道路车辆-60V和600V单芯电缆热收缩试验检测
引言
随着现代汽车技术的飞速发展,车辆电气系统的复杂性和重要性也日益增加。尤其是在电动汽车和混合动力汽车的日益普及中,电缆系统的可靠性变得至关重要。在这些系统中,60V和600V的单芯电缆被广泛应用,其中涉及跨越电池、电机和各种传感器的连接。这些电缆必须在多种环境下保持稳定的性能,以确保车辆的安全运行。为此,对这些电缆进行热收缩试验检测成为一个重要的环节。
热收缩试验的必要性
在车辆运行过程中,电缆会暴露于高温、振动、化学物质和潮湿等苛刻环境。这要求电缆必须具有高耐久性,能够在恶劣条件下仍然保持其原有的性能。通过热收缩试验,我们可以了解电缆在高温条件下的表现,以确保其在实际使用中不会因为环境变化而失效。
热收缩指的是当电缆暴露于高温环境时,电缆材料因热胀冷缩现象而发生尺寸变化的过程。如果一根电缆的热收缩表现不佳,可能会导致接头松动、信号丢失、绝缘失效等问题,从而引发安全隐患。因此,热收缩试验是保证电缆质量和安全性能的重要手段。
60V和600V电缆的区别
60V和600V电缆在设计和应用上有很大不同。60V电缆通常用于低电压和信号传输系统,例如车内的感应、控制和通讯线路。这些线路对电流的要求较低,绝缘和导体材料也相对简单。然而,这并不意味着它们不需要进行严格的热收缩测试,因为低电压系统中,可靠性和信号稳定性同样至关重要。
另一方面,600V电缆主要用于高电压、大电流传输,如驱动电动机的大功率线路。它们的设计需要承受更高的电气和热应力,因此在绝缘和结构强度上的要求更为严格。在此类电缆的热收缩检测中,任何微小的缺陷都有可能导致高压环境下的快速故障,如短路或火灾。
热收缩试验检测的方法
