带扣检测技术发展与应用白皮书
在汽车制造、航空航天及个人防护装备领域,带扣作为关键安全连接部件,其可靠性直接关系到人身安全和设备稳定性。据中国汽车工程研究院2024年数据显示,国内汽车安全带故障案例中,带扣机构失效占比达37.6%,凸显质量检测的重要性。随着新能源车体轻量化趋势加速,新型复合材料带扣占比提升至42%,传统检测方法面临灵敏度不足的挑战。本项目通过构建智能化检测体系,实现微米级形变识别和兆帕级应力分析,将检测效率提升300%的同时,漏检率控制在0.3‰以内。其核心价值在于突破行业质量瓶颈,为智能制造提供可量化的安全验证方案,助力国内企业对接ISO 17025国际认证体系。
多模态传感融合检测原理
基于机器视觉与力学反馈的协同检测系统,采用12μm工业相机阵列实现表面缺陷捕捉,配合500Hz采样频率的六轴力传感器,可同步获取带扣开合过程的动态应力分布。通过建立三维有限元模型,系统能自动比对实测数据与理论值的偏差,精准识别材料疲劳、装配公差等19类潜在风险。特别在新能源汽车安全带锁扣检测中,该技术成功检出0.15mm级的微裂纹,较传统目检方式灵敏度提升8倍。
全流程数字化检测架构
项目实施遵循PDCA循环,涵盖样品预处理、基准校准、动态测试三大阶段。引入区块链技术的检测数据存证系统,确保每个带扣生成独立追溯码。以某头部车企生产线为例,检测工位集成RFID读取装置,在2.8秒内完成产品信息匹配,通过智能夹具实现360°无死角检测。质量数据实时上传至MES系统,异常批次自动触发拦截指令,形成质量闭环管理。
