防腐蚀环氧漆检测的重要性与核心项目解析
防腐蚀环氧漆作为一种广泛应用于工业设备、船舶、管道及钢结构等领域的功能性涂料,其性能直接关系到基材的长期抗腐蚀能力和使用寿命。随着工业环境复杂性的提升,对环氧漆的质量要求也日益严格。为确保涂层体系的可靠性和耐久性,科学的检测项目成为生产、施工及验收环节中不可或缺的步骤。通过系统化的检测,不仅能验证涂料的实际性能是否符合设计要求,还能为工程维护提供数据支持,降低因涂层失效导致的安全隐患和经济损失。
核心检测项目及方法
1. 附着力测试
附着力是评价涂层与基材结合强度的关键指标。通常采用划格法(ASTM D3359)或拉开法(ISO 4624)进行测试。划格法通过刀具在涂层表面形成网格切口后,使用胶带剥离观察脱落面积;拉开法则通过专用仪器测量垂直方向剥离涂层所需的力值,结果以MPa表示。
2. 耐化学性检测
环氧漆需抵抗酸、碱、盐、溶剂等介质的侵蚀。实验室模拟环境通常将试板浸泡于特定浓度的化学试剂中(如10%硫酸、5%氢氧化钠溶液),定期观察涂层是否出现起泡、变色或剥落现象,测试周期一般为7-30天。
3. 膜厚检测
使用磁性测厚仪(ISO 2808)或超声波测厚仪测量干膜厚度(DFT)。单点测量需满足设计要求,同时需确保涂层厚度的均匀性,避免过薄导致防腐不足或过厚引发开裂风险。
4. 耐盐雾性能测试
通过盐雾试验箱(ASTM B117)模拟海洋或工业大气环境,连续喷洒5%氯化钠溶液,测试涂层在500-3000小时内的抗腐蚀能力。评估指标包括锈蚀面积、起泡等级及划痕处蔓延程度。
