波纹金属软管检测的重要性与关键项目解析
波纹金属软管作为一种柔性连接元件,广泛应用于石油化工、航空航天、机械制造及核能等工业领域。其核心功能是补偿管道系统的位移、吸收振动并适应复杂工况下的压力变化。然而,由于长期承受交变应力、介质腐蚀和机械磨损,软管的安全性成为关键问题。因此,系统化的波纹金属软管检测是确保设备可靠性、避免泄漏事故的核心环节。
外观与尺寸检测
首轮检测需通过目视和测量工具检查软管表面是否存在裂纹、凹陷或焊缝缺陷,同时使用卡尺、投影仪等设备验证波纹节距、波峰波谷高度等尺寸是否符合GB/T 14525-2010标准。此环节能快速发现制造工艺缺陷或运输损伤。
耐压与气密性测试
在液压试验台上,软管需承受1.5倍额定工作压力的静压测试,保压5分钟无渗漏;气密性检测则通过充入惰性气体并监测压力变化,确保密封性能。该测试直接反映软管在高压、脉冲工况下的结构稳定性。
疲劳寿命试验
利用高频疲劳试验机模拟实际工况下的往复运动,记录软管在特定压力、位移下的循环次数。根据ISO 10380标准,合格产品应达到10万次以上循环无泄漏,这对评估软管的动态耐久性至关重要。
材料成分与金相分析
通过光谱仪和电镜对不锈钢层(如316L)、镀层及编织网材料进行成分检测,确保镍、铬等元素含量达标。金相分析可观察晶粒结构是否均匀,避免热处理不当导致的晶间腐蚀风险。
耐腐蚀与环境适应性检测
将样品置于盐雾箱(ASTM B117标准)或酸碱溶液中,模拟极端腐蚀环境,评估表面氧化、点蚀情况。低温试验(-40℃)和高温试验(+300℃)则验证软管在温度骤变时的柔韧性保持能力。
振动与冲击测试
通过振动台模拟设备运行时的机械振动,结合冲击试验检测软管接头是否松动、波纹管是否发生塑性变形。该测试尤其适用于航空航天、车载系统等动态场景的质量验证。
检测流程的标准化意义
完整的波纹金属软管检测需覆盖设计验证、出厂检验及定期维护三个阶段。通过多维度数据采集与对比分析,不仅能预防突发失效,还能优化产品设计,延长使用寿命,为工业安全提供坚实基础。
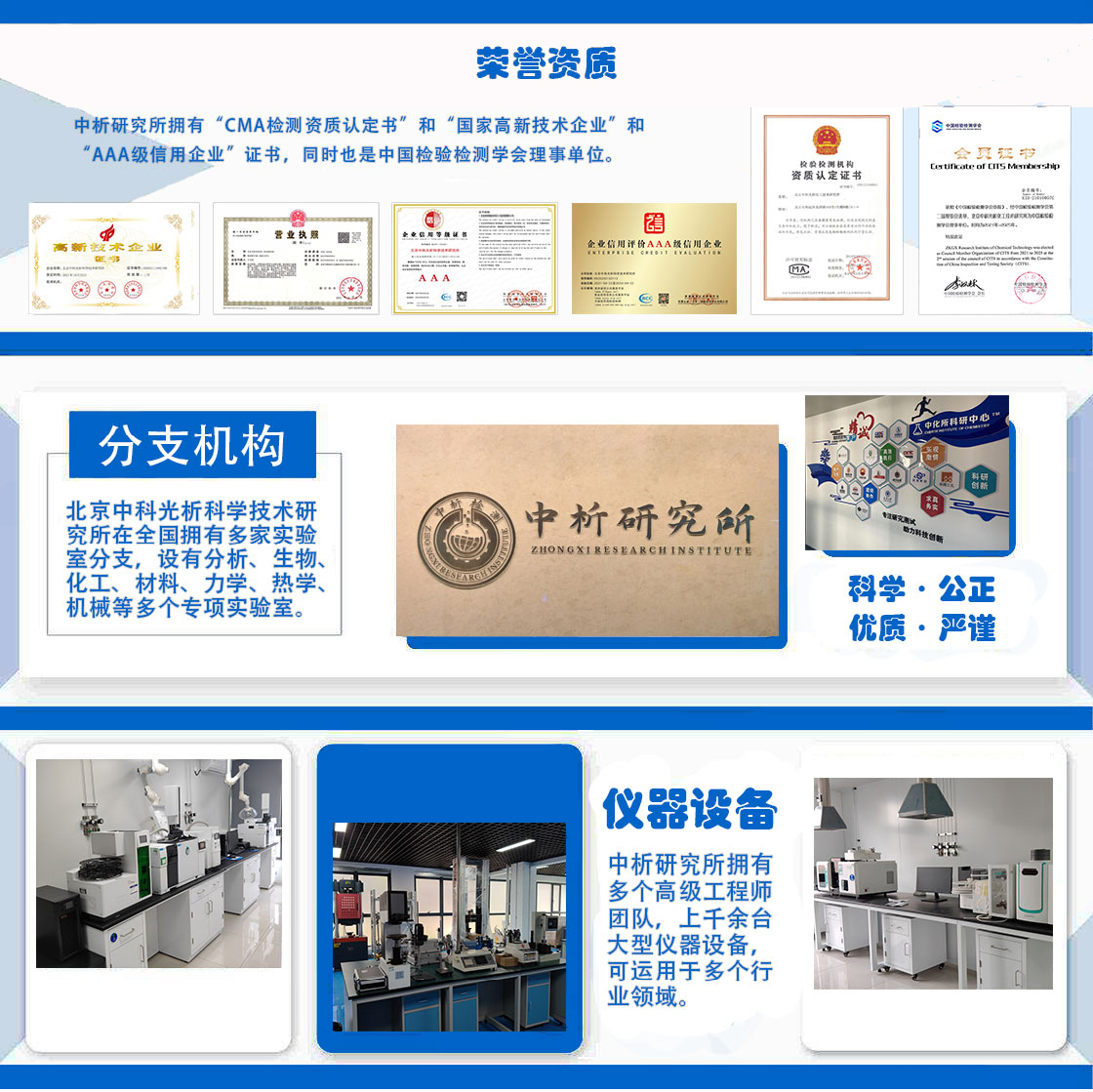
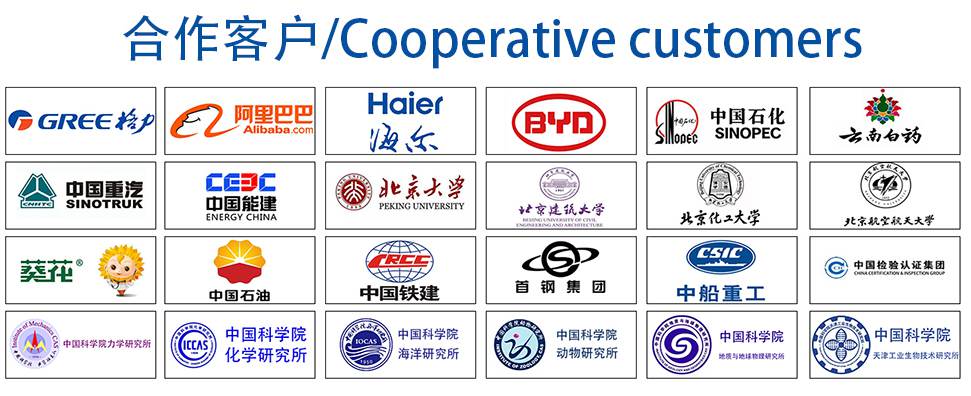