轴承钢检测的重要性与核心项目解析
轴承钢作为制造滚动轴承、精密零部件及高负荷机械装备的关键材料,其性能直接影响设备的运行寿命和可靠性。由于轴承在运转中需承受高频交变应力、摩擦磨损及复杂工况,对材料的纯净度、硬度、韧性等指标要求极为严苛。因此,轴承钢的检测是确保产品质量、避免早期失效的核心环节。通过科学系统的检测项目,可精准评估材料是否符合国家标准(如GB/T 18254-2016)或国际规范(如ASTM A295),从而保障轴承在汽车、航空、机床等领域的安全应用。
1. 化学成分分析
轴承钢的化学成分是决定其性能的基础。检测项目包括碳(C)、铬(Cr)、锰(Mn)、硅(Si)等主量元素,以及硫(S)、磷(P)、氧(O)等杂质含量。例如GCr15轴承钢要求碳含量为0.95%-1.05%、铬含量1.40%-1.65%。通过光谱分析仪(OES)或电感耦合等离子体发射光谱(ICP-OES)进行精确测定,确保元素配比满足抗疲劳和耐磨需求。
2. 硬度与力学性能测试
硬度是衡量轴承钢承载能力的重要指标,通常采用洛氏硬度(HRC)或维氏硬度(HV)测试。淬火+低温回火后的轴承钢硬度需达到60-65 HRC。此外,还需通过拉伸试验机检测抗拉强度(≥1800 MPa)和冲击韧性(Akv≥25 J),评估材料在动态载荷下的抗断裂能力。
3. 金相组织分析
