机械连接检测的重要性及行业应用
在机械制造、航空航天、汽车工业等领域,机械连接作为结构承载的核心环节,其可靠性直接关系到整体设备的安全运行。据统计,机械失效案例中约35%源自连接部位的异常,这使得机械连接检测成为质量管控的关键环节。随着现代工业对精密制造要求的提升,检测技术已从传统目视检查发展为涵盖力学性能、材料特性、动态响应等多维度的系统性评估体系。
关键检测项目分类与技术规范
1. 紧固件连接性能检测
采用扭矩测试仪对螺栓/螺母进行预紧力验证,配合超声波应力分析系统可精准测量轴向载荷分布。按ISO 16047标准要求,需对螺纹配合精度、表面硬度(洛氏硬度HRC检测)及防松性能(振动台模拟测试)进行综合评估。
2. 铆接质量无损检测
运用X射线探伤技术检测铆钉内部空隙率,结合数字图像相关法(DIC)分析铆接变形量。航空航天领域需满足NASM 1312-7标准,对铆钉墩头高度、直径公差(±0.1mm)及剪切强度(≥345MPa)进行严格把关。
3. 焊接接头完整性检测
通过相控阵超声检测(PAUT)扫描焊缝熔深,磁粉探伤检测表面裂纹。根据AWS D1.1规范,需进行宏观金相检验(放大100倍观测晶粒度)和显微硬度测试(HV0.5标尺),重点关注热影响区硬度梯度变化。
4. 销轴类连接动态监测
