通用结构钢检测:确保材料性能与安全的关键步骤
通用结构钢作为建筑、桥梁、机械制造等领域的核心材料,其性能直接关系到工程的安全性与使用寿命。随着工业技术的发展,结构钢的应用场景日益复杂化,对材料强度、韧性、耐腐蚀性等指标提出了更高要求。为确保钢材质量符合GB/T 700、ASTM A36、EN 10025等国内外标准规范,系统性检测成为从生产到应用全流程中不可或缺的环节。通过科学严谨的检测手段,可有效识别材料缺陷、验证性能参数,从而预防因材料失效引发的重大安全事故。
一、化学成分精准分析
采用电感耦合等离子体发射光谱(ICP-OES)和碳硫分析仪,精确测定C、Si、Mn、P、S等主量元素及微量合金成分。碳含量直接影响钢材的强度和焊接性,硫磷超标会导致热脆性和冷脆性。例如,Q235B钢要求碳含量≤0.20%,硫磷均需控制在0.045%以下。
二、力学性能多维验证
依据GB/T 228.1进行拉伸试验,获取屈服强度、抗拉强度和断后伸长率数据;按GB/T 232执行弯曲试验评估材料塑性;采用夏比冲击试验(GB/T 229)测定-20℃、0℃、室温下的冲击吸收功。某桥梁用钢板要求屈服强度≥345MPa,-20℃冲击功需达到34J以上。
三、无损检测技术体系
超声波检测(UT)可探测内部分层、夹杂等缺陷,检测深度可达300mm;磁粉检测(MT)对表面及近表面裂纹灵敏度达0.1mm;射线检测(RT)主要用于焊缝质量评估,识别未熔合、气孔等典型缺陷。某风电塔筒项目要求全焊缝100%UT+20%RT抽检。
四、几何精度与表面完整性
