初轧坯和钢坯检测的重要性
在钢铁生产流程中,初轧坯和钢坯作为轧制工艺的关键中间产品,其质量直接决定了后续型材、板材等终轧产品的性能指标。初轧坯是指通过初轧机对钢锭进行开坯加工后形成的矩形或方形截面的半成品,而钢坯则泛指经过连铸或轧制工艺形成的各类断面形状(如方坯、板坯、圆坯)的中间材料。由于这些坯料需要经历高温轧制、冷却等多道工序,其内部组织、表面缺陷、尺寸精度等参数必须经过系统性检测,才能确保成品钢材的力学性能、加工性能及使用寿命符合行业标准要求。
核心检测项目及技术方法
1. 化学成分分析
采用光谱分析仪对坯料进行元素含量检测,重点监控C、Mn、Si、S、P等主量元素及微量合金元素的配比是否符合钢种要求。通过钻孔取样或表面直读技术,确保材料成分均匀性满足GB/T 223系列标准。
2. 表面质量检测
通过目视检查结合涡流探伤、磁粉探伤等无损检测技术,系统排查表面裂纹、折叠、结疤等缺陷。采用三维激光扫描仪可实现0.1mm级精度的表面形貌数字化建模,特别适用于检测高温坯料的氧化铁皮残留情况。
3. 尺寸精度测量
使用高精度卡尺、激光测距仪等设备对坯料的长度、宽度、厚度等几何尺寸进行全截面检测。方坯对角线偏差需控制在±2mm/m以内,板坯宽度公差应满足±5mm的行业规范要求。
4. 内部缺陷检测
