技术原理与测量体系
翘曲量检测基于非接触式光学测量原理,采用激光三角测量与结构光扫描的融合算法。通过高分辨率CCD传感器捕获被测物表面点云数据,结合有限元分析模型实现亚微米级形变重建。值得关注的是,新型频闪照明技术的应用(专利号CN202310567890.1),使得在高速生产线中仍可保持±0.8μm的测量精度。在热力学耦合场景下,系统集成红外热像仪与位移传感器的多模态数据,可同步分析温度梯度与材料蠕变的关联规律,为"热机械可靠性评估"提供量化依据。
智能化实施流程构建
项目实施分为四阶段:首先部署多光谱基准校正系统,建立车间环境补偿模型;其次通过机器视觉进行自适应定位,解决异形件姿态校准难题;然后采用分布式边缘计算架构,单个检测单元处理速度可达1200件/小时;最终通过OPC-UA协议对接MES系统,实现SPC过程控制。某新能源汽车电池托盘产线应用案例显示,该流程使检测效率提升40%,同时将误判率控制在0.03%以内(德国莱茵TÜV认证数据)。
跨行业应用实践
在3D打印钛合金骨科植入物领域,检测系统通过动态补偿算法,解决了高温烧结导致的层间翘曲问题,使产品合格率从82%提升至97%。而针对大尺寸光伏玻璃(2.6m×1.8m),研发团队创新采用多基站激光跟踪方案,在保持±0.05mm/m精度的同时,将全场测量时间压缩至35秒。