热喷涂涂层检测的重要性与应用背景
热喷涂技术作为一种高效的表面强化和修复工艺,广泛应用于航空航天、能源电力、汽车制造、石油化工等领域。通过将熔融或半熔融的材料高速喷涂到基体表面形成涂层,能够显著提升工件的耐磨、耐腐蚀、隔热等性能。然而,涂层的质量直接影响最终产品的使用寿命和可靠性,因此热喷涂涂层的检测成为生产过程中不可或缺的环节。通过系统性检测,可评估涂层的厚度、结合强度、孔隙率、硬度等关键指标,确保其满足设计要求,避免因涂层失效导致的设备损坏或安全事故。
热喷涂涂层的主要检测项目
热喷涂涂层的检测需覆盖物理性能、力学性能及化学性能等多个维度。以下是核心检测项目及其方法:
1. 涂层厚度检测
涂层厚度是影响防护性能的关键参数。常用检测方法包括:
- 磁性测厚法:适用于磁性基体上的非磁性涂层(如铝涂层)。
- 涡流测厚法:用于非导电基体上的导电涂层测量。
- 金相显微镜法:通过切割试样并观察截面,精度高但属于破坏性检测。
2. 结合强度测试
涂层与基体的结合强度决定其抗剥离能力。检测方法包括:
- 拉伸试验法(ASTM C633):将涂层与标准对偶件粘接后拉伸至断裂,计算结合强度。
- 划痕试验法:通过金刚石压头划擦涂层表面,结合声发射信号判断临界载荷。
3. 孔隙率与致密度分析
涂层中的孔隙会降低耐腐蚀性和力学性能。检测手段包括:
- 金相显微镜分析:通过图像处理软件统计孔隙面积占比。
