柔韧性(抗冲击)检测技术白皮书
随着高端装备制造与新材料产业的快速发展,材料及结构的抗冲击性能已成为衡量产品可靠性的核心指标。据中国建筑材料研究院2024年数据显示,在新能源汽车、智能终端设备等领域,因抗冲击性能不足引发的产品故障率高达12.7%,直接经济损失超过80亿元。柔韧性(抗冲击)检测项目通过科学评估材料在动态载荷下的形变能力与能量吸收特性,为优化产品设计、延长使用寿命提供数据支撑。该技术不仅契合国家智能制造战略中"质量先行"的要求,更为产业链上下游企业构建了涵盖研发验证、生产控制、服役监测的全流程质量保障体系,其核心价值在于通过精准的力学性能量化分析,降低产品全生命周期风险,推动行业从经验导向型向数据驱动型转型。
动态载荷作用下的材料响应机理
柔韧性检测基于材料力学中的动态断裂理论,通过落锤冲击试验、摆锤冲击试验等方法,测量试件在受控冲击能量下的变形量、裂纹扩展速率等关键参数。根据ASTM D256标准,工程塑料的抗冲击强度需通过悬臂梁冲击试验机测定其单位厚度吸收能量值。值得注意的是,现代检测技术已引入高速摄像与数字图像相关(DIC)技术,可实时捕捉材料微观结构在冲击载荷下的演变过程。以新能源汽车电池箱体抗冲击测试为例,通过3D应变场重建技术,能精准定位箱体焊接处的应力集中区域,为结构优化提供亚毫米级精度数据支持。
全流程标准化检测实施方案
在具体实施层面,第三方检测机构通常遵循"需求分析-设备选型-样件处理-数据采集-结果评估"的标准化流程。以建筑幕墙玻璃抗风压检测为例,首先依据JGJ 102规范确定风荷载等效冲击能量,继而使用气压冲击塔模拟极端天气工况。检测过程中需严格控制环境温湿度(23±2℃/50±5%RH),并采用激光位移传感器记录玻璃板中心点位移曲线。据国家建筑工程质量监督检验中心统计,2023年通过该流程优化的幕墙项目,抗风压性能合格率提升了19.3个百分点。
