机动车非金属材料及制品检测技术发展与应用白皮书
在汽车产业向轻量化、电动化转型的背景下,机动车非金属材料使用比例已从2015年的32%提升至2023年的48%(中国汽车工业协会数据)。这一趋势推动了包括高分子复合材料、工程塑料、橡胶制品在内的非金属材料检测需求快速增长。机动车非金属材料及制品检测作为保障行车安全、满足环保法规的核心环节,其技术规范直接关系到整车的NVH性能、阻燃安全性和VOC排放水平。通过建立覆盖材料性能、环境耐受性及化学物质析出的全维度检测体系,不仅能够提升供应链质量管理水平,更有助于车企在智能化座舱、新能源电池包等新兴领域实现技术突破。据德勤2024年汽车行业研究报告预测,到2028年汽车非金属检测市场规模将突破82亿美元,其中中国市场份额占比将超过35%。
基于多模态分析的技术原理体系
机动车非金属检测体系融合了材料科学、分析化学与工程力学的交叉技术。针对内饰材料的VOC排放检测,采用热脱附-气相色谱/质谱联用技术(TD-GC/MS),可精准识别包括苯系物、醛酮类在内的13种有害物质。在力学性能评估领域,基于ASTM D638标准的拉伸试验机可同步获取弹性模量、断裂伸长率等关键参数。值得关注的是,新能源汽车电池包阻燃材料测试已形成专用评价体系,UL 94垂直燃烧试验结合极限氧指数法(LOI)可量化材料的自熄特性,据中国汽车技术研究中心2024年报告显示,国内主流电池企业的阻燃材料检测通过率已提升至92.7%。
全生命周期质量管理实施流程
