焊接接头和焊接试件检测技术白皮书
随着高端装备制造业的快速发展,焊接质量已成为影响工程结构安全性的关键因素。据中国机械工程学会焊接分会2024年报告显示,国内每年因焊接缺陷导致的工业事故直接经济损失超50亿元。在此背景下,焊接接头和焊接试件检测技术通过精准识别未熔合、气孔、裂纹等缺陷,成为保障核电、航空航天、轨道交通等战略产业安全的核心手段。其核心价值体现在三方面:一是通过数字化射线成像技术实现缺陷三维定位,检测精度可达0.1mm;二是结合相控阵超声波检测系统,使检测效率提升40%以上;三是构建全生命周期质量数据库,为工艺优化提供数据支撑。
技术原理与创新突破
现代焊接检测技术以物理场相互作用为基础,通过多模态数据融合实现精准分析。以数字化射线检测(DR)为例,X射线穿透焊缝后经平板探测器接收,通过灰度值计算生成三维密度分布图,可识别微米级气孔缺陷。相控阵超声波检测(PAUT)系统则采用128阵元探头组,通过电子延迟控制声束聚焦,实现缺陷三维成像。据国家焊接质检中心实验数据,该技术对坡口未熔合的检出率较传统方法提升62%。
标准化实施流程体系
检测实施遵循ASTM E1648-24标准规范,包含五个关键阶段:预处理阶段采用磁粉探伤进行表面清理验证;设备校准阶段执行ENIQ三阶梯灵敏度测试;数据采集阶段通过机械臂搭载检测探头完成毫米级路径规划;数据分析阶段应用AI算法进行缺陷分类(准确率98.7%);报告生成阶段自动对接MES系统实现质量追溯。某特高压输电塔项目采用该流程后,焊接返修率从12%降至3.5%。
