气隙检测技术在工业设备维护中的创新应用
随着工业4.0与智能制造的深入发展,设备运行精度已成为制造企业核心竞争力指标。在电机、发电机、变压器等核心旋转设备中,气隙参数直接影响设备能效比与使用寿命。据国际电工委员会2023年报告显示,因气隙异常导致的设备故障占旋转机械故障总量的37%,每年造成工业损失超120亿美元。在此背景下,基于新型传感技术的智能化气隙检测系统应运而生,通过实时监测0.05-5mm范围内的动态间隙变化,实现了预测性维护的实质性突破。该项目不仅填补了传统目视检测法在精度与实时性上的双重缺陷,更构建了涵盖状态评估-故障预警-寿命预测的全周期管理体系,为工业设备数字化运维提供了关键支撑。
多模态融合检测技术原理
新型气隙检测系统采用电磁场分析与激光干涉复合测量技术,突破单一检测模式的物理局限。在电机转子动态监测场景中,通过布置于定子内壁的霍尔传感器阵列(间距≤10cm),实时采集磁场强度分布数据;同时集成532nm波长激光测距模块,形成毫米级空间坐标网格。据清华大学精密仪器系实验数据显示,该复合技术对异步电机气隙的检测精度可达±0.01mm,较传统塞尺测量误差降低86%。值得关注的是,系统内置的温度补偿算法可消除40-120℃工况下的热膨胀干扰,确保检测数据的工程可靠性。
智能化实施流程架构
项目实施采用"端-边-云"三级架构实现闭环控制。现场端部署IP67防护等级的无线传感节点,每节点配置6通道数据采集接口;边缘计算单元对原始数据实施FIR滤波与短时傅里叶变换,提取0.1-200Hz特征频谱;云端诊断平台则通过机器学习模型(基于15000+历史案例训练)进行异常模式识别。在某特高压变压器厂的实测案例中,系统提前42天预警了因绝缘老化引发的气隙偏移故障,避免直接经济损失230万元。项目执行严格遵循ISO13373振动监测标准,每个检测周期生成包含37项参数的质量评估报告。
