船用车间底漆检测的重要性与核心项目解析
船用车间底漆是船舶建造过程中保护钢材免受腐蚀的第一道防线,其性能直接影响船舶结构的耐久性和安全性。随着国际海事组织(IMO)对船舶涂层标准的日益严格,车间底漆的检测已成为船舶制造、维修及认证中的关键环节。检测项目需覆盖物理性能、化学稳定性、施工适配性等多个维度,以确保底漆在预处理、焊接、切割等工序中仍能维持稳定的防护效果。
1. 附着力检测
附着力是评估车间底漆与钢板结合强度的核心指标。通常采用划格法(ISO 2409)或拉开法(ASTM D4541)进行测试,要求底漆在切割后无明显剥离现象,且剥离面积不超过5%。高附着力的底漆可有效防止后续工序中因机械冲击或热应力导致的涂层脱落。
2. 膜厚均匀性检测
车间底漆的膜厚直接影响防腐蚀寿命。通过磁性测厚仪(ISO 2808)或涡流测厚仪(ASTM B499)多点测量,确保干膜厚度(DFT)控制在15-25μm范围内。膜厚不足会导致防护失效,过厚则可能影响焊接质量和后续涂层的附着力。
3. 耐盐雾性测试
模拟海洋环境的高盐雾条件(ASTM B117),连续暴露500小时后观察锈蚀扩展情况。合格底漆应无气泡、起泡或基材锈蚀,划痕处锈蚀宽度不超过2mm。此项目验证底漆在长期潮湿环境中的稳定性和牺牲阳极保护能力。