完整的检测流程分为四个阶段:预处理阶段依据ISO 291标准进行温湿度调节;实验室检测阶段通过自动化设备集群完成物理化学性能测试;数据分析阶段采用AI算法进行异常值筛查和趋势预测;报告生成阶段嵌入区块链技术确保数据可追溯。在长城汽车某车型仪表盘材料检测项目中,该流程将检测周期缩短40%,同时通过建立材料指纹数据库,使供应商质量问题追溯准确率达到99.3%。
行业典型应用场景解析
在新能源汽车领域,蔚来ET5车型的座椅发泡材料通过动态机械分析(DMA)验证了-40℃至120℃工况下的弹性保持率。传统燃油车方面,一汽大众针对门板密封条开展了累计3000小时的紫外老化测试,有效解决了材料黄变问题。值得关注的是,机动车内饰VOC排放检测已形成"实验室+车载"联动的创新模式,吉利汽车联合SGS建立的实时舱内监测系统,可将甲醛检出灵敏度提升至0.01mg/m³。
标准化质量保障体系建设
行业领先机构已构建三级质量管控网络:一级网络涵盖 、CMA实验室认证体系;二级网络实施检测人员ASTM/ISO双认证机制;三级网络部署智能校准系统,确保设备误差率控制在0.5%以内。上汽集团建立的供应商"检测能力雷达图"评价模型,从设备精度、检测效率等6个维度进行动态评级,使物料批检不合格率下降63%。
面向汽车产业技术变革,建议从三方面完善检测体系:首先加快智能传感技术在在线检测中的应用,其次推动主机厂-检测机构-材料供应商的数据链协同,最后需加强生物基材料、可降解复合材料等新兴领域的标准研制。随着自动驾驶技术发展,未来应重点关注座舱材料光学性能与触控灵敏度的协同检测,为行业高质量发展提供技术支撑。
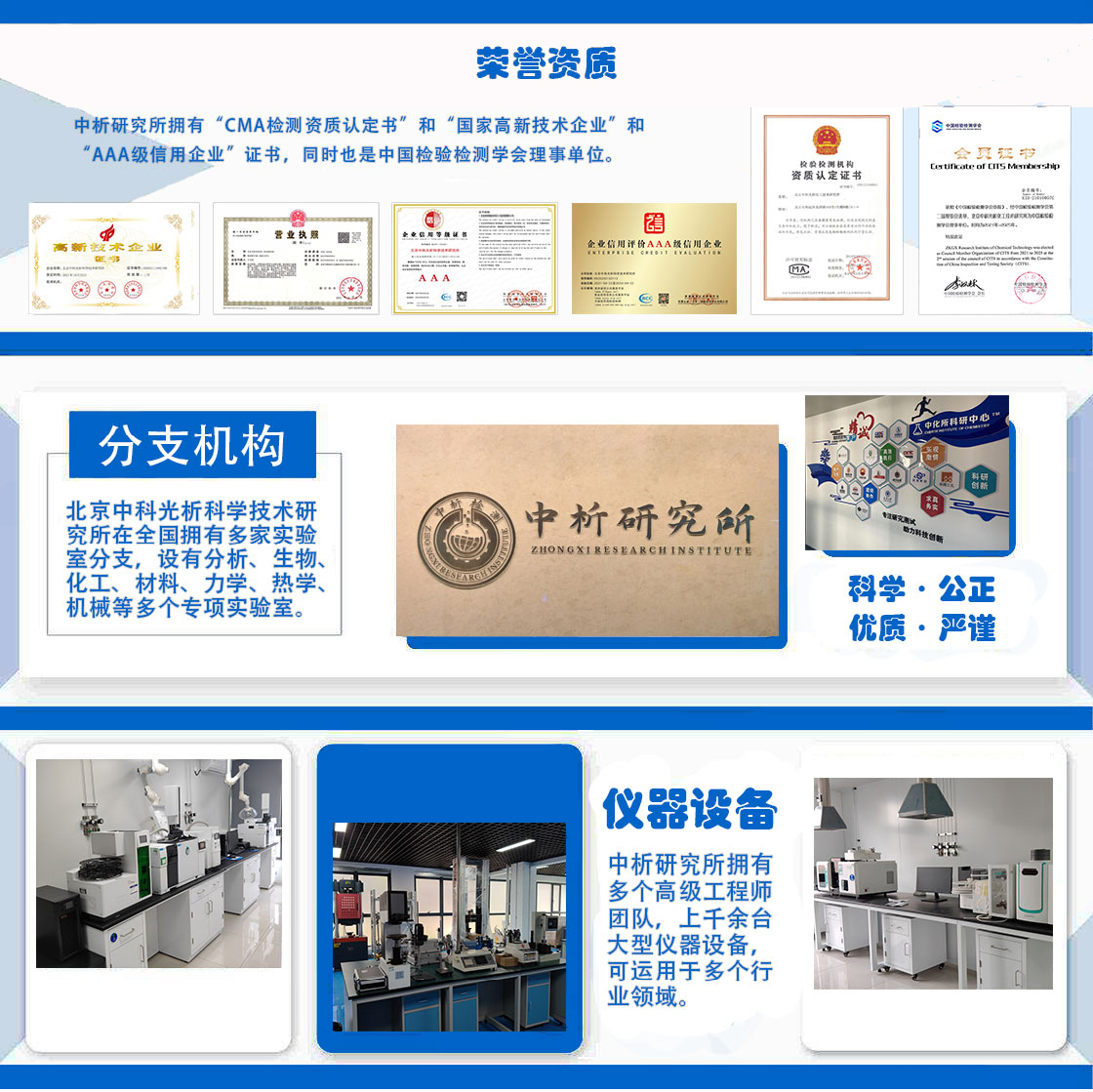
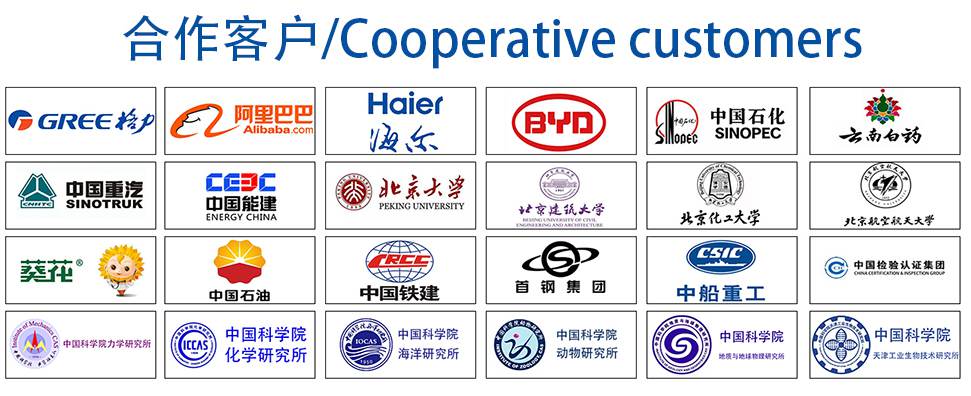