电容器用金属化薄膜检测的重要性
电容器作为电子设备中不可或缺的被动元件,其性能直接影响到电路的稳定性和效率。金属化薄膜是电容器核心材料之一,通过在聚合物基膜(如聚酯、聚丙烯)表面真空蒸镀纳米级金属层(通常为铝或锌),赋予其导电性与自愈功能。然而,金属化薄膜的厚度均匀性、附着力、耐压性等参数直接影响电容器的容量、损耗和寿命。因此,严格的检测流程是确保成品电容器可靠性的关键环节。
主要检测项目及方法
1. 电气性能检测
方阻测试:通过四探针法测量金属化薄膜单位面积电阻,确保镀层导电性符合设计要求,通常方阻范围需控制在2-10Ω/□之间,具体依据电容器类型调整。
耐压能力测试:使用高压测试仪施加额定电压(如400V DC至2000V DC),检测薄膜在持续电场下的绝缘强度,观察是否发生击穿或局部放电现象。
自愈性验证:通过模拟局部击穿试验,检测金属层在短路瞬间蒸发隔离缺陷的能力,评估自愈效率及对电容值的影响。
2. 机械性能检测
拉伸强度与延伸率:利用拉力试验机测试基膜与金属镀层的结合强度,确保薄膜在卷绕工艺中不易断裂,聚丙烯基膜的典型拉伸强度需≥100MPa。
厚度均匀性检测:采用激光测厚仪或β射线测厚仪,沿薄膜纵向和横向多点测量,厚度偏差需控制在±3%以内,避免因局部过薄引发击穿风险。
3. 表面质量分析
针孔缺陷检测:通过光学显微镜或电子扫描显微镜(SEM)观察镀层表面,统计单位面积内针孔数量,通常要求≤5个/m²,且最大孔径不超过5μm。