4. 耐热性及焊接兼容性测试
通过火焰切割试验(IMO MSC.215(82))和焊接试验检测底漆高温下的表现。要求底漆在1200℃火焰切割后不产生有害烟雾,残留物不影响焊缝质量。焊接区域的底漆碳化层需易清除,且无锌盐析出导致的气孔缺陷。
5. 挥发性有机物(VOC)检测
根据IMO VOC限值及各国环保法规(如GB 30981),采用气相色谱法测定底漆中苯、甲苯、二甲苯等有害物质含量。低VOC配方需满足≤420g/L的标准,同时确保闪点>23℃的施工安全性。
6. 施工性能检测
包括流平性(ASTM D4062)、干燥时间(ISO 9117)和复涂间隔测试。底漆应能在20℃、65%湿度下30分钟内表干,且与环氧、聚氨酯等后续涂层兼容无排斥。喷涂试验需验证无流挂、桔皮等缺陷。
检测环境与标准依据
所有检测需在温度23±2℃、湿度50±5%的恒温恒湿实验室进行,参照ISO 12944-5、PSPC标准及船级社(如CCS、DNV)规范。检测报告应包含样品信息、检测方法、结果数据及与标准的符合性判定,为船舶分段建造提供技术背书。
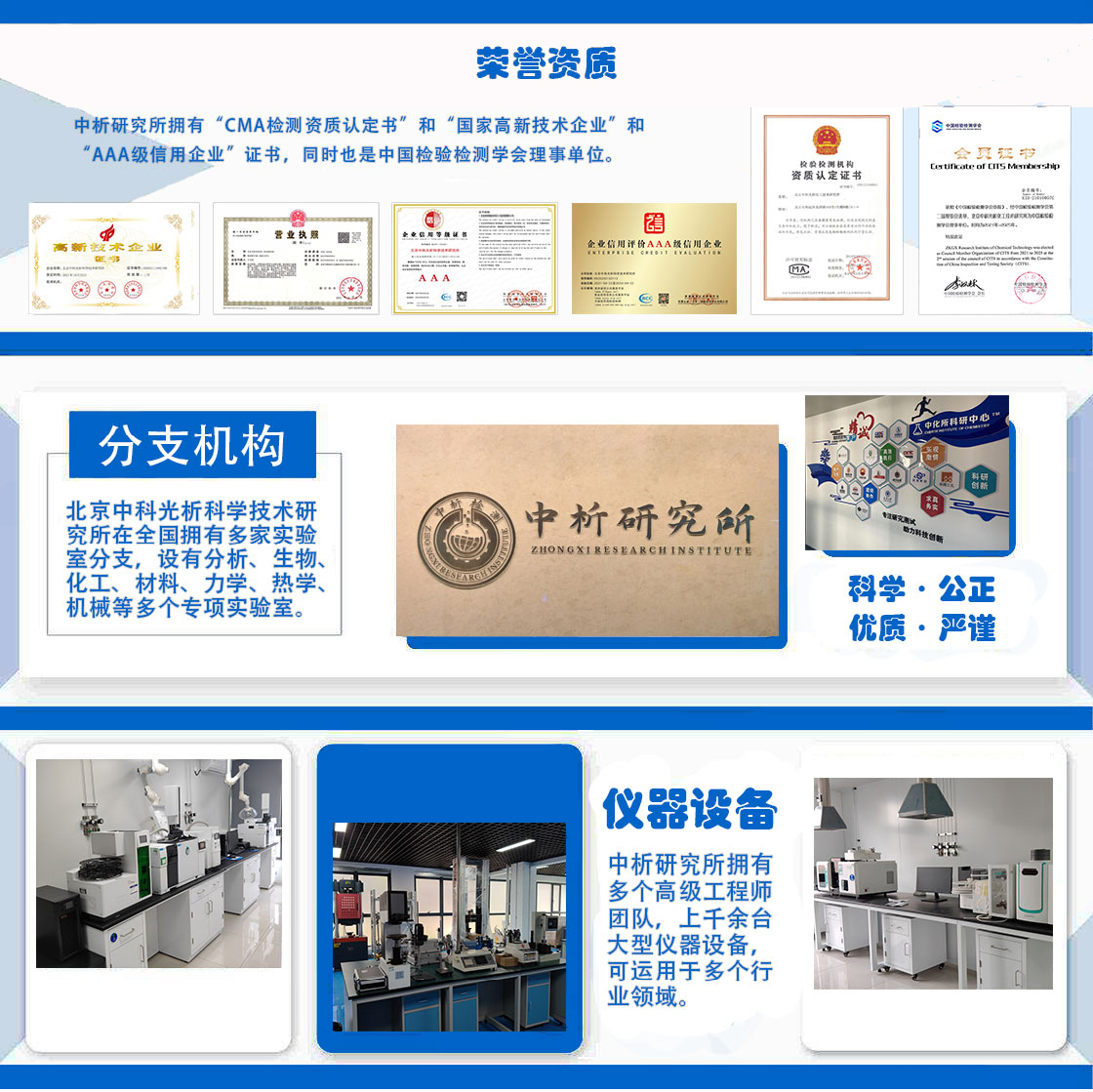
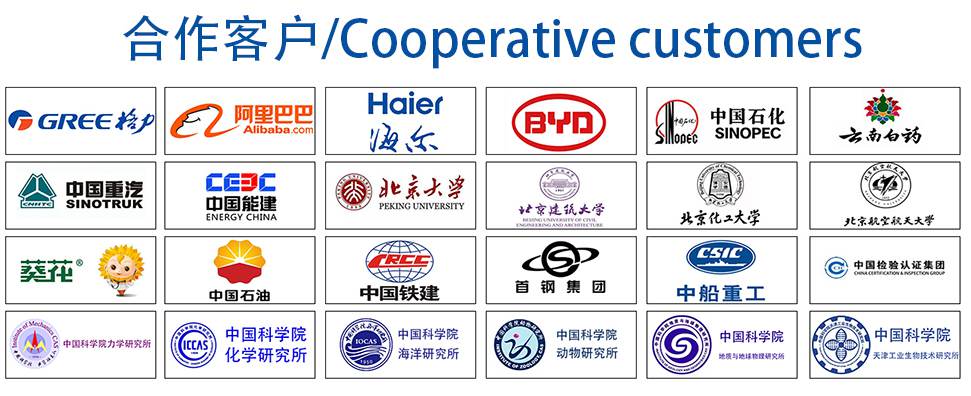