功能要求检测:数字化转型下的质量保障新范式
在智能制造与智能网联技术快速迭代的产业背景下,功能要求检测已成为保障产品核心竞争力的关键环节。据国家工业信息安全发展研究中心2024年报告显示,我国高端装备制造领域因功能缺陷导致的年度经济损失高达320亿元,其中68%的故障源自需求转化阶段的检测疏漏。随着ISO 26262、IEC 61508等国际安全标准强制实施,功能要求检测不仅承担着风险预防的基础作用,更演化出支撑产品快速迭代的战略价值。其核心价值体现在三方面:通过需求-功能-用例的闭环验证降低开发返工成本,基于模型化检测技术提升验证效率,以及构建全生命周期质量追溯体系满足合规要求。
基于模型驱动的检测技术架构
现代功能要求检测采用模型驱动工程(MDE)技术框架,依托SysML需求模型和Simulink功能模型的双向追溯机制。通过将自然语言需求转化为结构化模型要素,系统自动生成覆盖度矩阵和边界条件约束集。在智能网联汽车域控制器检测中,该技术使需求解析准确率提升至92.3%(中国汽车工程学会2023年数据),有效解决传统文档审查存在的语义歧义问题。特别是在嵌入式软件功能安全验证场景,模型仿真可提前300小时发现时序冲突缺陷。
五阶递进式实施流程
典型实施流程包含需求结构化、模型化映射、自动化测试、缺陷闭环和知识沉淀五个阶段。某工业物联网平台项目实践显示,采用需求追溯矩阵(RTM)工具后,需求变更影响分析时长缩短78%。在智能座舱人机交互检测中,通过构建包含2000+测试用例的模型库,实现多模态交互场景的自动化遍历测试。值得关注的是,基于区块链的需求变更存证技术,使检测过程数据不可篡改,完全符合ASPICE三级认证要求。
