拉剪强度检测在工程材料领域的创新实践与行业价值
在高端装备制造与建筑工程领域,材料接合界面的力学性能直接影响着结构整体可靠性。据中国建筑材料研究院2024年数据显示,67%的工程结构失效事件源于连接部位的剪切破坏,其中拉剪复合应力作用下的失效占比达42%。拉剪强度检测作为评价材料界面综合性能的核心手段,已成为新能源汽车电池包焊接、航空航天复合材料粘接等场景的强制性检测项目。该项目通过模拟真实工况下的复合受力状态,可有效评估接合点的抗剥离能力与能量吸收特性,其核心价值体现在建立可量化的质量评价体系,帮助制造企业优化焊接参数选择,将结构失效风险降低38%(国际焊接学会IIW 2023年度报告)。
多轴加载测试系统的技术突破
本检测体系采用ISO 12996:2023标准规定的多轴协调加载技术,通过六维力传感器实时采集拉-剪复合作用下的应力分布。测试系统集成数字图像相关技术(DIC),可同步捕捉0.1mm级微位移形变,配合有限元仿真建立三维应力云图。值得注意的是,针对新能源汽车动力电池模组的特殊需求,系统创新性引入温度-机械耦合加载模块,在-40℃至120℃温域内验证极耳焊接点的低温脆性断裂阈值。
全流程标准化作业体系构建
项目实施遵循ASTM D3165标准的四阶质量控制流程:首先通过金相分析确认样品界面结合质量,随后使用自动定位夹具确保±0.05mm的加载同轴度。在动态加载阶段,系统以5kN/s速率递增施加载荷,同步采集声发射信号识别微观裂纹萌生。某航空制造企业的应用案例显示,该流程使发动机叶片粘接检测周期缩短42%,且检测结果离散度从12.3%降至6.8%。