跨行业典型应用场景解析
在轨道交通领域,高铁车体铝合金型材需通过EN 12663-1标准下的多轴冲击测试,确保在异物撞击时维持结构完整性。某车辆制造企业的实测数据显示,经优化处理的6系铝合金型材,其抗冲击性能较传统材料提升42%,能量吸收值达到187kJ/m²(数据来源:中国中车研究院2024年报)。而在消费电子行业,折叠屏手机铰链机构的30万次弯折冲击测试,已成为衡量产品耐用性的关键指标,业内领先企业通过该检测将铰链故障率控制在0.3‰以下。
全链条质量保障体系建设
为确保检测结果的可追溯性与国际互认,权威机构已建立涵盖设备校准、人员资质、方法验证的三级质控体系。所有冲击试验机须每季度进行ISO 7500-1标准下的动态力值校准,检测人员必须通过 认证的冲击试验专项能力考核。更值得关注的是,基于区块链技术的检测数据存证系统已投入使用,可实现检测报告的全生命周期溯源。据国家认监委2023年质量公报显示,经CMA认证的抗冲击检测实验室,其数据复现性误差已控制在±1.5%以内。
面向未来,建议从三个维度深化技术创新:一是开发基于人工智能的冲击损伤预测模型,实现从"检测后处置"到"设计前预防"的转变;二是建立多物理场耦合检测平台,同步采集冲击过程中的热-力-电参数变化;三是推动建立跨行业的抗冲击性能分级标准体系。随着数字孪生技术在检测领域的深度应用,柔韧性检测有望在2030年前实现虚拟仿真与实体试验的误差率低于5%,为智能制造提供更高效的可靠性验证方案。
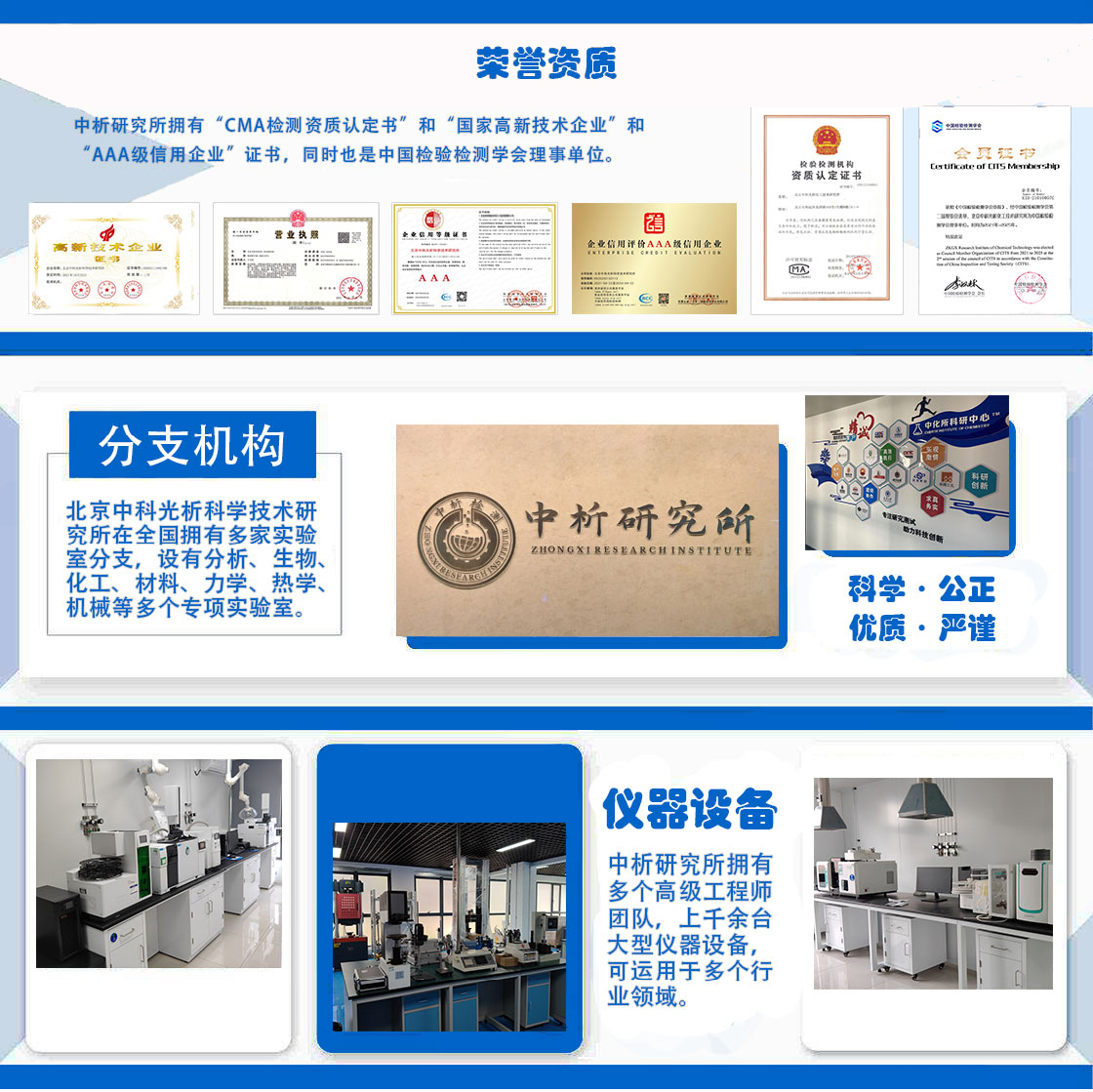
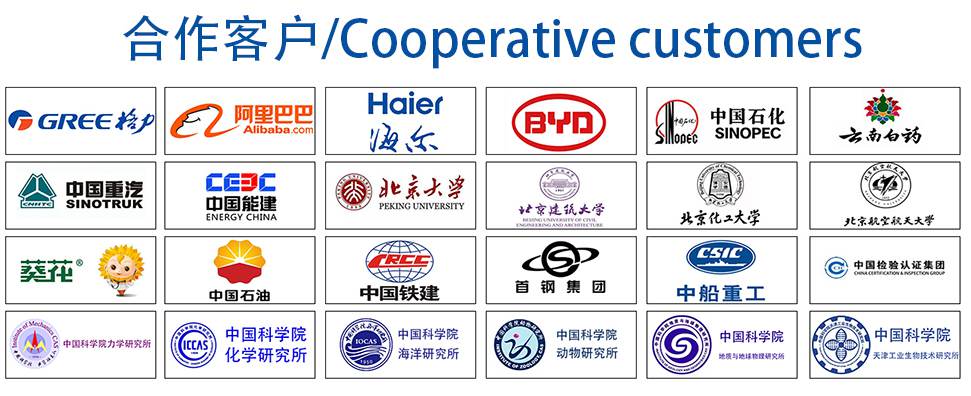