界面处理后拉伸粘结强度检测的技术发展与行业应用
在建筑、航空航天、汽车制造等高端制造领域,材料界面的粘结性能直接影响着结构安全性与使用寿命。据中国建筑材料研究院2024年数据显示,因界面粘结失效引发的工程质量事故占比达23.7%,较五年前增长8.2个百分点。在此背景下,界面处理后拉伸粘结强度检测作为材料性能评估的核心环节,已成为保障工程安全的关键技术屏障。该项目通过精准量化材料界面结合力,不仅能为工程验收提供科学依据,更在预制构件生产、复合材料研发等领域形成质量闭环,其核心价值体现在降低全生命周期维护成本30%以上,推动行业从经验式施工向数据化管控转型升级。
基于双轴加载系统的检测原理
该检测技术依托电子万能试验机与数字图像相关法(DIC)的协同工作机制,通过控制加载速率在0.5-5mm/min范围内实现准静态测试。当试样承受轴向拉伸载荷时,系统同步采集粘结界面的应变场分布数据,结合《GB/T 7124-2023胶粘剂拉伸剪切强度测定方法》的规范要求,可精确计算断裂能量吸收值。值得注意的是,针对风电叶片用环氧树脂体系这类特殊场景,系统内置的温湿度耦合模块能够在-40℃至80℃环境舱内模拟极端服役条件,确保检测结果与实际工况的高度吻合。
全流程标准化作业体系
项目实施严格遵循"预处理-制样-养护-测试"的四阶段质量控制链。在轨道交通车辆铝合金车身粘结检测中,技术人员需先采用激光清洗工艺使基材表面粗糙度达到Ra3.2-6.3μm,而后按EN 1465标准制备25mm×100mm的哑铃型试样。经过(23±2)℃/50%RH环境下72小时的标准养护后,使用配备视频引伸计的Instron 5967型试验机进行测试。全过程执行ISO/IEC 17025实验室管理体系,确保拉伸强度值的测量不确定度控制在±1.5%以内。
