航空机轮和机轮刹车装置检测的重要性
航空机轮及刹车装置是飞机起降系统的核心部件,直接关系到飞行安全、着陆稳定性和运行效率。作为飞机与地面接触的载体,机轮需承受高速摩擦、极端温度变化和巨大冲击载荷,而刹车装置则需在短时间内吸收并耗散动能,确保飞机在有限跑道距离内安全停止。因此,针对航空机轮和刹车装置的定期检测与性能评估至关重要。国际航空管理机构(如FAA、EASA)和制造商均制定了严格的技术规范,涵盖结构完整性、材料性能、功能可靠性等多维度检测项目。
航空机轮检测核心项目
1. 轮毂与轮胎结构检测:
通过目视检查、渗透探伤(PT)和超声检测(UT)排查裂纹、腐蚀及变形,确保轮毂无结构损伤;轮胎需检测胎面磨损深度、帘线层完整性及胎压稳定性。
2. 动平衡测试:
使用专用设备测量机轮旋转时的振动值,防止因质量分布不均导致高速滚动失衡,影响起降稳定性。
3. 轴承性能验证:
检查轴承润滑状态、游隙公差及旋转阻力,防止过热或卡滞导致机械故障。
4. 耐压与气密性试验:
对轮毂进行静压试验(通常达2倍工作压力)并监测泄漏率,确保无爆裂风险。