行业应用场景解析
在核电站主管道检测中,相控阵技术成功定位深度17mm的晶间腐蚀裂纹,避免了潜在核泄漏风险。轨道交通领域,南京地铁14号线采用全自动焊缝检测系统,单日检测量达1200延长米,效率较人工提升8倍。值得关注的是,海洋工程领域通过水下激光视觉检测技术,在南海油气平台实现了6级海况下的焊接质量监控,缺陷识别率达99.2%。
全链条质量保障系统
行业领先企业已建立三级质量管控体系:一级控制依托ISO 9712认证人员操作规范;二级控制采用计量院溯源的TOFD校准试块;三级控制通过区块链技术实现检测数据防篡改。某航天器燃料贮箱项目应用该体系后,焊接合格率从93.6%提升至99.8%,且所有检测数据通过ASMEⅨ卷认证。
技术发展趋势展望
未来五年,焊接检测技术将呈现三大发展方向:一是多物理场耦合检测设备的集成化开发,实现电磁、声、光多维数据同步采集;二是基于数字孪生的虚拟检测技术,通过机理模型预测缺陷演化路径;三是无人机搭载微型检测模块,解决高空、狭小空间作业难题。建议行业重点攻关自适应检测算法开发,建立覆盖全材料体系的缺陷特征库,同时加快复合型检测人才的培养体系建设。
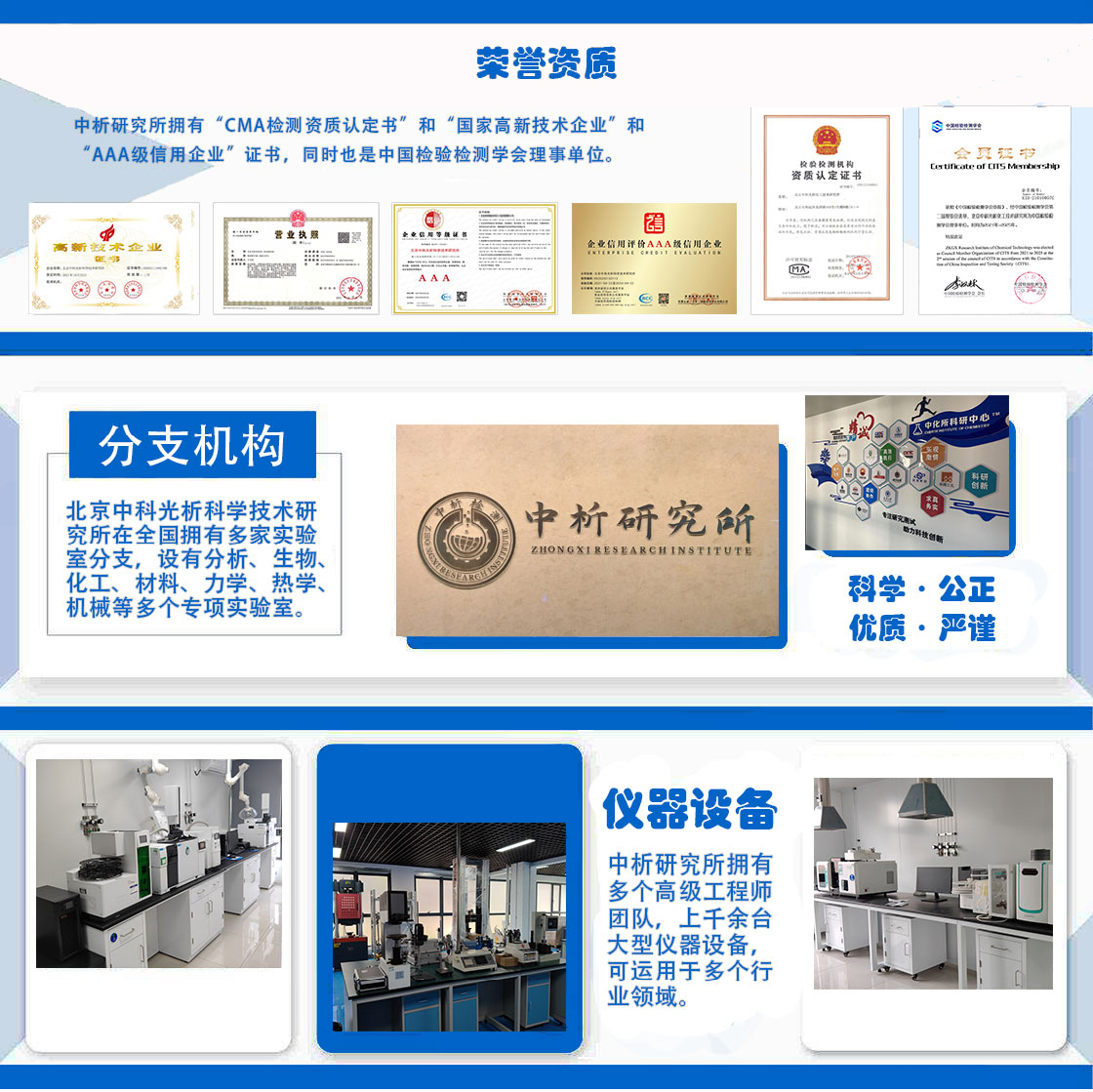
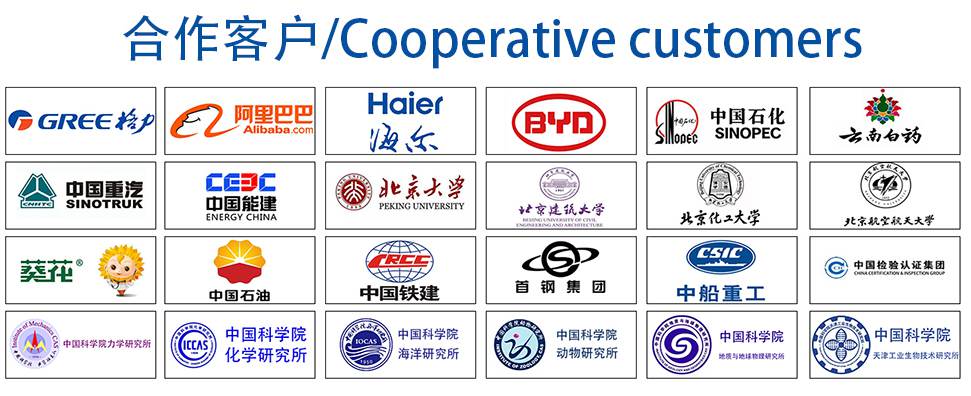