表面粗糙度测试:使用原子力显微镜(AFM)或轮廓仪量化镀层表面形貌,粗糙度Ra值需保持在0.05-0.15μm范围内,以确保金属层与基膜的良好结合。
4. 耐环境性能测试
高温高湿试验:将薄膜置于85℃/85%RH环境中500小时,检测镀层氧化程度和方阻变化率,要求电阻漂移≤10%且无可见氧化斑。
温度循环测试:在-55℃至+125℃间进行100次循环,验证薄膜热胀冷缩下的抗开裂能力,确保金属层与基膜的热匹配性。
5. 化学成分分析
镀层纯度检测:采用X射线荧光光谱仪(XRF)分析金属层成分,铝纯度需≥99.9%,杂质元素(如Fe、Cu)含量需≤0.01%以避免电化学腐蚀。
有机物残留检测:通过气相色谱-质谱联用仪(GC-MS)测定蒸镀工艺中残留的溶剂或脱模剂,总残留量应<50ppm,防止介质损耗角增大。
结语
金属化薄膜的检测需贯穿原材料筛选、生产过程监控及成品验收全流程。通过上述多维度的检测项目,可系统性评估薄膜的物理、化学及电气特性,为高可靠性电容器的制造提供数据支撑。未来随着新能源、电动汽车等领域对电容器性能要求的提升,金属化薄膜的检测技术将向更高精度、自动化方向发展。
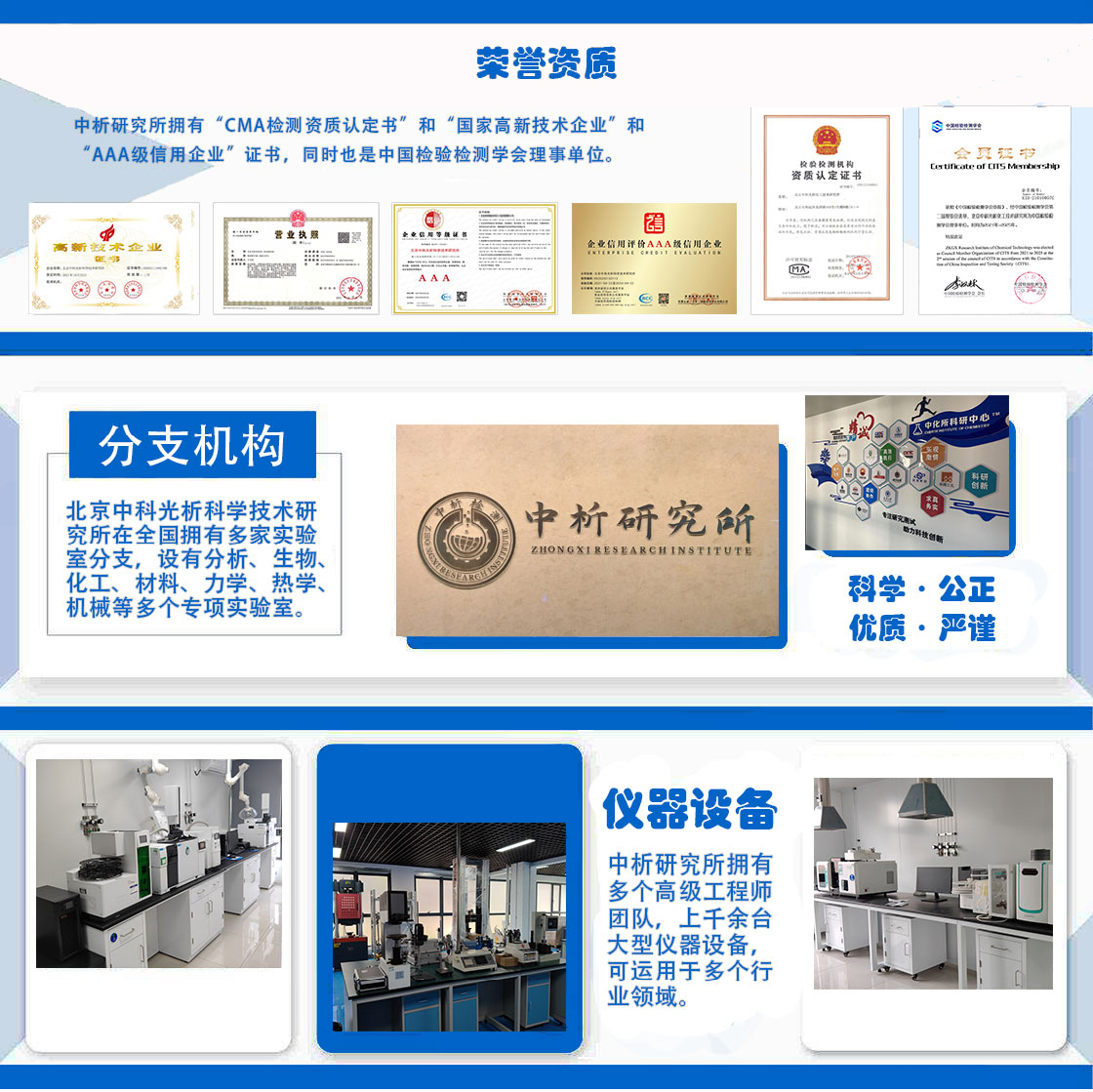
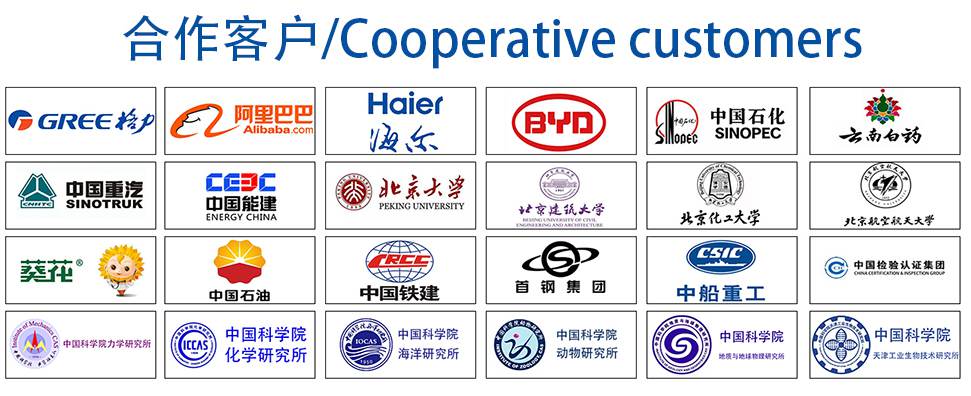