机轮刹车装置专项检测
1. 刹车盘热疲劳测试:
模拟多次紧急制动场景,通过热成像仪监测刹车盘表面温度梯度及裂纹扩展趋势,评估耐高温循环能力。
2. 摩擦材料磨损分析:
测量刹车片厚度、均匀性及摩擦系数衰减,确保制动效率符合适航标准(如CCAR-25部要求)。
3. 液压/电传作动系统测试:
检测作动筒响应时间、压力传输效率及密封性,验证刹车指令的实时性与精确度。
4. 防滑控制功能验证:
通过台架试验模拟湿滑跑道工况,检查防滑系统(ABS)对轮速差的调节能力,防止轮胎抱死或失控。
综合检测技术与发展趋势
当前检测技术正结合智能化手段升级,例如利用光纤传感器实时监控刹车温度场分布,或通过机器学习分析振动频谱预测部件寿命。同时,复合材料刹车盘的普及推动了非破坏性检测(如X射线断层扫描)的广泛应用。未来,基于数字孪生的虚拟测试与物理检测结合,将进一步优化检测周期并提升故障预警能力。
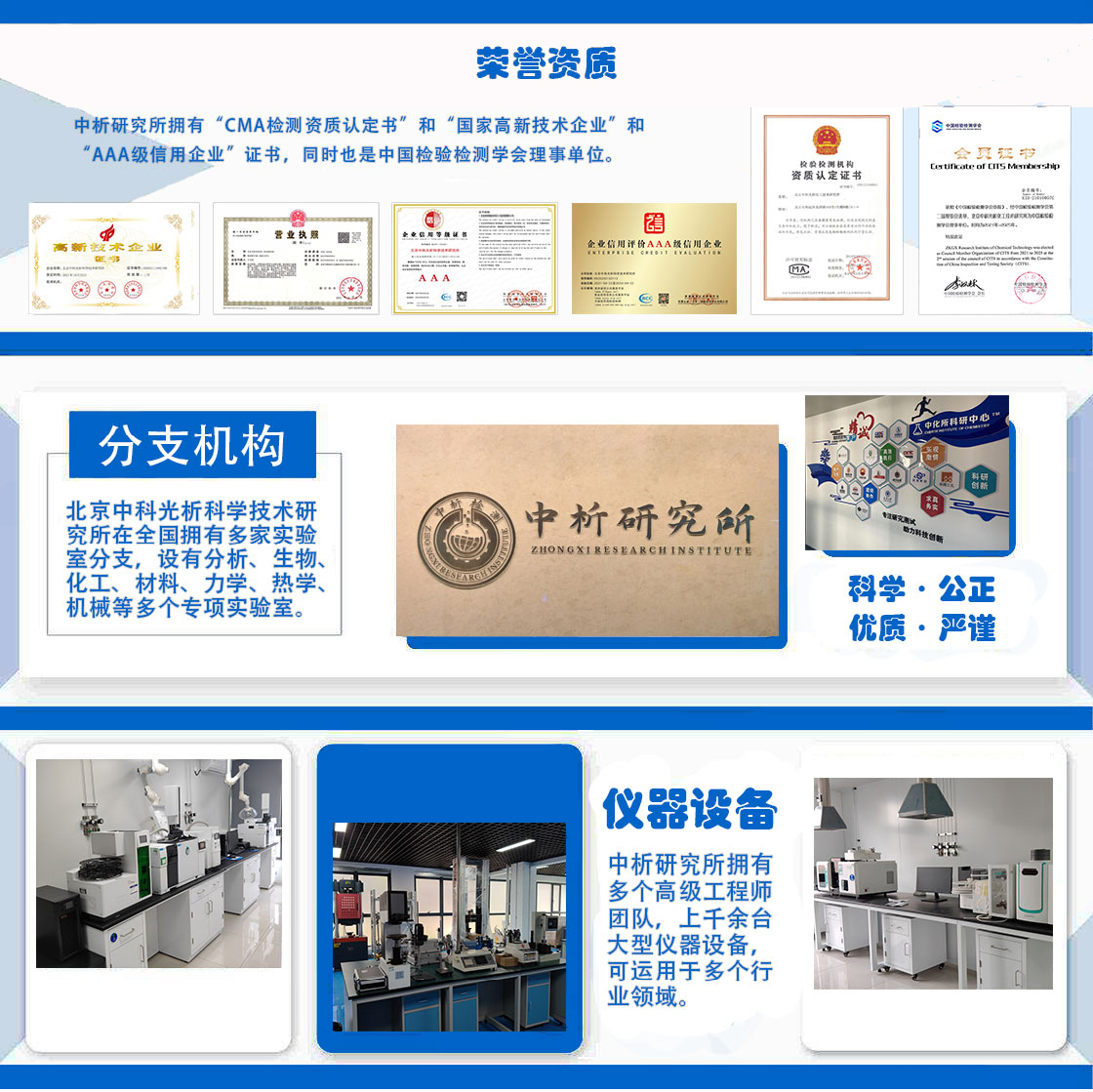
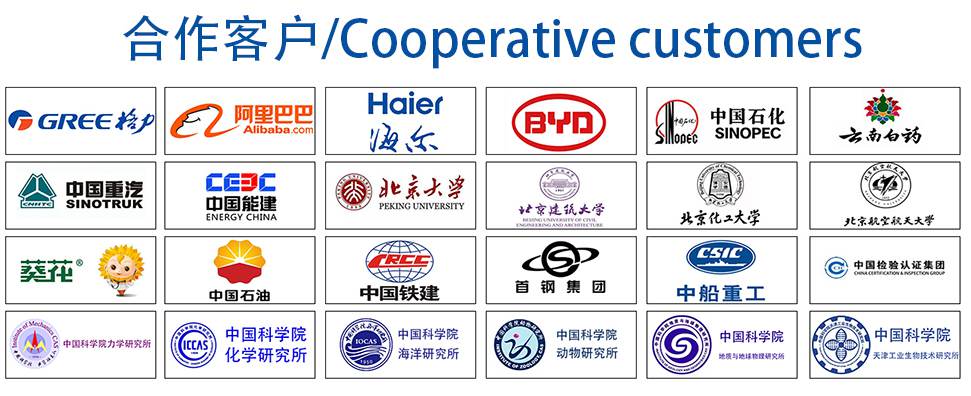