底色漆/清漆涂层体系检测的意义与背景
底色漆/清漆涂层体系作为现代工业中广泛应用的表面处理技术,其性能直接影响产品的耐候性、美观度和使用寿命。该体系通常由底漆、底色漆(提供色彩与金属/珠光效果)和清漆(透明保护层)组成,广泛应用于汽车、航空航天、家电及建筑等领域。检测这一涂层体系的完整性、附着力、耐腐蚀性等关键指标,不仅关乎产品的最终质量,还与安全性和环保要求密切相关。随着材料科学与工艺技术的发展,涂层体系的复杂性日益增加,检测项目也需覆盖更全面的物理性能、化学稳定性和环境适应性,以确保其在极端条件下的可靠性。
核心检测项目及方法
1. 附着力测试
通过划格法(ASTM D3359)、拉开法(ISO 4624)评估涂层与基材及层间结合强度。需重点关注清漆与底色漆界面的附着力,防止因应力变化导致分层或剥落。
2. 耐候性评估
利用QUV紫外线老化试验箱(ASTM G154)、盐雾试验(ASTM B117)模拟长期暴露环境,检测涂层抗黄变、粉化、开裂及腐蚀的能力,尤其关注清漆层的紫外屏蔽效能。
3. 光泽度与表面形貌分析
采用多角度光泽仪(ISO 2813)测量涂层镜面反射率,结合激光共聚焦显微镜观察清漆表面微观结构,确保光泽均匀性及橘皮、流痕等缺陷控制。
