随着新能源电动汽车产业的快速发展,充电桩作为核心基础设施的制造标准日益严格。充电桩壳体作为设备防护的第一道屏障,其材料性能直接关系到设备安全性、使用寿命及环境适应性。聚碳酸酯/丙烯腈-丁二烯-苯乙烯(PC/ABS)合金凭借优异的机械强度、耐候性和阻燃性能,成为充电桩壳体的主流材料之一。然而,由于充电桩需长期暴露于户外复杂环境(如高温、雨水、紫外线等),且需满足电气绝缘、防火安全等严苛要求,对PC/ABS专用料的检测项目提出了系统性规范。
一、基础物性检测
PC/ABS专用料的基础物性检测是材料质量控制的基石。需通过熔融指数(MFI)测试评估加工流动性,确保注塑成型工艺稳定性;采用GB/T 1040标准进行拉伸强度、弯曲强度及冲击强度测试,验证材料的力学性能是否满足壳体抗压、抗冲击需求。此外,热变形温度(HDT)测试可判断材料在高温环境下的结构稳定性,避免壳体因温度变化导致变形失效。
二、阻燃性能检测
充电桩壳体需满足UL94 V-0级阻燃标准,此项检测通过垂直燃烧试验评估材料的自熄性及熔滴情况。同时,灼热丝可燃性指数(GWFI)和灼热丝起燃温度(GWIT)测试模拟电气故障引发的过热场景,确保材料在高温接触条件下不引发明火,这对预防充电桩电气火灾风险至关重要。
三、电气绝缘性能检测
根据IEC 60243标准,需测试PC/ABS材料的介电强度、体积电阻率和表面电阻率,验证其在潮湿、污秽环境下仍能保持可靠绝缘性。局部放电测试则可进一步评估材料在高电压工况下的耐电痕化能力,防止因漏电引发的安全事故。