使用激光测距仪、三维坐标测量机核查钢板厚度偏差(±0.3mm)、平面度(≤3mm/m)等尺寸参数。目视检查结合渗透检测(PT)排查表面裂纹、折叠、结疤等缺陷,确保材料表面质量符合GB/T 14977规定。
五、微观组织解析
通过金相显微镜(100-1000倍)观察显微组织,评估晶粒度(GB/T 6394)、非金属夹杂物(GB/T 10561)等级。某压力容器用钢要求晶粒度≥5级,A类硫化物夹杂不超过2.0级,确保材料具备均匀的力学性能。
六、环境耐受能力评估
盐雾试验(GB/T 10125)模拟海洋大气环境,周期可达2000小时;湿热试验(GB/T 2423.3)验证高温高湿条件下的耐蚀性。某海上平台用钢要求经720h盐雾试验后,腐蚀速率≤0.5mm/a。
七、焊接工艺适配性测试
进行斜Y型坡口焊接裂纹试验(GB/T 4675.1),评估冷裂纹敏感性;通过热影响区最高硬度试验(HV10检测)控制硬度值≤350HV,防止焊接脆化。某重型钢结构项目要求焊缝区-20℃冲击功不低于27J。
综合检测体系通过21项关键指标把控,实现从成分到性能的全维度质量监控。选择具备CMA/ 资质的检测机构,采用符合ISO/IEC 17025标准的检测流程,可确保数据准确可靠。定期检测不仅能避免批次质量问题,更为结构钢的选型应用提供科学依据,有效延长工程结构的使用寿命。
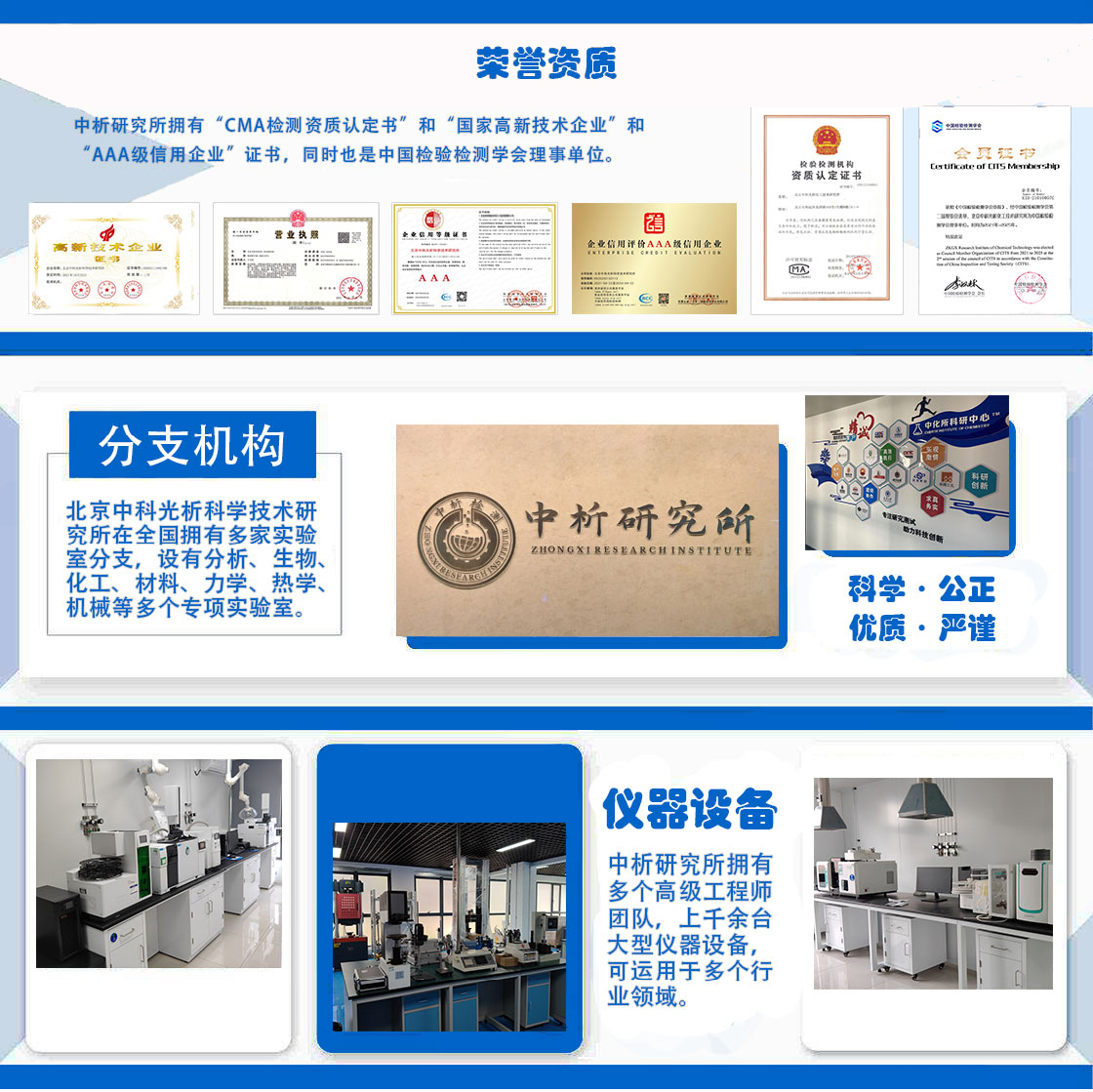
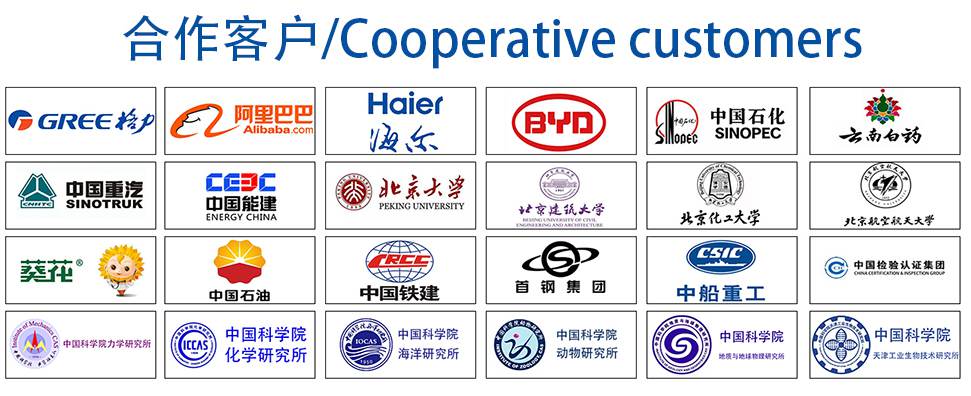