- 渗透检测(如荧光渗透法):识别贯穿性孔隙。
- 氦气测漏法:高精度检测封闭孔隙率。
4. 显微硬度与耐磨性测试
涂层的硬度直接影响耐磨性能:
- 维氏/努氏显微硬度计:测量涂层截面微区硬度,避免基体干扰。
- 摩擦磨损试验:模拟实际工况,评估涂层耐磨寿命。
5. 化学成分与相结构分析
涂层的成分及相组成影响其综合性能:
- 能谱分析(EDS):检测涂层元素分布。
- X射线衍射(XRD):分析涂层中晶相与非晶相比例。
- 电子探针(EPMA):高精度定位元素分布。
检测标准与质量控制
热喷涂涂层的检测需依据国际或行业标准,如ASTM、ISO、GB/T等。例如:
- ASTM B633:电镀及喷涂层厚度标准;
- ISO 14923:热喷涂涂层孔隙率评估;
- GB/T 8642:热喷涂涂层结合强度试验方法。
企业需结合具体应用场景制定质量控制流程,例如在航空发动机叶片涂层检测中,需增加高温氧化试验和热震试验。
结语
热喷涂涂层的系统性检测是保障其性能稳定性的核心手段。通过多维度检测数据,可优化喷涂工艺参数、改进材料选择,并为涂层失效分析提供依据。未来,随着在线检测技术和人工智能数据分析的应用,涂层质量控制将向智能化、高效化方向持续发展。
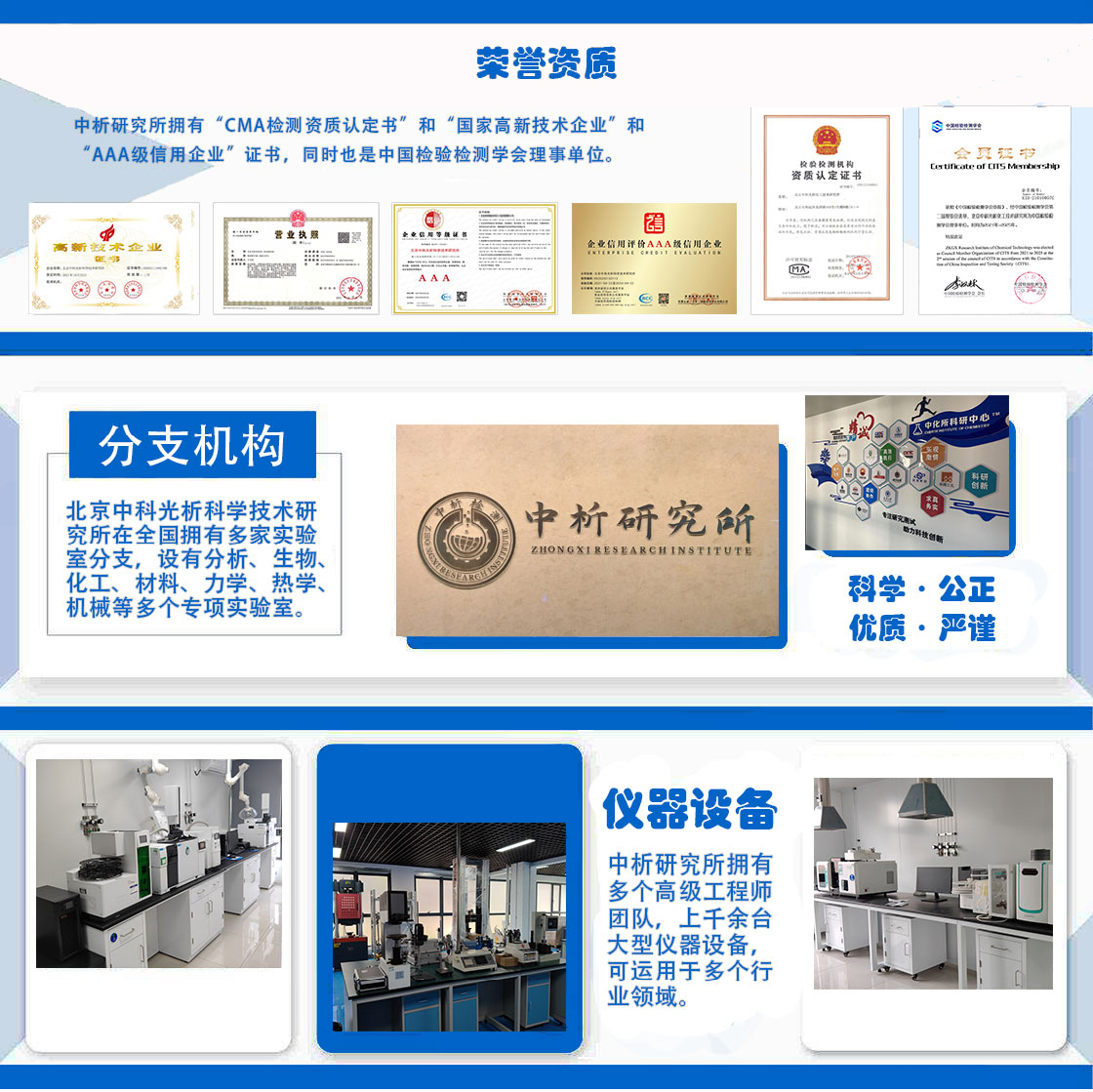
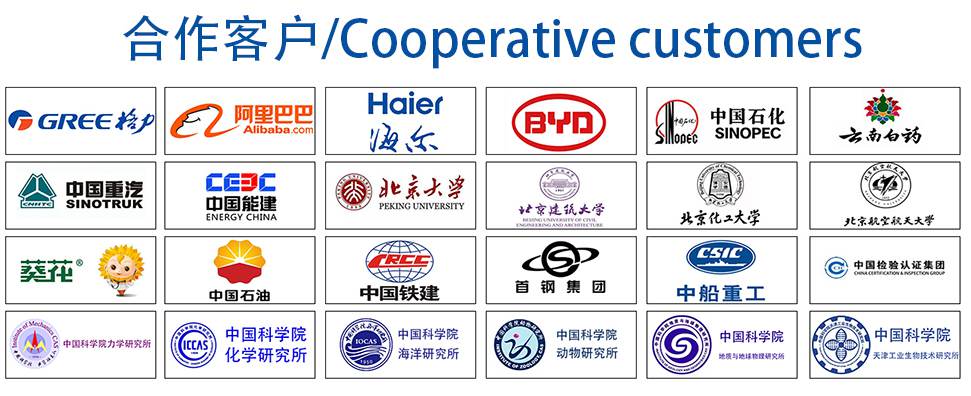