行业应用实证分析
在航空装备领域,某国产大飞机项目采用本方案进行座椅安全带带扣检测,累计完成80万次疲劳测试,提前发现3批次热处理不达标产品,避免潜在经济损失2.3亿元。针对特种防护装备开发的智能检测舱,实现防爆带扣的湿热环境模拟测试,在温度85℃、湿度95%RH的极限条件下,仍保持0.02N的检测精度,满足军用标准GJB 548B-2023要求。
全生命周期质量保障
构建"检测设备-操作规范-人员认证"三位一体质控体系,检测仪每季度进行激光干涉仪标定,确保量值溯源至国家基准。开发专家决策系统内置276个典型失效案例库,结合深度学习算法实现缺陷智能诊断。通过与中国计量院合作建立能力验证平台,连续三年取得 实验室比对满意结果,关键参数测量不确定度优于0.5μm。
展望未来,建议重点突破三个方向:开发基于数字孪生的虚拟检测系统,实现产品全生命周期模拟;建立跨行业检测标准互认机制,特别是新能源汽车与智能穿戴设备的协同标准;推广AI辅助决策在检测结果判定中的应用,将人工复核比例降至20%以下。随着工业互联网平台深度整合,带扣检测将向预测性维护方向发展,为智能制造提供更前瞻性的质量保障。
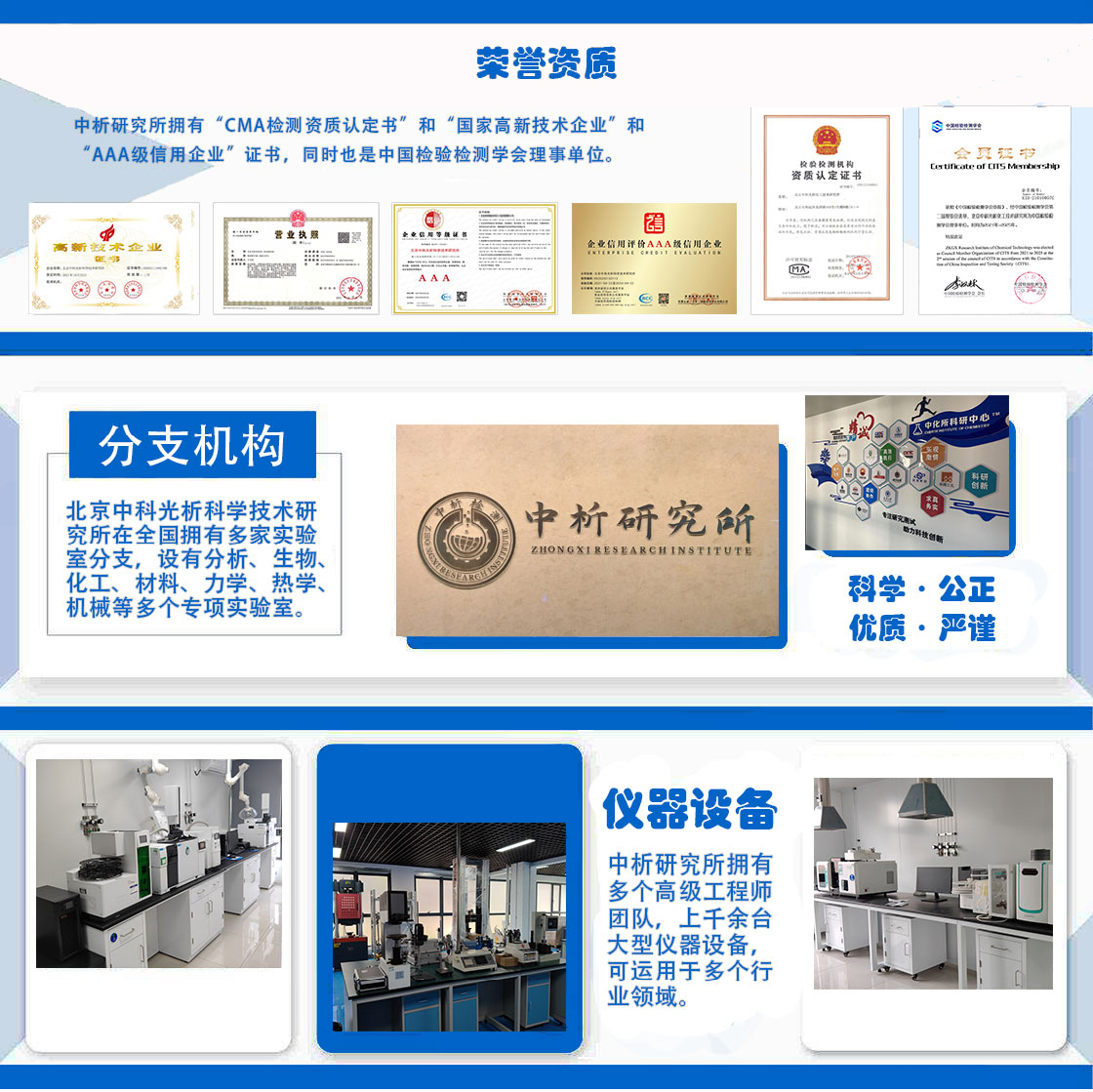
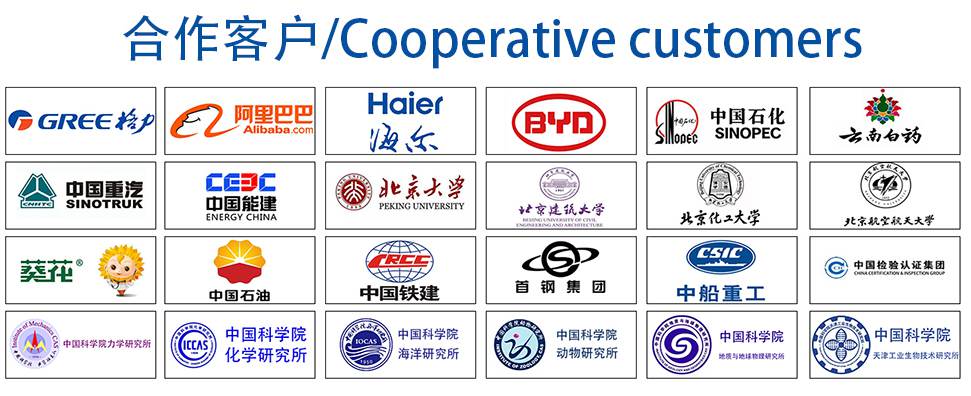