辊锻模检测的关键项目与技术要点
辊锻模作为金属塑性成形工艺的核心装备,其质量直接影响锻件精度、生产效率和模具使用寿命。在汽车零部件、航空航天锻件等高端制造领域,辊锻模需要承受高温、高压和循环载荷的复杂工况环境,因此系统化的检测项目成为确保模具性能的重要保障。通过全面检测可有效识别模具早期缺陷,预防裂纹扩展、型腔变形等失效风险,同时为模具维护和工艺优化提供数据支持。
1. 模具尺寸精度检测
采用三坐标测量机(CMM)对模具型腔进行三维扫描,重点检测关键截面曲线与理论模型的偏差值。对于批量生产的模具,需建立周期性复测机制,监控分模面配合间隙、导向结构磨损量等指标。高精度激光跟踪仪可对大型模具(长度>5米)进行现场动态测量,确保多工位模具的装配一致性。
2. 表面质量评估
通过磁粉探伤(MT)或渗透探伤(PT)检测模具工作表面的裂纹、折叠等缺陷,对于合金钢模具需特别注意热处理引起的表面微裂纹。使用表面粗糙度仪测量型腔区域Ra值(建议控制在0.8-1.6μm),同时配合金相显微镜分析表面脱碳层深度,确保其不超过设计允许的0.1mm阈值。
3. 材料性能验证