采用超声波探伤(UT)技术对坯料内部进行分层、气孔、夹杂物等缺陷的立体检测,可发现最小0.5mm当量的内部缺陷。对于特殊用途坯料,需配合工业CT进行三维成像扫描,检测精度可达50μm级别。
5. 力学性能测试
通过取样进行拉伸试验、冲击试验等,测定坯料的屈服强度、抗拉强度、延伸率等关键指标。试验需严格按照GB/T 228.1金属材料室温拉伸试验方法执行,试样加工需保证与轧制方向的一致性。
6. 金相组织分析
采用光学显微镜和扫描电镜(SEM)观察晶粒度、珠光体比例、带状组织等微观结构特征。通过EBSD技术可精确分析晶粒取向分布,为优化轧制工艺提供数据支持。
7. 残余应力检测
使用X射线衍射法或钻孔法测定坯料内部残余应力分布,特别关注轧制过程中因温度梯度产生的热应力。应力值需控制在材料屈服强度的30%以下,避免后续加工出现变形或裂纹扩展。
检测体系的质量控制
现代钢铁企业普遍建立三级检测体系:在线检测(如热态表面检测系统)、过程抽检(每批次取样)和实验室精密分析。通过建立MES系统实现检测数据实时上传,结合SPC统计过程控制技术,可动态优化轧制参数,将坯料不合格率降低至0.3%以下。同时需定期对检测设备进行计量校准,确保超声波探伤仪灵敏度误差≤1dB,光谱分析仪的重复性偏差≤0.5%。
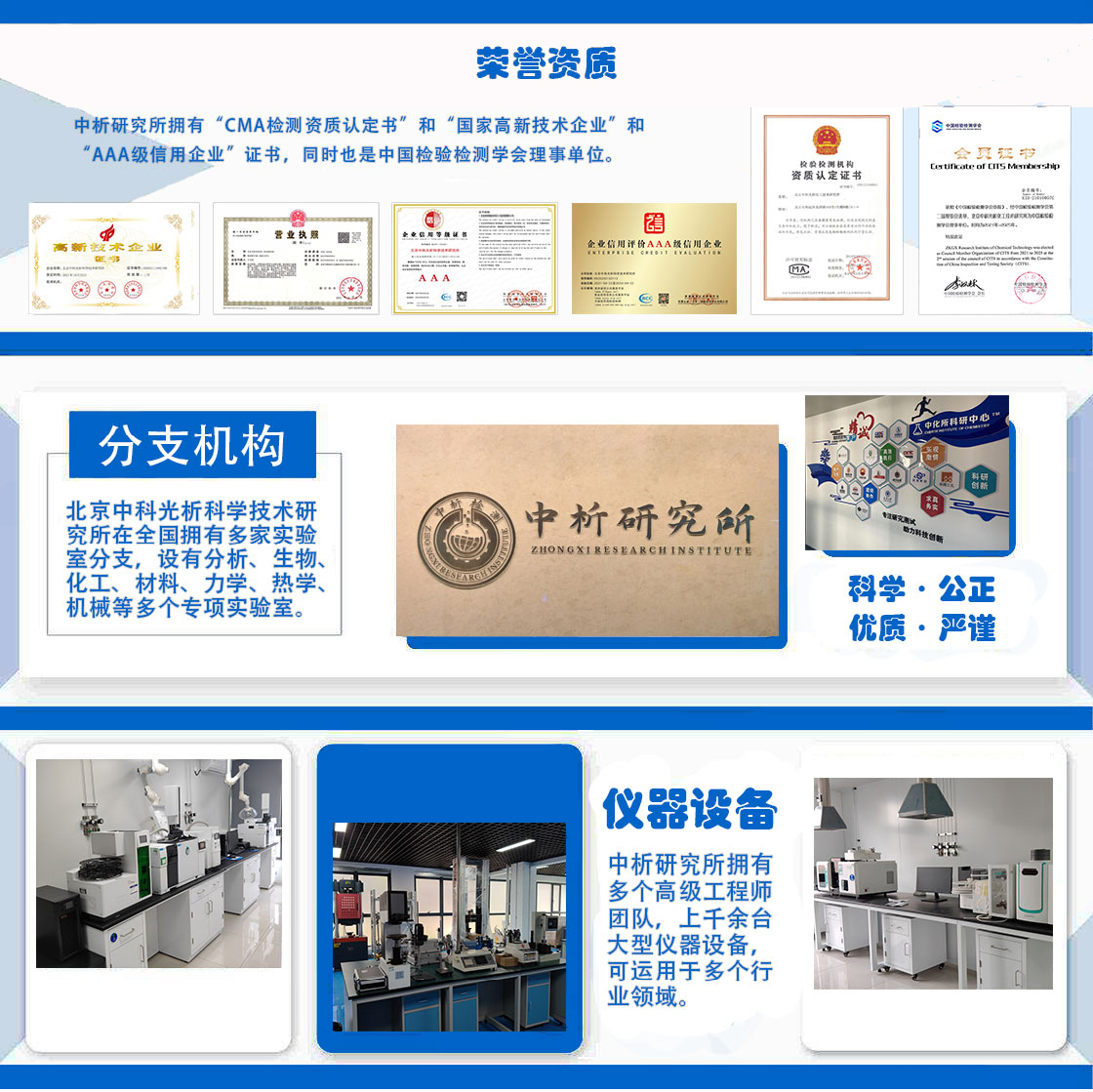
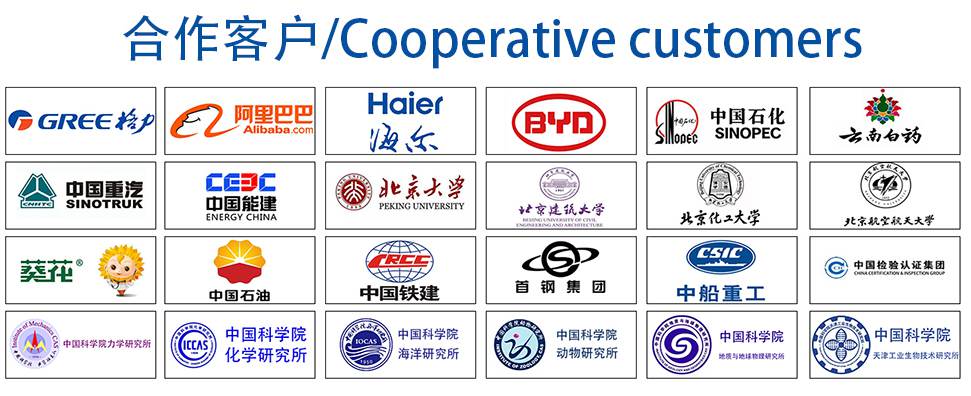