工业防护涂料中有害物质检测的重要性
工业防护涂料广泛应用于船舶、桥梁、管道、储罐等设施的表面防护,能够有效抵御腐蚀、高温、化学侵蚀等环境危害。然而,涂料生产过程中常会添加溶剂、重金属、有机化合物等物质,以改善涂料的物理性能和施工特性。这些物质若含量超标,不仅会对施工人员的健康造成威胁,还可能通过挥发、渗漏等途径污染环境,甚至影响终端产品的安全性。因此,对工业防护涂料中有害物质进行系统性检测,既是保障人体健康和生态环境的必要措施,也是企业满足国内外法规标准、提升市场竞争力的重要环节。
核心检测项目及技术方法
1. 挥发性有机化合物(VOCs)检测
VOCs是工业涂料中主要的环境污染物,包括苯、甲苯、二甲苯、甲醛等。检测时需依据GB 30981-2020《工业防护涂料中有害物质限量》标准,采用气相色谱-质谱联用(GC-MS)或热脱附法测定总VOCs含量。企业需重点关注涂料施工和固化阶段的VOCs释放控制。
2. 重金属含量检测
铅、镉、铬、汞等重金属可能存在于颜料或防锈添加剂中。通过原子吸收光谱法(AAS)或电感耦合等离子体质谱法(ICP-MS)可精确测定其含量。例如,欧盟REACH法规对涂料中铅的限值为0.01%(质量分数),超出限值将面临贸易壁垒。
3. 苯系物及甲醛检测