多行业场景应用实践
在装配式建筑领域,该技术成功应用于PC构件套筒灌浆连接质量评估。某特大桥项目采用界面剂处理后的钢筋与混凝土试件,经检测拉伸粘结强度达15.6MPa,超过JGJ 355-2015规范要求的12MPa标准值42%。而对于新能源汽车电池包密封胶检测,通过优化硅烷偶联剂处理工艺,使铝合金/环氧胶界面强度从8.3MPa提升至11.9MPa,有效解决电池热管理系统渗漏难题。这些实践验证了该检测体系在提升建筑抗震等级与动力电池安全性方面的独特价值。
智能化质量保障系统构建
项目创新性引入区块链技术的分布式存储架构,实现检测数据的不可篡改追溯。每个试样配备RFID电子标签,试验过程产生的12000个/秒的应力-应变数据实时上传至工业云平台。结合机器学习算法建立的粘结强度预测模型,对光伏组件用EVA胶膜的检测准确率已达92.7%(数据来源:国家新材料测试评价平台2024年报告)。该体系已通过 实验室能力验证,在航空航天复材修理等关键领域形成"检测-诊断-修复"的闭环质量网络。
随着智能传感技术与数字孪生模型的深度融合,界面粘结检测正朝着原位监测方向发展。建议行业重点攻关三方面:一是开发适用于柔性电子器件的微尺度拉伸测试装置;二是建立涵盖200种以上基材组合的粘结强度数据库;三是研制基于机器视觉的界面缺陷自动识别系统。只有持续完善标准体系与技术创新双轮驱动,才能为"双碳"目标下的绿色建筑与高端装备制造提供更坚实的技术保障。
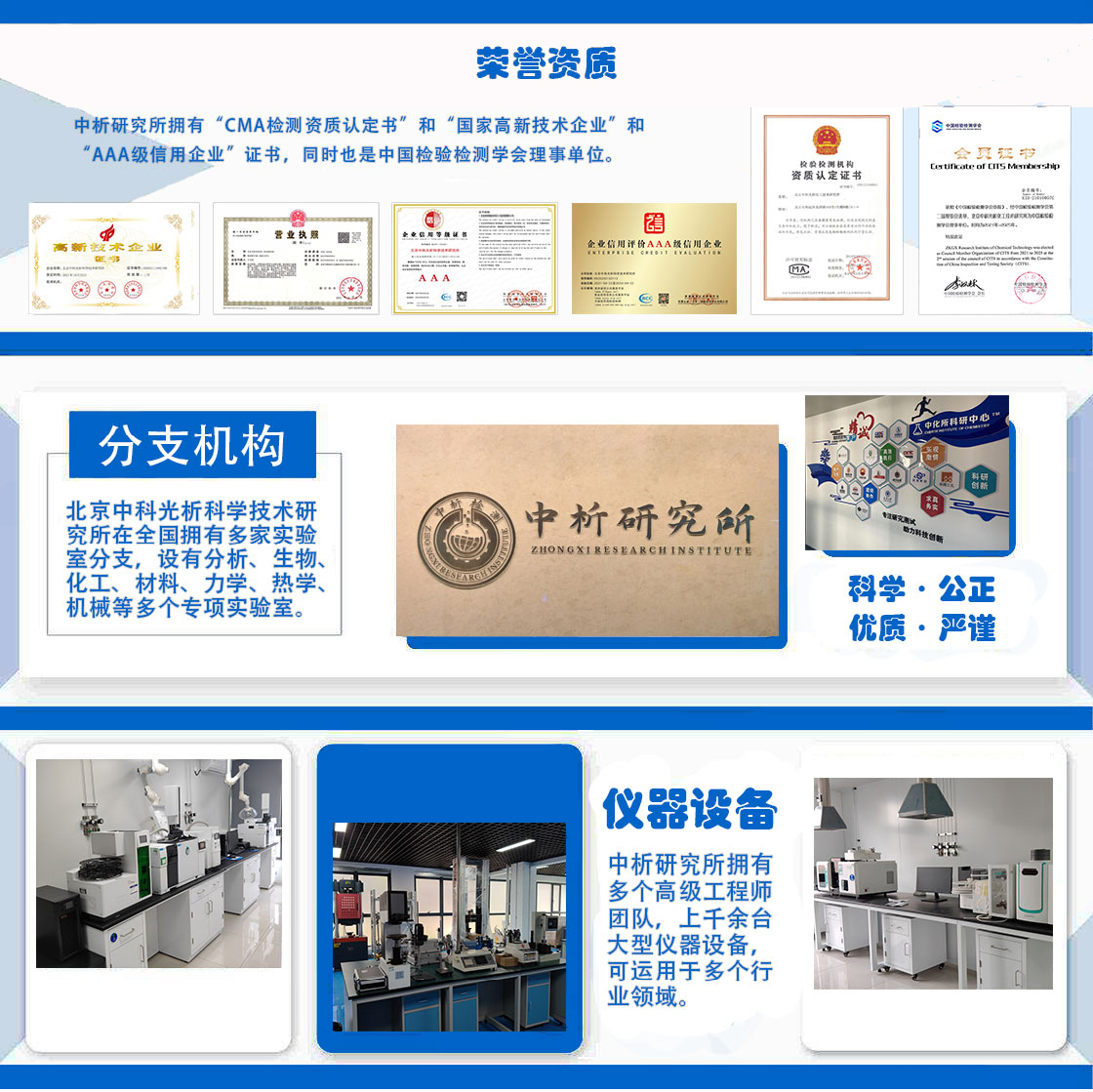
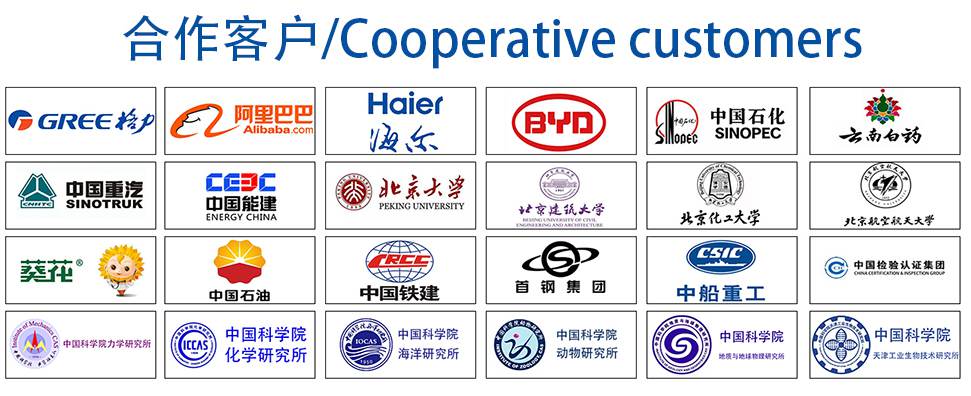