在模具制造阶段需取样进行理化分析,重点检测:①材料成分(如H13钢的Cr含量5.00-5.50%);②冲击韧性(室温AKU≥25J);③高温强度(600℃拉伸强度≥800MPa)。对于修复模具,需通过超声波测厚仪核查关键部位的剩余壁厚,避免因材料流失导致的强度不足。
4. 硬度分布检测
采用里氏硬度计进行网格化硬度测试(网格密度10×10cm),绘制模具整体硬度分布云图。型腔表面硬度应稳定在48-52HRC范围,芯部硬度与表面差异不超过3HRC。特别注意过渡区域的硬度梯度变化,避免因淬火工艺不当引起的应力集中。
5. 疲劳寿命预测
通过有限元分析(FEA)模拟模具的应力集中区域,结合应变片实测数据进行验证。对服役超5000次的模具实施定期裂纹检测,采用声发射技术监测裂纹扩展速率。建立模具寿命数据库,根据实际服役数据修正理论预测模型,实现剩余寿命的精准评估。
现代检测技术已发展出基于工业CT的模具内部缺陷可视化检测、基于机器视觉的在线尺寸监测系统等创新方法。建议企业建立包含上述检测项目的标准化流程,结合ISO 9001质量管理体系要求,形成从模具验收、服役监测到报废评估的全生命周期质量控制闭环。
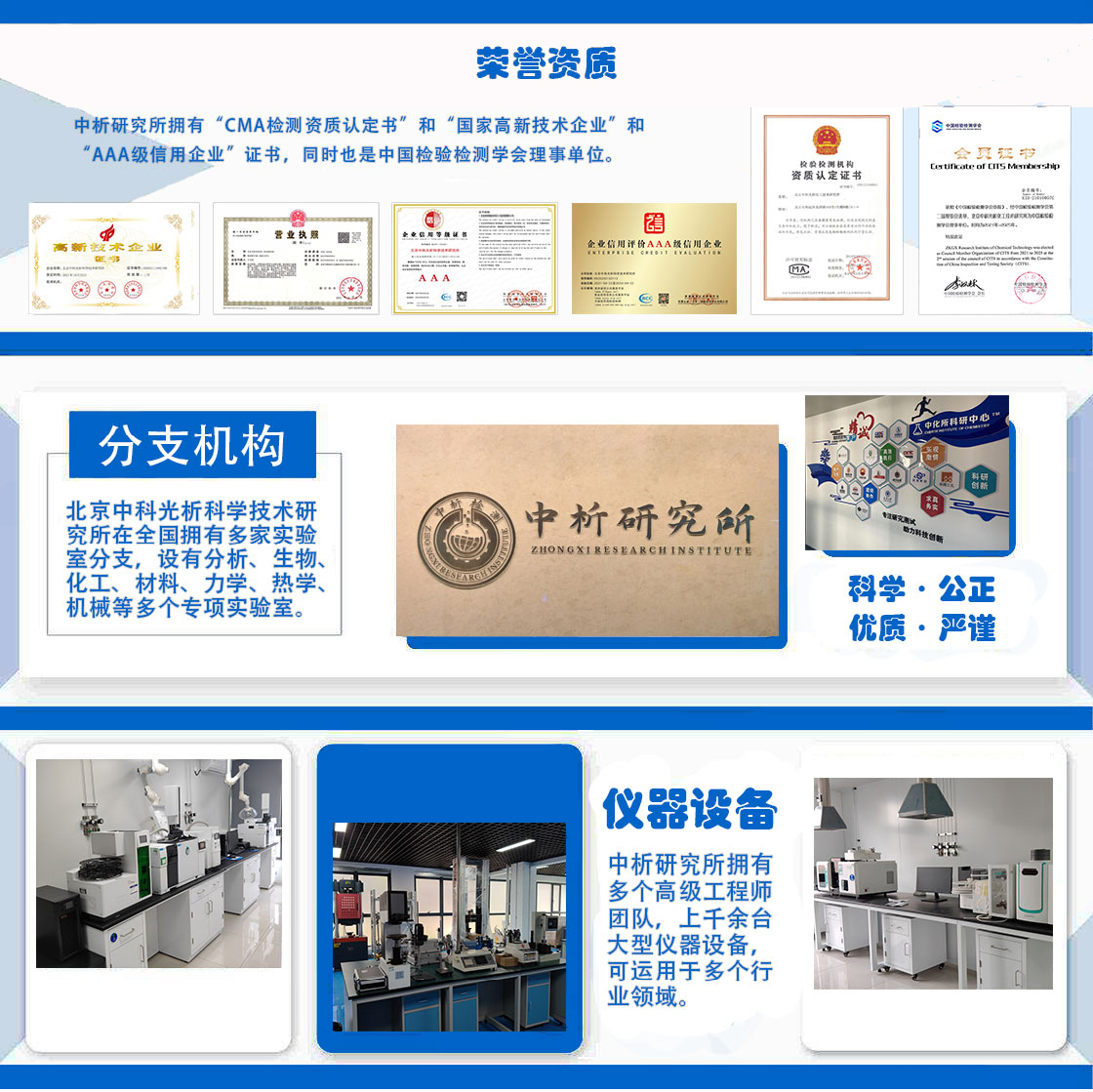
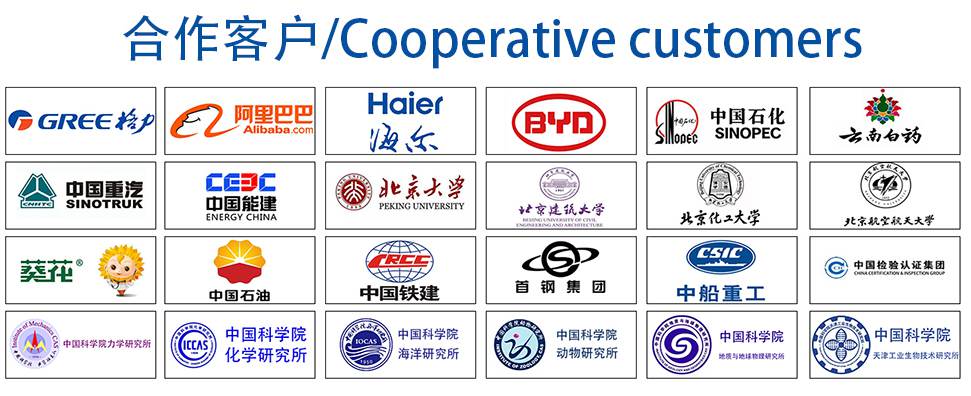