道路车辆-60V和600V单芯电缆长期耐老化 3000h检测
引言
在现代化的交通运输中,道路车辆的电气系统变得越来越复杂和重要。电缆作为车辆中的关键组成部分,负责传输电力和信号,其性能直接影响车辆的安全性和可靠性。尤其是在电动汽车和混合动力汽车的快速普及下,对电缆的要求不断提高。为了确保电缆在车辆整个生命周期中的功能和安全,耐老化测试显得尤为重要。其中,60V和600V单芯电缆是汽车领域常用的规格,本文将详细探讨它们在3000小时耐老化测试中的表现和结果。
电缆耐老化测试的重要性
电缆在车辆中运行时,会受到环境温度、湿度、机械振动和电气负载等多种因素的影响,这些因素会导致电缆材料性能降低,甚至失效。耐老化测试即是在模拟这些环境因素的条件下,对电缆进行长时间的性能考核,评估其在实际条件下的寿命和可靠性。
针对60V和600V电缆的耐老化测试,主要关注的是绝缘层的老化情况、导体的电阻变化以及电缆整体的机械性能。这些指标决定了电缆在实际应用中的耐久性,因此对于评估电缆质量具有重要参考价值。
60V单芯电缆的耐老化测试
60V单芯电缆通常用于低压信号传输或控制系统,它们在车辆电气系统中普遍存在。例如,车载音响系统、照明系统以及其他低压电控模块都可能使用到这类电缆。在进行耐老化测试时,这些电缆通常会置于模拟工作环境中,包括温度循环、湿度变化以及振动冲击。
经过3000小时的测试后,60V电缆的绝缘材料一般呈现出不同程度的硬化或龟裂。因此,测试过程会详细记录绝缘电阻的变化情况,以评估其在长时间服役后的安全性。测试结果通常会与国际标准进行比较,以确定其是否符合行业要求。有些高性能的60V电缆可能会使用改进的材料,提高其耐老化能力,从而在测试中显示出更稳定的性能。