4. 硬度与耐磨性测试
通过铅笔硬度法(ASTM D3363)、Taber磨耗试验(ASTM D4060)量化涂层抗划伤和磨损性能,重点验证清漆层对底色漆的机械保护效果。
5. 耐化学腐蚀检测
模拟酸雨(pH 3.5溶液)、溶剂(汽油、机油)等接触场景,评估涂层抗溶胀、褪色及渗透能力,确保清漆层能有效隔绝腐蚀介质。
6. 膜厚与均匀性控制
使用磁性/涡流测厚仪(ISO 2808)精确测量各涂层厚度,结合电镜断面分析验证喷涂工艺稳定性,避免因厚度偏差导致光学效果失真或保护性能下降。
7. 颜色与特效一致性
借助分光光度计(ASTM E308)量化色差(ΔE值),通过多角度观测评估金属/珠光颜料的排列取向,确保批次间颜色匹配及特殊视觉效果再现性。
检测技术的发展趋势
随着智能化检测设备的普及,原位红外光谱、纳米压痕技术逐渐应用于涂层界面分析;大数据平台则通过整合检测数据实现工艺参数优化。未来检测体系将更关注涂层全生命周期的性能预测,以及环保法规对VOC排放、重金属含量的严苛要求。
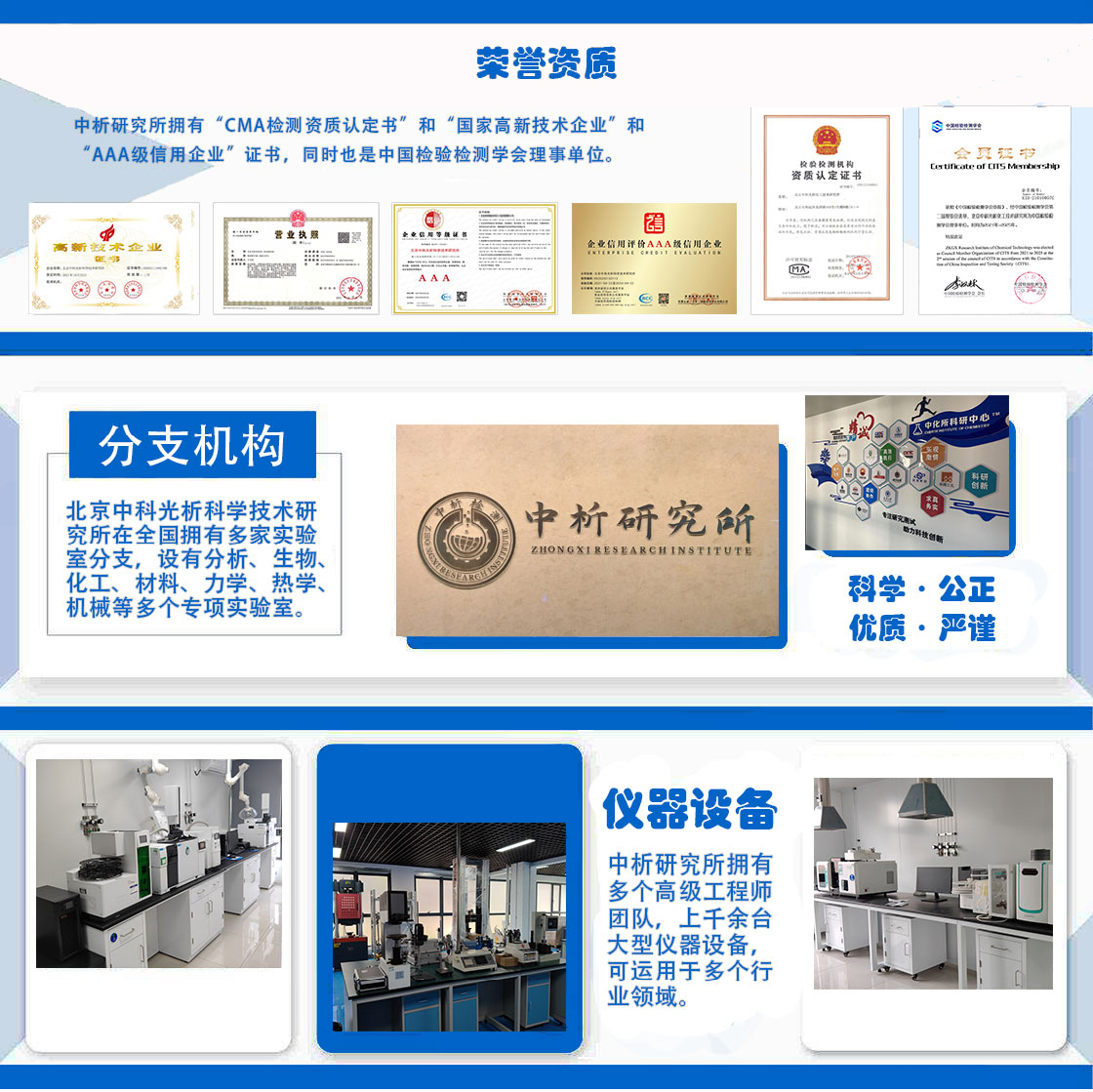
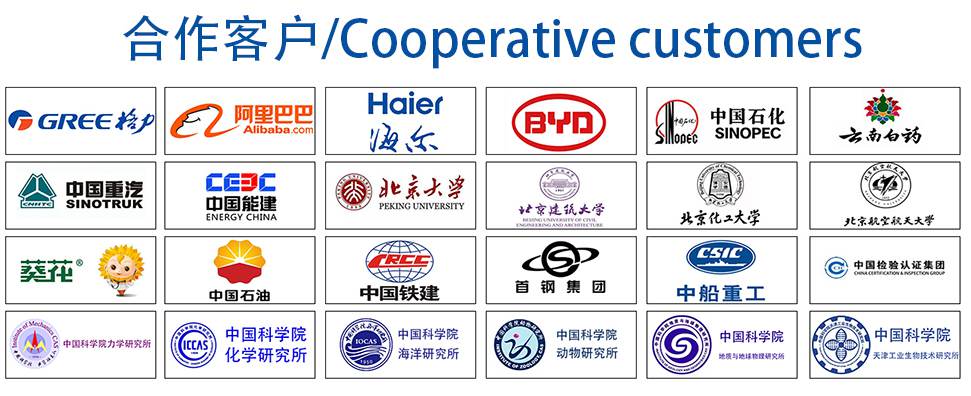