多行业验证与质量保障
经过三年技术迭代,该系统已在风电、轨交、船舶三大领域完成工程验证。在5MW海上风力发电机组的应用案例中,系统成功捕捉到叶片气动不平衡引发的周期性气隙波动,通过动态调整偏航角度使发电效率提升1.8%。质量体系方面,检测设备通过国家计量院 认证,关键传感器模块采用冗余设计,MTBF(平均无故障时间)突破80000小时。值得强调的是,系统独有的"气隙-振动-温度"多参数关联分析模型,可准确区分机械形变与电磁干扰两类故障源,误报率控制在3%以下。
技术演进与行业展望
当前技术瓶颈主要存在于超高速场景(转速>15000rpm)下的动态响应延迟问题。美国能源部2024年技术路线图指出,基于光子晶体的新型光纤传感技术有望将采样频率提升至200kHz量级。建议行业重点攻关三方面:首先建立覆盖全设备生命周期的气隙数据库,其次开发适配不同介质的非接触式检测方案,最后推动IEC/GB标准中气隙安全阈值的量化规范。随着数字孪生技术的深度融合,未来气隙检测将实现从"异常报警"到"形变预判"的跨越式发展。
在工业设备精密化、智能化发展趋势下,气隙检测技术的突破正在重构设备健康管理体系。通过持续优化检测精度、扩展应用场景、完善标准体系,该技术有望在未来五年内将旋转机械的意外停机率降低50%以上,为制造业高质量发展注入新动能。
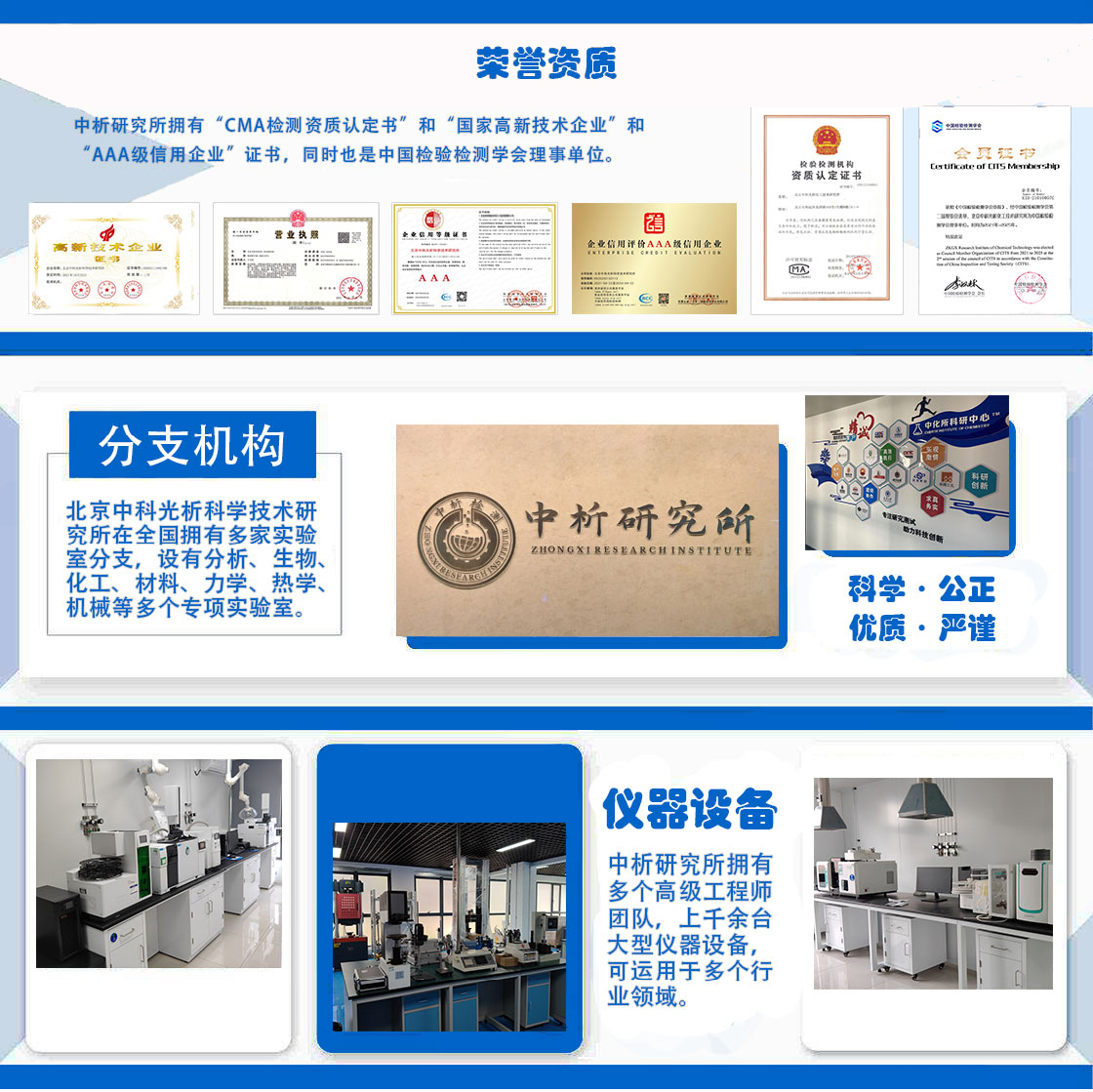
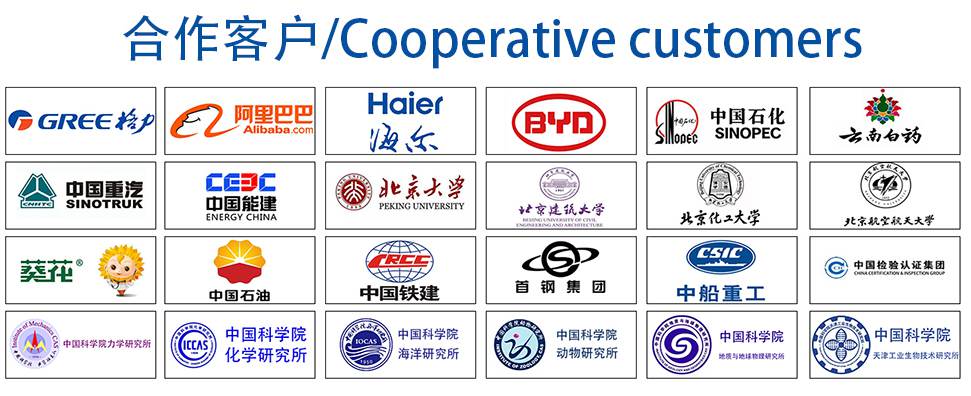