600V单芯电缆的耐老化测试
600V单芯电缆主要用于车辆的主干电路,如动力电池和电机之间的连接,这类电缆需要承载更大的电流和电压,对其绝缘性和导电性要求更高。在耐老化测试中,600V电缆不仅要经过更苛刻的高温和高湿条件测试,还要进行更多次的电气载荷冲击测试。
测试过程中,600V电缆的关键评估项目包括导体的电阻增量、绝缘电阻的变化以及出现的机械损伤。经过3000小时的测试,理想情况下,电缆不应该有显著的导体电阻增加和绝缘失效。但是,若测试中发现电缆性能显著下降,则需要进行材料改进或工艺优化,以提高耐久性。
材料和工艺的影响
电缆材料的选择和制造工艺对电缆的耐老化性能起着决定性作用。在60V和600V电缆的生产中,高质量的绝缘材料比如交联聚乙烯(XLPE)和热塑性塑料被广泛应用,这些材料表现出优良的电气绝缘性能和耐热性。此外,制造工艺中的每一个环节,从挤出到成型,再到冷却过程,都要严格控制,以确保电缆在耐老化方面的优秀表现。
结论
通过对60V和600V单芯电缆进行长达3000小时的耐老化测试,我们可以更好地理解电缆在实际应用中可能面临的问题,从而指导材料选择和生产工艺优化。尽管不同厂家和型号的电缆可能在测试中表现出不一样的特性,但耐老化性能的测试结果对所有电缆产品的长期可信性和安全性评估至关重要。
未来,随着材料科技的发展和工艺的不断创新,道路车辆电缆的耐久性和安全性将会进一步提升,这不仅提升了车辆本身的安全性,也为整个交通运输行业提供更加可靠的电气基础设施。
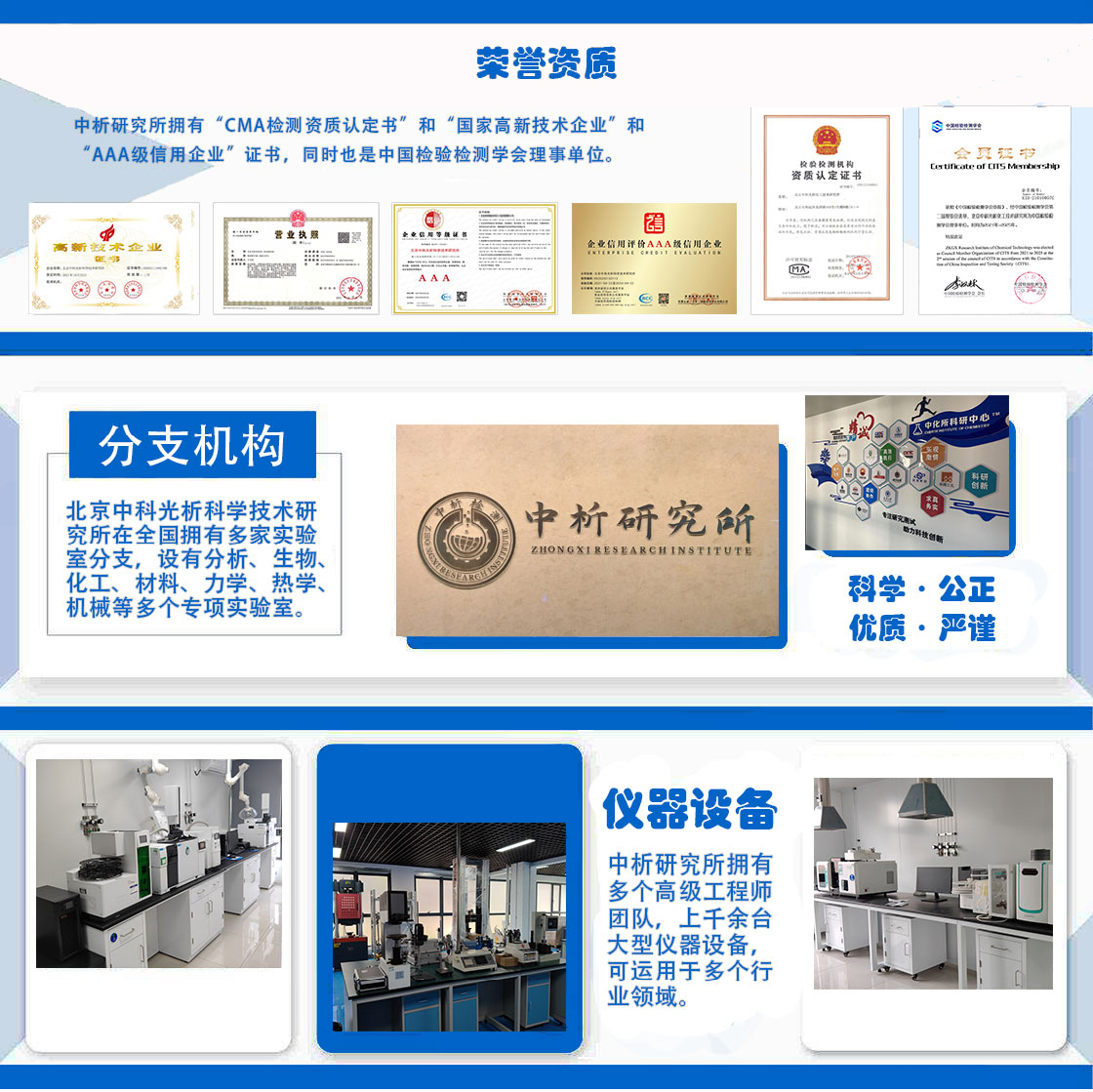
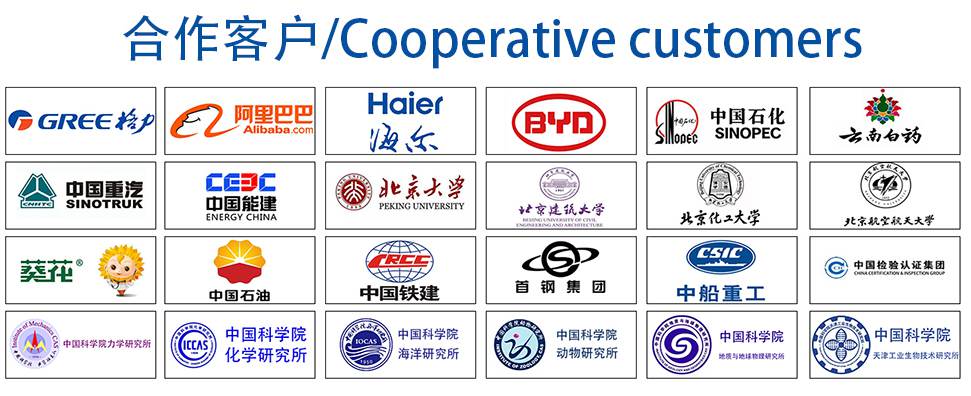