四、耐候性与环境适应性检测
通过紫外老化试验(QUV)、氙灯老化试验模拟户外光照条件,评估材料抗黄变、抗粉化能力;高低温循环试验(-40℃~85℃)验证壳体在极端温差下的尺寸稳定性。盐雾试验则模拟沿海地区高盐环境,检测材料的耐腐蚀性能,防止金属嵌件锈蚀扩散至塑料基体。
五、环保与化学稳定性检测
依据RoHS和REACH法规,需对材料中重金属(铅、镉等)、多溴联苯(PBBs)等有害物质进行定量分析。同时,耐化学品测试(如汽油、酸雨溶液浸泡)可评估壳体在意外接触腐蚀性物质时的抗溶胀、抗开裂能力,确保长期使用可靠性。
六、加工性能与外观质量检测
材料加工前需进行水分含量测试(卡尔费休法),避免注塑过程中产生银纹等缺陷。成型后壳体需通过色差仪检测颜色一致性,并利用落球冲击试验、划痕测试验证表面涂层附着力。此外,CTI(漏电起痕指数)测试可进一步确认材料在潮湿污染条件下的绝缘耐久性。
综上所述,PC/ABS充电桩壳体专用料的检测需构建涵盖物理、化学、电气及环境适应性的多维评价体系。通过标准化检测流程,可有效保障材料性能与充电桩全生命周期安全需求的匹配,为新能源汽车基础设施的可靠运行提供技术支撑。
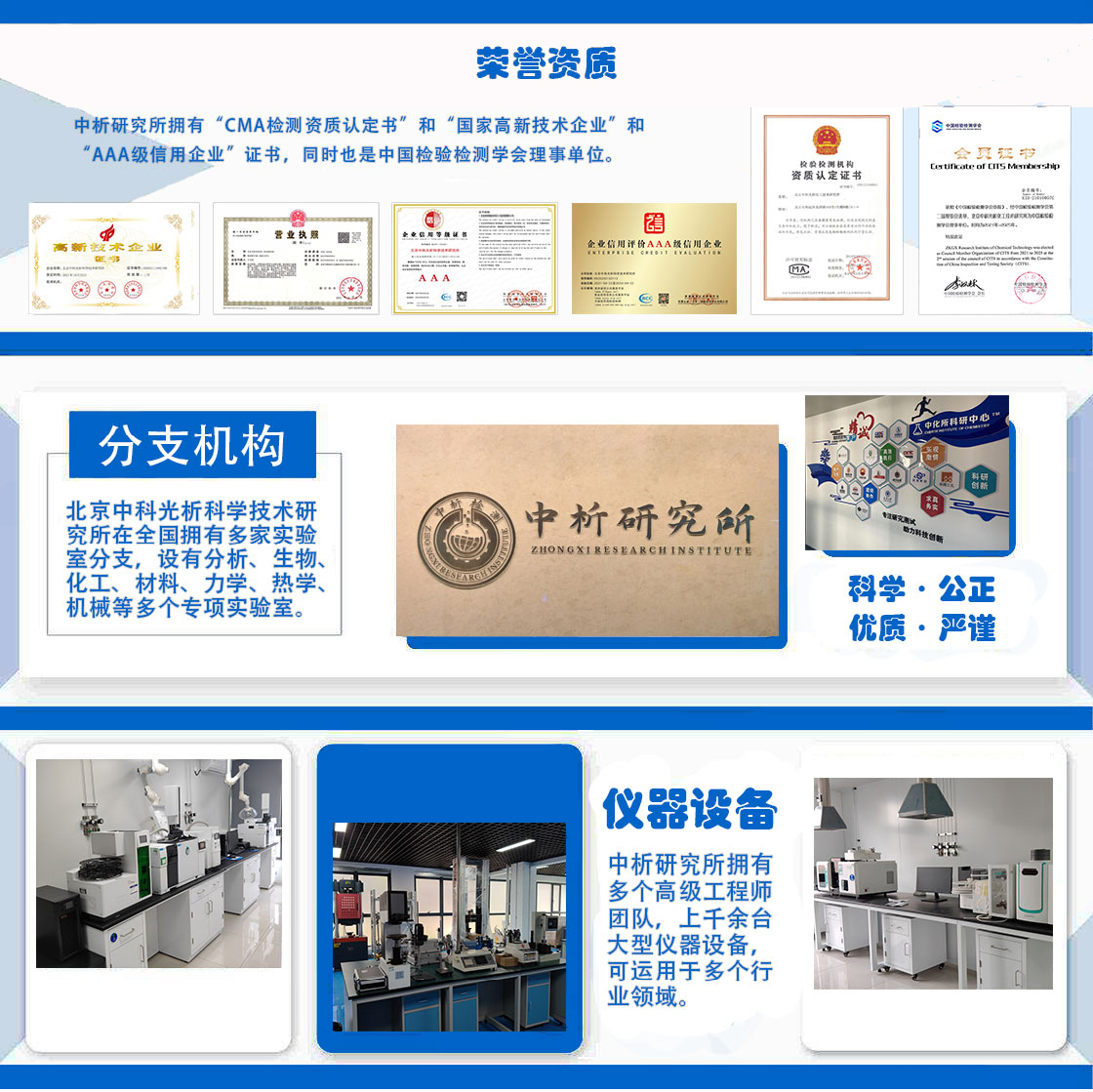
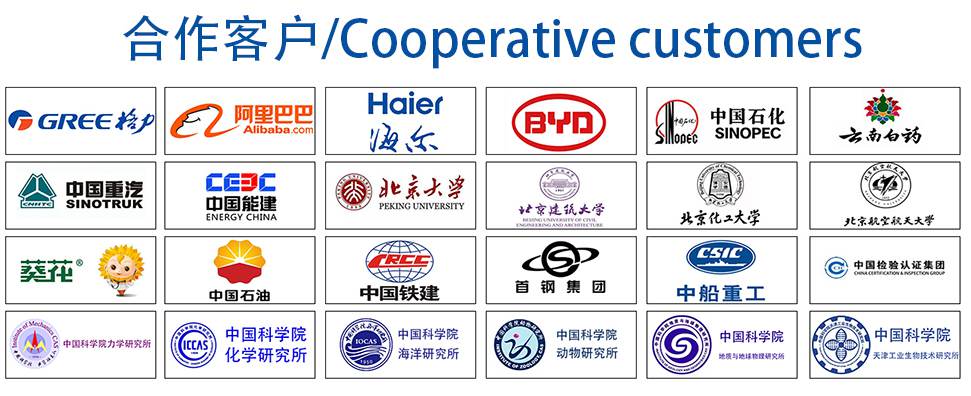