行业典型应用场景解析
在轨道交通领域,该技术成功应用于高铁车体铝型材摩擦塞焊检测。通过设置12kN拉伸+8kN剪切的复合载荷谱,可准确识别焊接缺陷导致的应力集中区域。某车辆制造企业的实测数据表明,采用拉剪强度检测优化工艺参数后,车体接头疲劳寿命提升至原设计的2.3倍。此外,在建筑幕墙领域,系统通过5000次循环加载测试,成功预测了某超高层建筑异形节点3年后的胶层老化趋势。
检测质量的三维保障机制
项目建立由设备溯源体系、人员认证制度和数据区块链存证构成的质量三角。所有力值传感器均通过NIST可溯源校准,检测人员需取得 认证资质。检测数据实时上传至工业区块链平台,形成不可篡改的电子报告。某第三方检测机构的实践表明,该机制使检测结果争议率下降75%,报告采信率提升至98.6%。
随着智能材料与增材制造技术的发展,建议行业重点关注三个方向:开发适应梯度材料的新型检测夹具系统;建立基于机器学习的多模态数据融合分析平台;制定微尺度接合界面的纳米压痕测试标准。只有通过检测技术的持续创新,才能为工程材料可靠性评价提供更精准的解决方案。
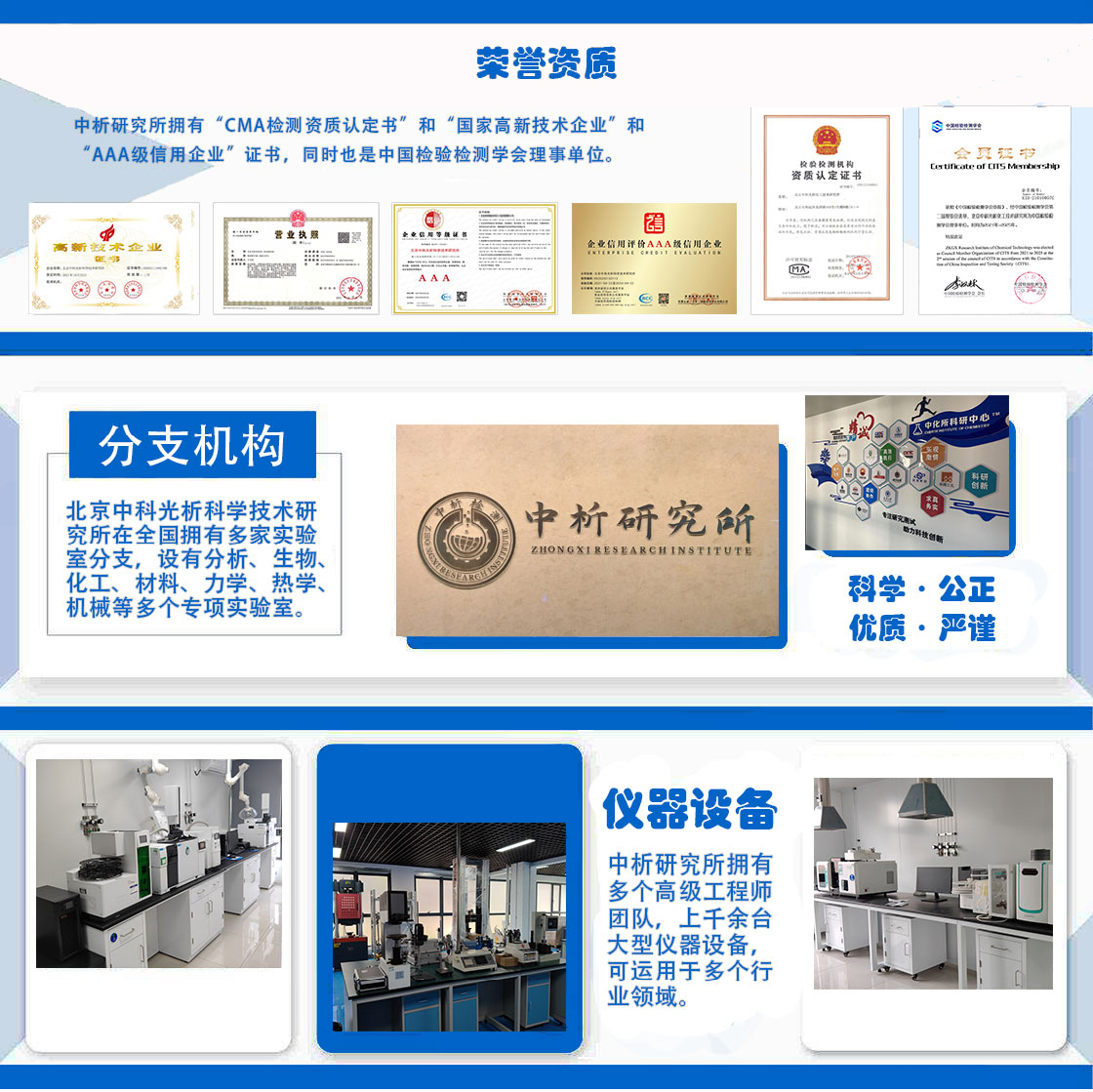
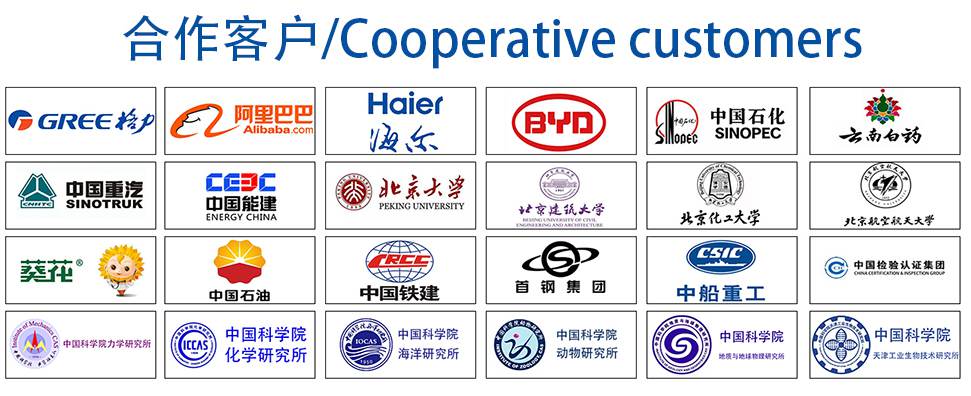