苯系物具有强致癌性,而甲醛则是常见的致敏物质。检测需使用高效液相色谱(HPLC)或分光光度法,确保符合GB 18581-2020《室内装饰装修材料溶剂型木器涂料中有害物质限量》等标准的要求,特别是在封闭空间施工场景中需严格管控。
4. 其他特定有害物质筛查
包括短链氯化石蜡(SCCPs)、邻苯二甲酸酯类增塑剂(如DBP、DEHP)以及异氰酸酯类固化剂等。针对这些物质,需采用高灵敏度检测技术,如液相色谱-串联质谱(LC-MS/MS),并结合欧盟RoHS、中国《新化学物质环境管理办法》等法规进行合规性评价。
检测流程与技术发展趋势
检测流程通常包括样品采集、前处理、仪器分析和数据审核四个阶段。当前,快速检测技术(如便携式XRF光谱仪)和在线监测系统的应用显著提升了检测效率。同时,绿色涂料配方的研发推动了对低VOCs、无重金属涂料的全生命周期检测需求。未来,随着人工智能在数据分析中的渗透,检测结果的准确性和可追溯性将进一步提升。
结论
工业防护涂料的有害物质检测是连接产品质量、环境责任与市场准入的核心环节。通过建立标准化的检测体系,企业不仅能规避法律风险,更能推动行业向环保化、高端化转型。随着“双碳”目标的推进,对涂料中有害物质的管控将更加严格,技术创新与法规适配将成为产业发展的重要驱动力。
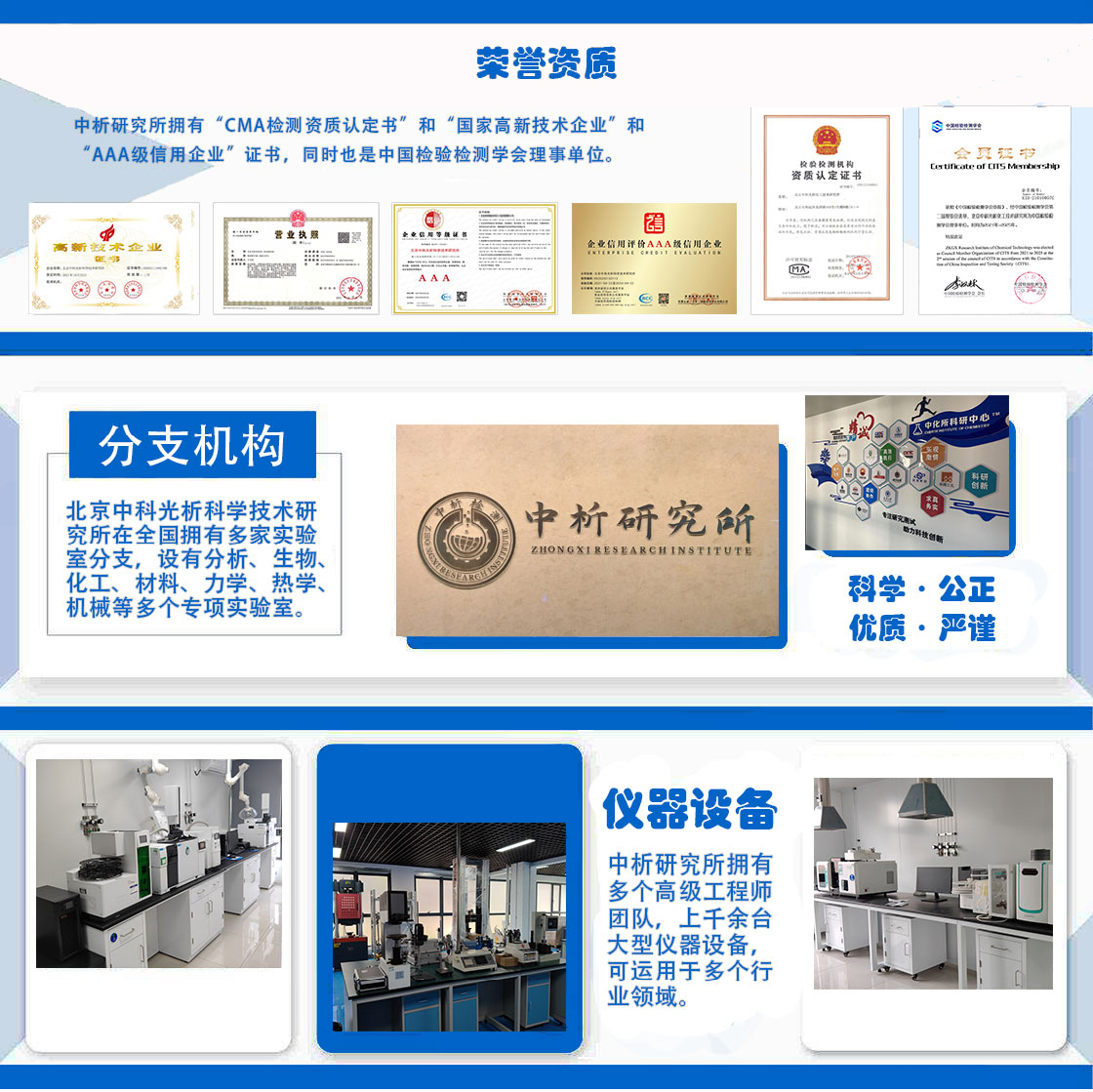
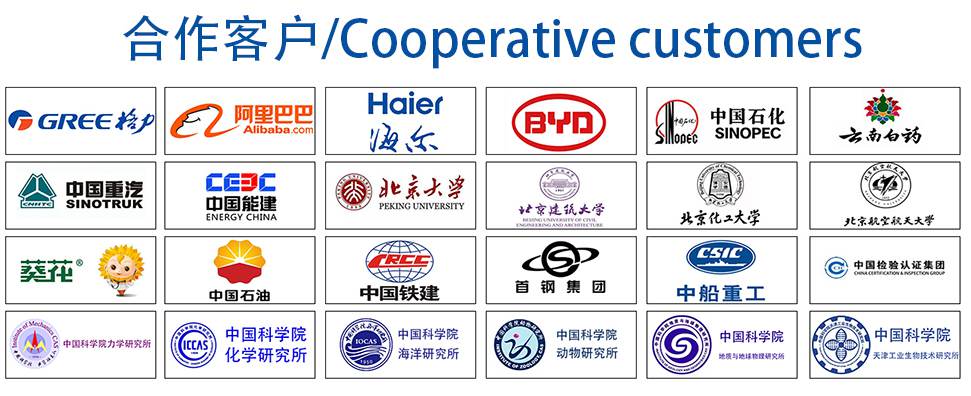