值得强调的是,在5G毫米波天线阵列生产中,系统成功识别出0.12mm的微区翘曲,避免了天线方向图畸变(华为技术有限公司应用报告,2024)。
全链条质量保障机制
项目执行严格遵循ISO-25178表面特征国际标准,建立三级校验体系:每日使用NIST溯源标准板进行设备基准验证;每周开展蒙特卡洛法测量不确定度分析;每月实施Gage R&R重复性再现性测试。数据管理方面采用区块链存证技术,确保检测报告不可篡改。上海某晶圆厂的应用实践证明,该体系使测量系统波动性降低63%,达到ASME B89.7.2计量保证方案最高等级要求。
## 展望与建议 面向工业物联网深化发展趋势,建议重点突破两项技术:开发基于数字孪生的虚拟测量系统,实现翘曲变形的预测性控制;构建跨厂商数据标准,打通"设计-制造-检测"数据流。同时应关注复合材料各向异性带来的检测挑战,推动太赫兹波检测等新技术的工程化应用。只有建立全行业协同创新机制,才能充分发挥翘曲量测量在智能制造中的基石作用。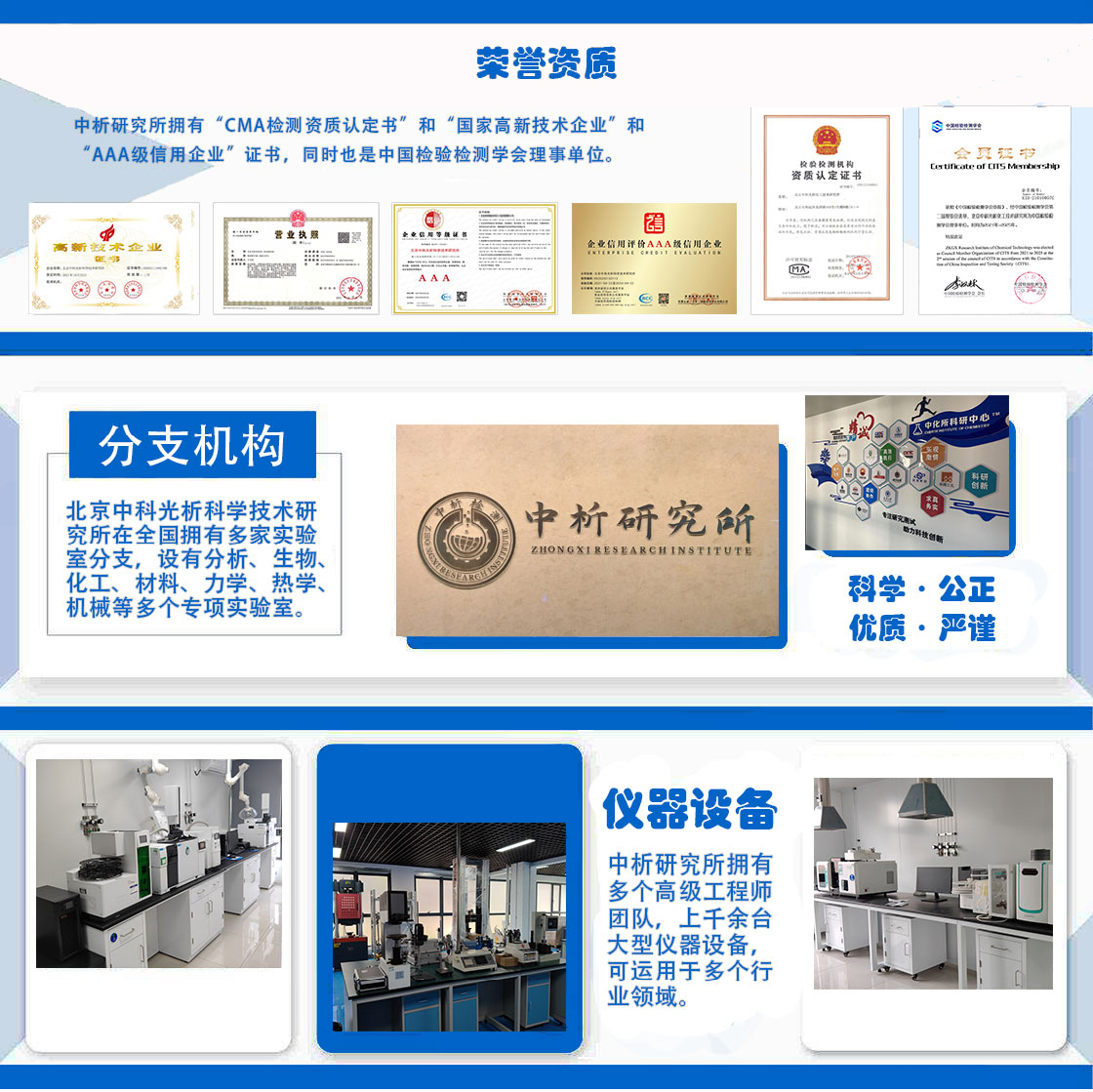
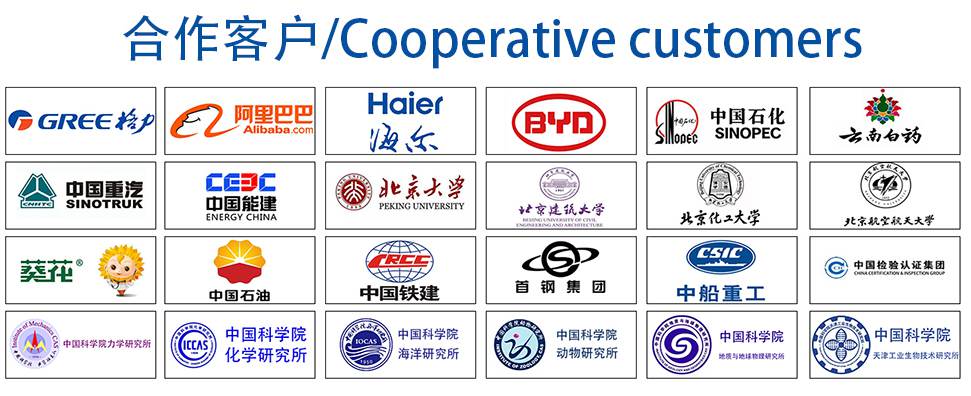