进行热收缩试验通常需要借助专业的设备,如热缩炉和热像仪。测试的目的是通过控制温度升高的过程,模拟实际环境中的热应力条件,观察电缆在各种高温状态下的长时间性能表现。
首先,务必选择合适的测试电流,确保电缆符合其额定电压等级。然后将电缆暴露于逐渐升高的温度环境中,通常从室温升至120°C乃至150°C。在此过程中,需要连续记录电缆尺寸、形状变化以及表面状态的改变,如是否出现开裂、变色或其他物理变形。
此外,应用热像仪能提供电缆的热分布图像,有助于识别绝缘层内部的热点或潜在缺陷。这一过程需要稳定的操作环境和精确的测量工具,以确保结果的可靠性和可重复性。
影响试验结果的因素
影响热收缩试验结果的因素很多,包括试验设备的校准、环境条件的控制以及电缆本身的生产过程和材料选择。某些高分子绝缘材料对温度的耐受性较差,这可能导致在较低温度下就出现明显的收缩,因此选择合适的材料对于电缆的可靠性非常重要。
同时,电缆的制造工艺也会影响其耐高温能力。例如,在制造过程中如果出现过度的机械拉伸或不均匀挤出,将可能导致在加热时产生应力集中,从而加剧收缩问题。因此,质量控制和过程监测在电缆生产中扮演着不可或缺的角色。
结论
热收缩试验是评估道路车辆电缆可靠性的重要手段,特别是在越来越复杂的汽车电子系统中。通过对60V和600V电缆进行精确的热收缩检测,可以有效预防电气故障的发生,从而保障车辆的安全和性能表现。
未来,随着材料科学和检测技术的不断进步,相信热收缩试验的准确性和效率将会进一步提升,为道路车辆电气系统提供更精准的安全保障。这也是电动汽车和高电压系统可靠性的重要基础,对汽车产业的可持续发展具有积极的推动作用。
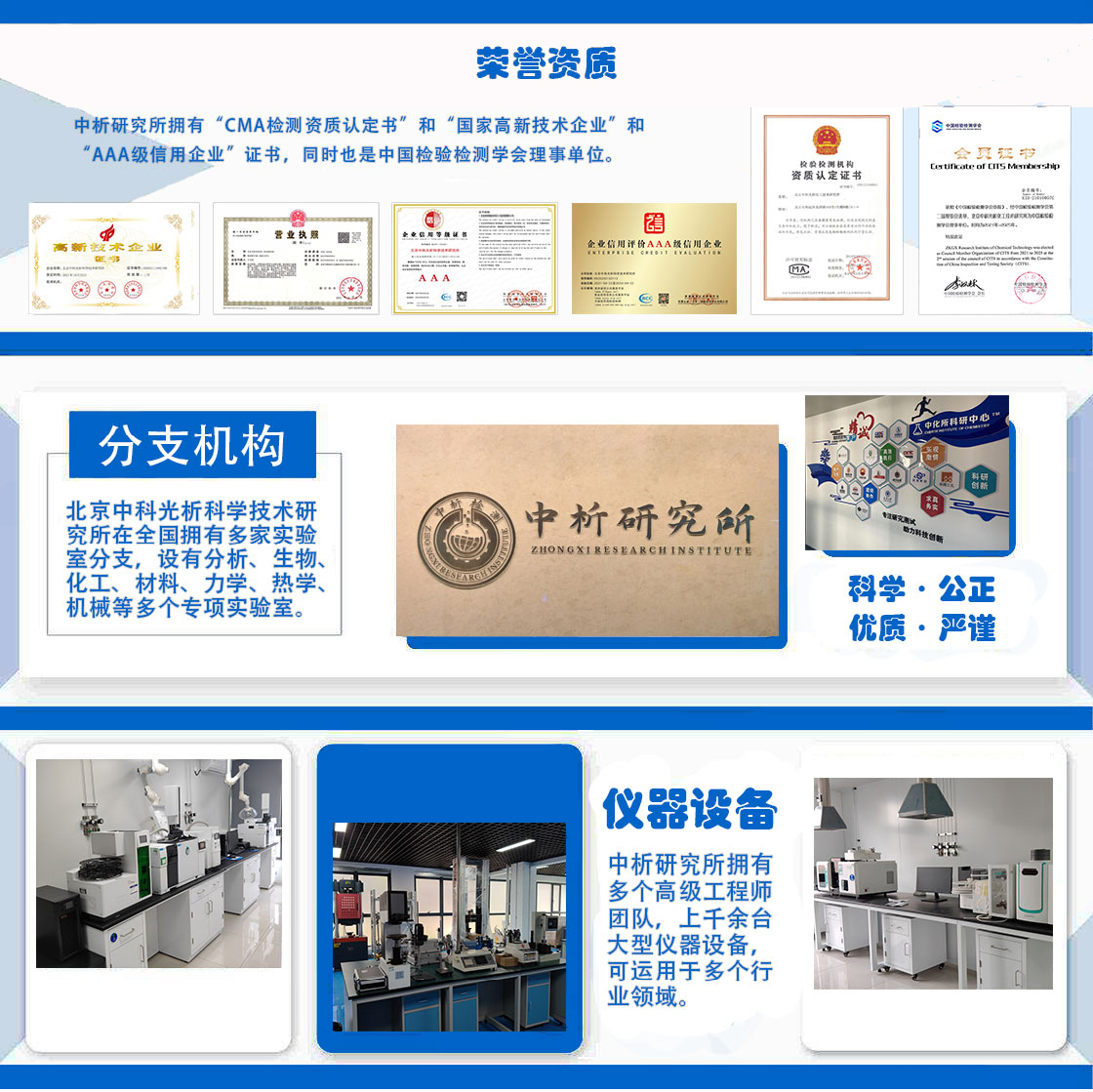
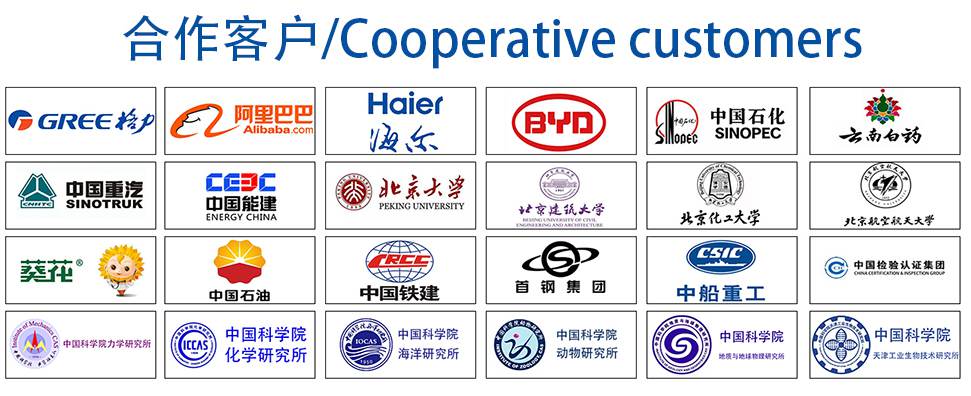