm/m。
2. 材料性能检测
通过光谱分析验证材质成分是否满足ASTM A182标准,进行硬度测试(HB180-220)、冲击试验(-46℃夏比冲击功≥40J)及金相组织分析。针对H₂S环境需额外进行SSC应力腐蚀试验。
3. 压力完整性测试
执行API 6A规定的压力循环试验:
- 壳体强度试验:1.5倍额定工作压力保压30分钟
- 密封试验:额定压力下保持15分钟无渗漏
- 气体密封性试验(氦检漏):泄漏率≤1×10⁻⁶ mbar·L/s
4. 阀门功能性验证
采用电动扭矩测试仪检测主阀、安全阀启闭扭矩,开关循环试验≥500次无卡阻。节流阀需进行20%-100%开度调节精度测试,流量特性曲线需符合设计要求。
齐全检测技术应用
1. 超声波相控阵检测(PAUT)
对法兰连接区、阀体焊缝实施全截面扫查,可检测最小0.5mm深度的内部缺陷,相比常规UT检测效率提升60%。
2. 数字化孪生评估
基于ANSYS仿真平台建立设备数字模型,模拟极端工况下的应力分布,预测剩余使用寿命,指导维修决策。
3. 动态密封监测系统
安装光纤Bragg光栅传感器实时监测密封面接触压力,当压力下降超过15%时触发预警,实现主动式维护。
检测周期与管理要求
新建装置须通过第三方型式试验认证,在役设备执行分级检测:
- I类设备(含硫井):年度全面检测
- II类设备(高压井):2年检测周期
- III类设备(常压井):5年检测周期
检测数据需接入QHSE管理系统,建立包含10万+检测数据点的设备健康档案库。
通过系统化检测与智能化监测技术的融合应用,现代井口装置检测已实现从"事后维修"向"预测性维护"的转型。统计数据显示,规范化的检测程序可使设备故障率降低75%,延长使用寿命8-10年,为油气田安全生产提供坚实保障。
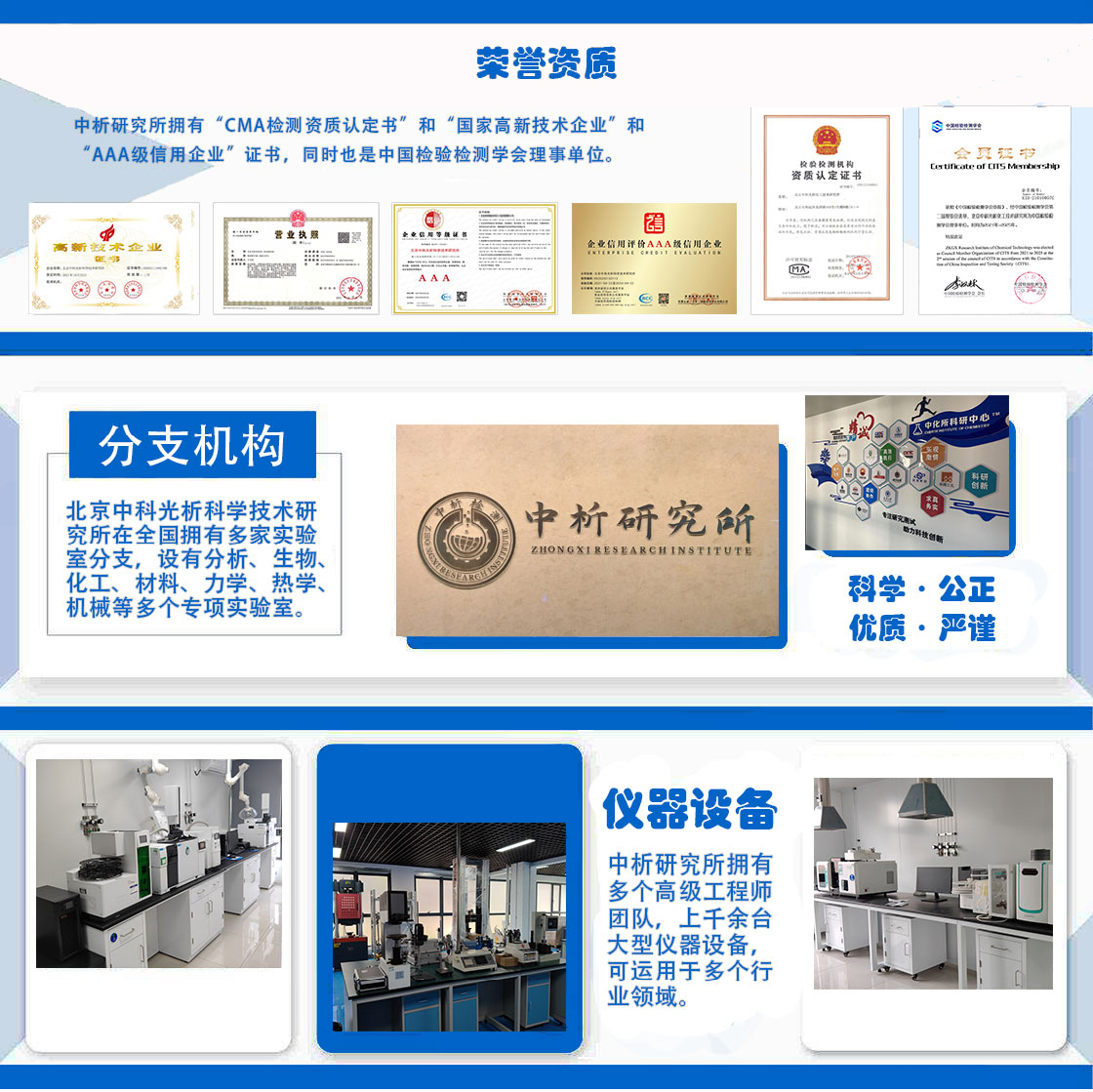
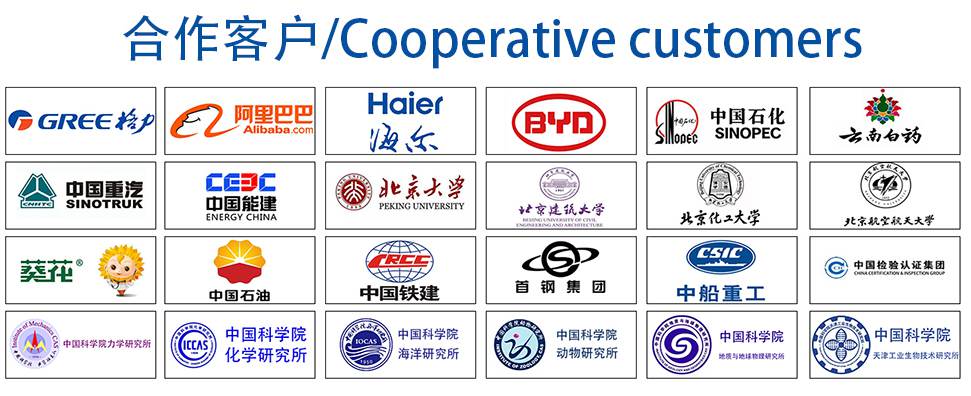