采用三坐标测量仪检测销轴圆柱度(≤0.005mm),配合应变片测量接触应力分布。针对重载设备,需进行50万次疲劳测试(参照ISO 12107),同步监测磨损量变化曲线,确保极限工况下的连接可靠性。
5. 智能化检测技术革新
基于机器视觉的自动定位系统可识别0.02mm级装配偏差,物联网传感器实时监测连接部位温升(精度±1℃)与振动频谱。最新EN 15085-2标准已强制要求关键连接点部署在线监测装置,实现预测性维护。
检测标准体系与实施要点
现代机械连接检测需构建多层级标准体系:基础层执行GB/T 3098系列紧固件标准,进阶层参照ASME PCC-1螺栓连接指南,特殊行业需满足API 6A井口装置等专项规范。检测过程中应特别注意环境补偿(温度补偿系数0.003%/℃)、设备校准周期(扭矩扳手每500次标定)及数据溯源性管理。
随着数字孪生技术的应用,机械连接检测正朝着虚拟验证与实体检测深度融合的方向发展。建议企业建立包含12项核心指标的检测数据库,通过大数据分析优化工艺参数,将连接失效风险降低至0.3%以下,切实保障装备制造质量安全。
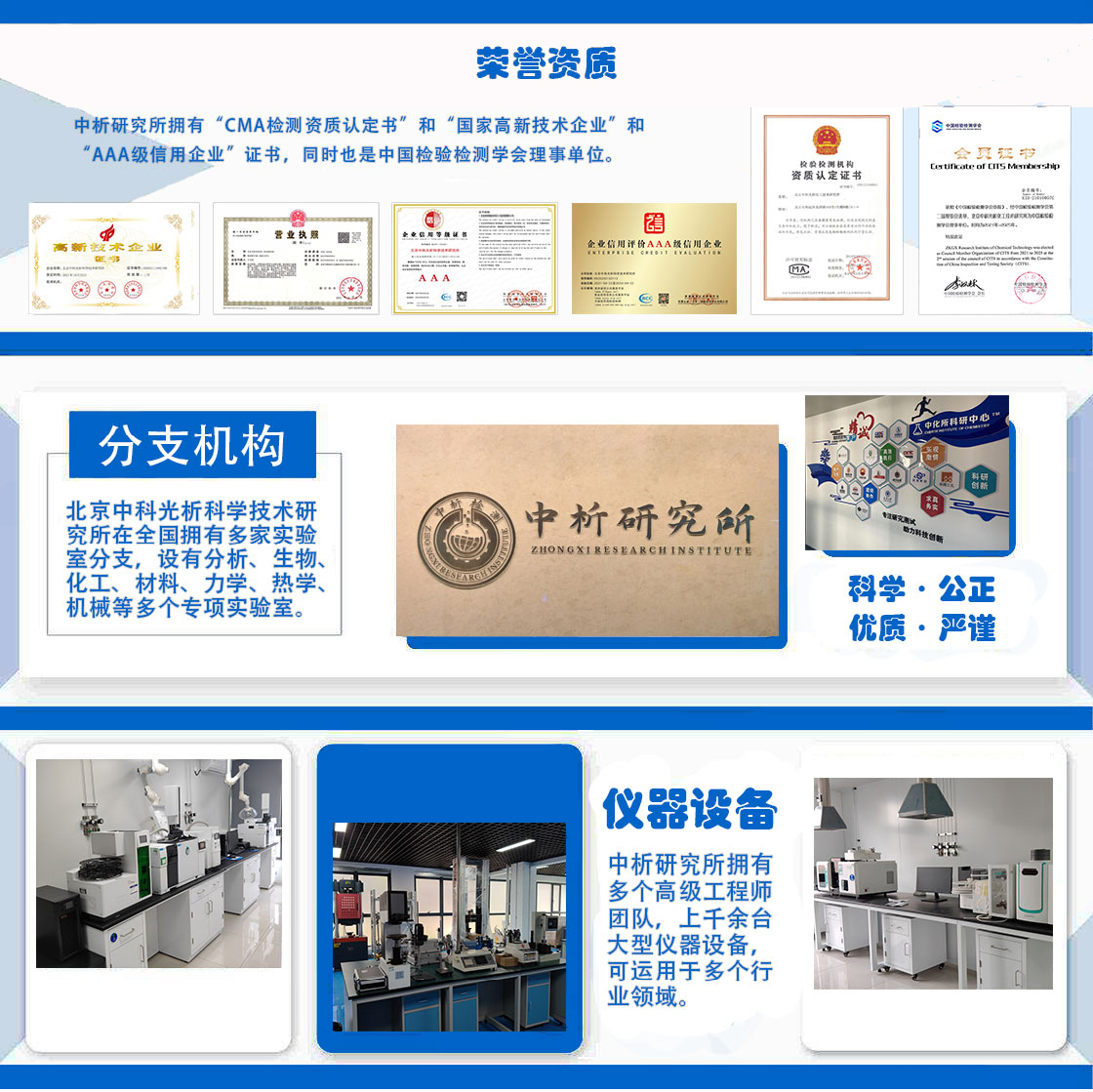
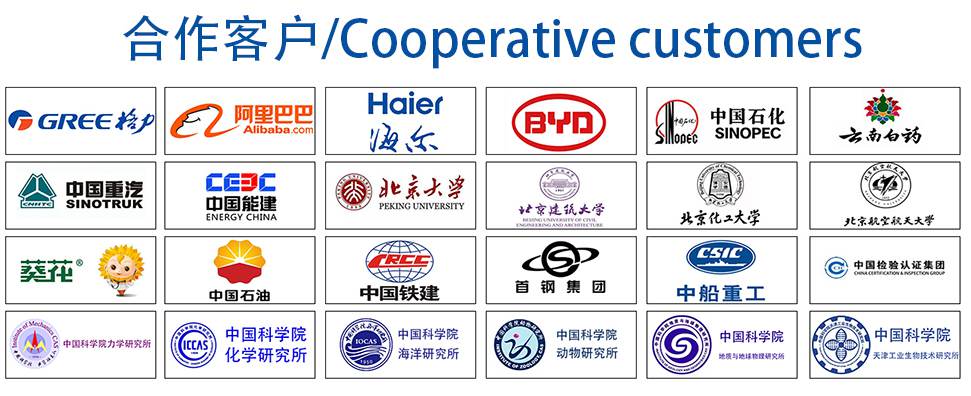