5. 干燥时间与硬度测试
依据ISO 9117标准测定表干和实干时间,确保施工间隔合理。硬度检测常用铅笔硬度法(ASTM D3363)或摆杆硬度计(ISO 1522),数值越高表明涂层抗划伤能力越强。
6. 耐候性加速老化试验
采用QUV紫外老化箱(ASTM G154)或氙灯试验箱(ISO 11341),模拟紫外线、湿度及温度循环对涂层的影响,评估保光率、色差(ΔE≤2为合格)及粉化等级等性能变化。
7. 电绝缘性能检测
针对用于电气设备的环氧漆,需测试体积电阻率(ASTM D257)和介电强度(IEC 60243),确保其在潮湿或污染环境中仍能维持稳定的绝缘特性。
8. 环保与安全指标
检测VOC(挥发性有机物)含量(GB/T 23986)、重金属(铅、铬等)溶出量(GB 30981)及闪点(ISO 3679),满足绿色施工和职业健康安全管理要求。
总结
防腐蚀环氧漆的检测需覆盖物理性能、化学稳定性及环境适应性等多维度指标,严格遵循ISO、ASTM或国标等规范进行操作。建议企业建立从原料入厂到施工验收的全流程检测体系,并结合实际使用环境定制检测方案,以确保涂层在全生命周期内发挥最优防护效果。
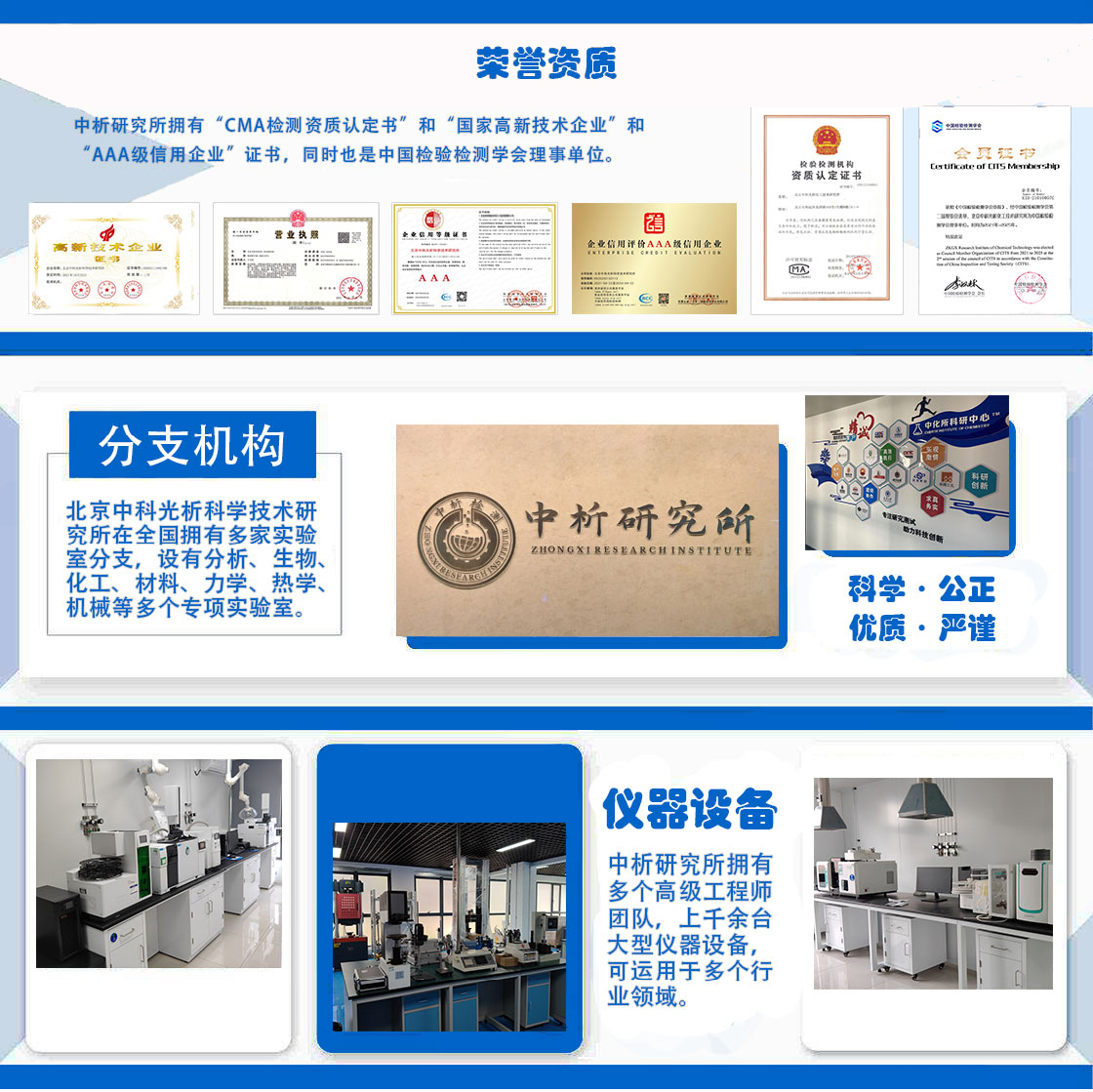
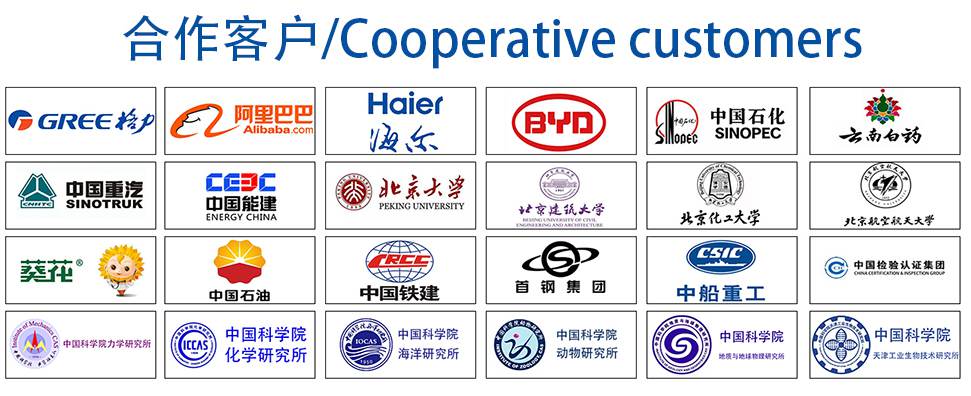