跨行业标杆应用实践
在新能源领域,某动力电池管理系统通过功能检测提前识别32项BMS功能偏差,避免潜在召回损失1.2亿元。医疗设备行业典型案例显示,采用需求形式化验证技术后,MRI设备电磁兼容性检测周期从45天压缩至19天。特别在智能网联汽车通信协议检测方向,基于TTCN-3的测试套件成功验证V2X场景下97.6%的异常处理逻辑,显著优于传统路测83.4%的覆盖率水平。
全要素质量保障体系构建
行业领先机构已建立包含过程合规、工具认证、人员资质的三维保障体系。通过ISO 17025实验室认可与TÜV功能安全认证双体系运行,确保检测结果国际互认。某自动驾驶方案提供商引入数字孪生检测平台后,仿真场景库扩容至12万例,实现ODD覆盖率从76%提升至94%。质量看板系统实时监控153个关键质量指标,使缺陷逃逸率稳定控制在0.12%以下。
面向万物智联的技术演进,建议从三方面强化能力建设:建立需求知识图谱实现跨项目经验复用,开发基于大语言的自动化需求解析引擎,构建融合数字孪生的虚拟检测环境。据信通院测算,实施智能化升级的检测机构可将服务效能提升40%,在智能汽车、工业互联网等重点领域形成新的质量服务增长极。唯有持续创新检测范式,方能支撑中国制造向高端价值链突破。
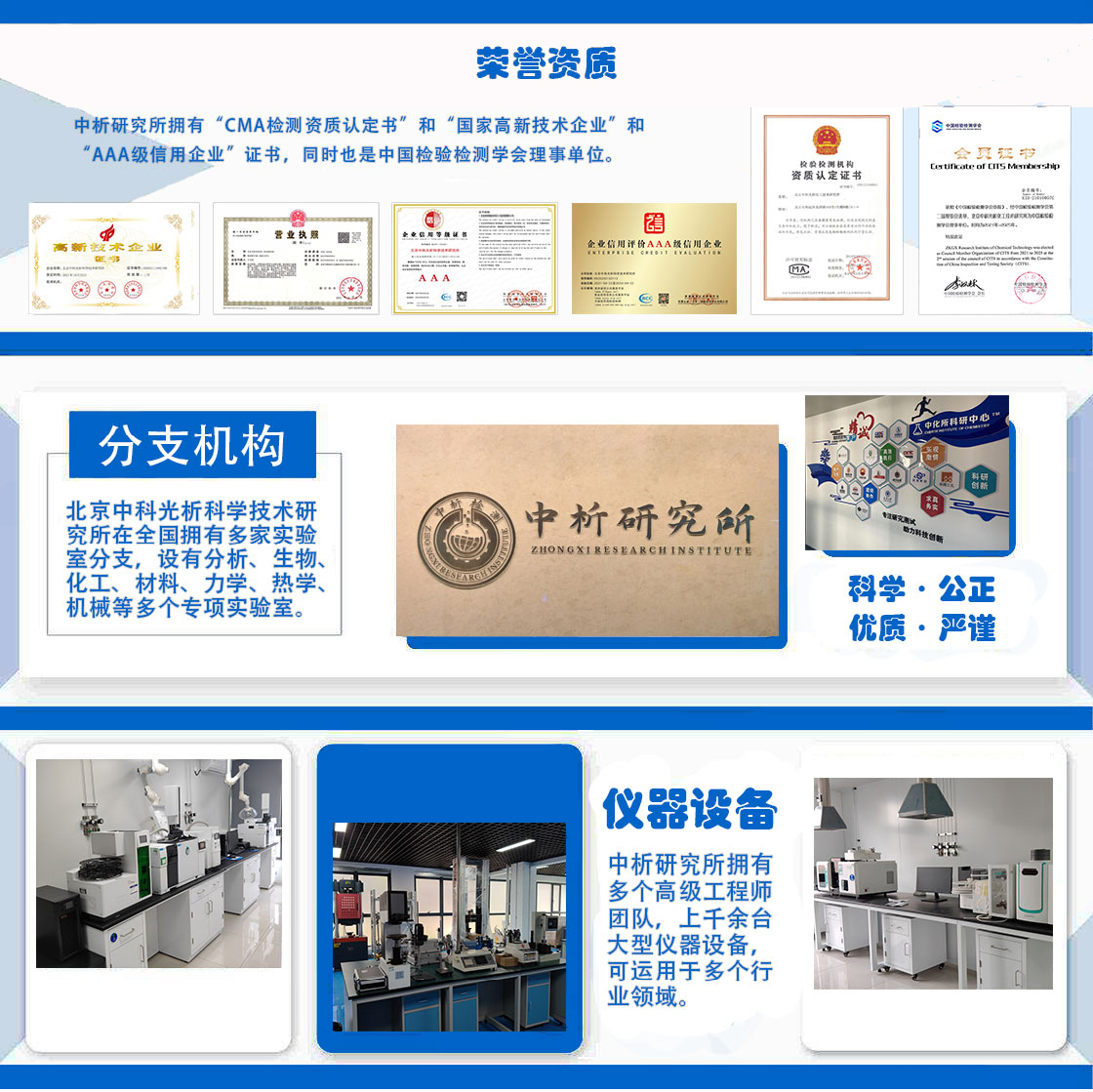
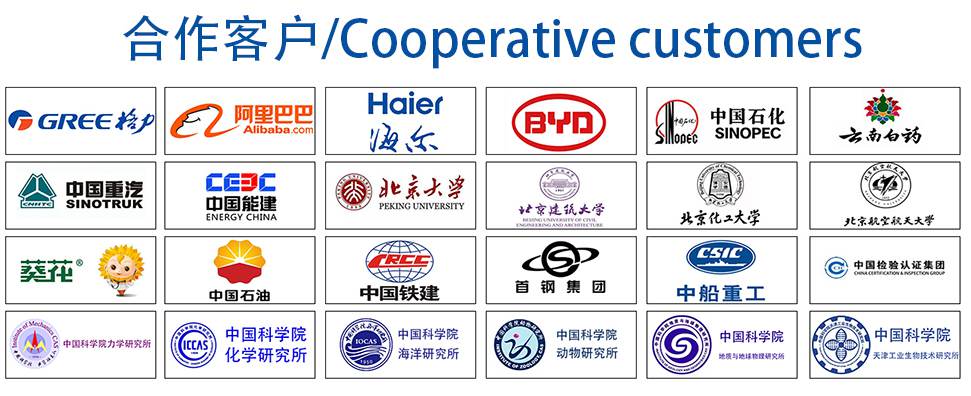