通过金相显微镜观察显微组织,包括马氏体形态、残余奥氏体含量及碳化物分布。合格的轴承钢应呈现细针状马氏体,碳化物颗粒细小均匀(尺寸≤0.6μm),残余奥氏体含量控制在3%-8%之间。同时需检测奥氏体晶粒度(通常要求≥8级),晶粒粗大会显著降低疲劳强度。
4. 非金属夹杂物检测
采用ASTM E45或ISO 4967标准,对氧化物(A类)、硫化物(B类)、硅酸盐(C类)和球状氧化物(D类)夹杂物进行评级。优质轴承钢要求夹杂物级别≤1.5级(细系),过高夹杂物会形成应力集中源,导致轴承早期剥落失效。
5. 表面与内部缺陷检测
使用磁粉探伤(MT)或超声波探伤(UT)检测表面裂纹、折叠等缺陷;通过酸浸低倍试验检查内部疏松、偏析。对于高端轴承钢,还需采用扫描电镜(SEM)分析断口形貌,评估缺陷的微观特征及其对性能的影响。
6. 尺寸与形位公差测量
针对轴承套圈、滚子等成品,需使用三坐标测量机(CMM)或光学投影仪检测直径公差(通常要求IT5级)、圆度(≤0.005mm)及表面粗糙度(Ra≤0.2μm)。严格的尺寸控制可确保轴承装配精度与运转平稳性。
通过上述多维度的检测体系,能够全面把控轴承钢从原材料到成品的质量,为高端装备制造提供可靠的材料保障。企业需建立完善的检测流程,结合智能化设备与数字化管理系统,实现检测数据的高效追溯与分析优化。
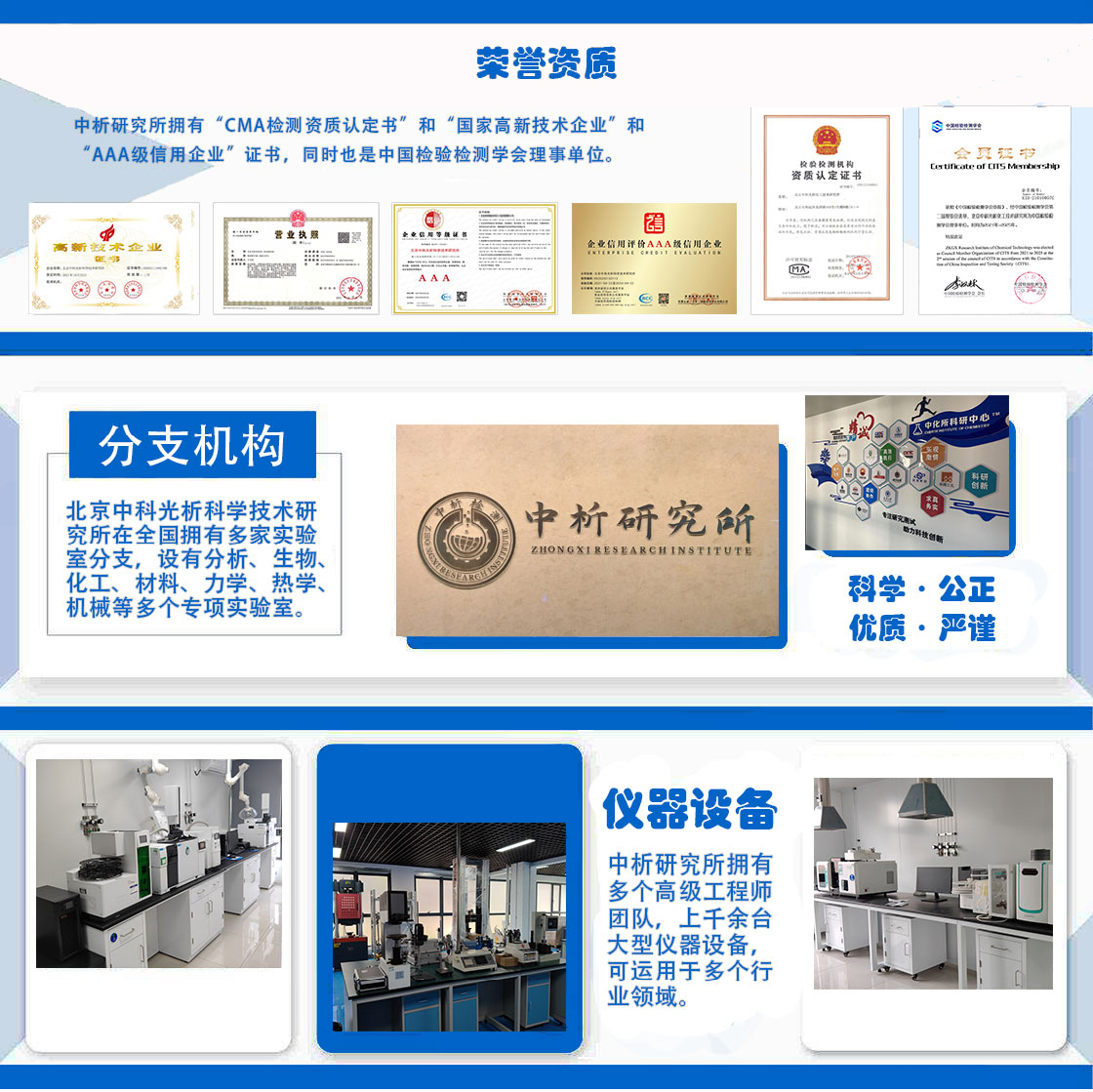
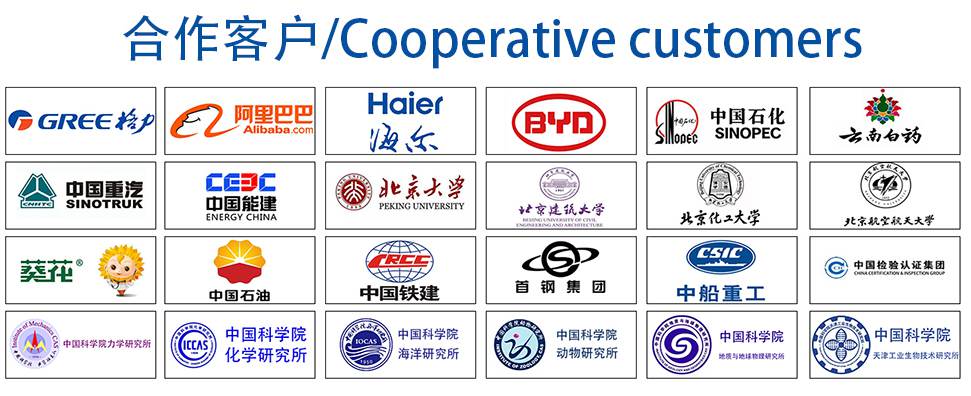