# 温变试验检测技术发展与应用白皮书
## 行业背景与核心价值
在化工业4.0与智能制造转型进程中,温度变化试验作为产品可靠性验证的核心环节,正成为装备制造、新能源、电子信息等战略产业的关键质量关口。据中国电子技术标准化研究院2024年数据显示,因温变失效导致的工业产品年损失超1200亿元,其中新能源汽车三电系统、航空航天精密器件等高端制造领域故障率占比达37.6%。温变试验检测通过模拟-50℃至+150℃的极端温度梯度变化,验证材料热膨胀系数、密封件抗老化性能及电子元器件热稳定性,其核心价值在于突破传统质量控制的事后纠错模式,构建起覆盖产品全生命周期的可靠性预测体系。通过精准的温度循坏测试系统,企业可提前识别产品在寒带极低温冷启动、热带高温高湿环境下的潜在失效风险,支撑产品设计优化与质量成本管控。

## 技术原理与实现路径
### 温度应力加载机理
温变试验检测基于材料热力学性能与失效物理模型,采用交变温场加载技术模拟产品在实际使用中的温度应力。通过高低温循环测试系统(LT-CT Series)实现每分钟5℃的快速温变速率(据IEC 60068-2-14:2023标准),在可控环境下完成材料相变分析、焊点疲劳测试等关键项目。系统搭载的红外热成像模块可实时捕捉PCB板在温度冲击下的局部过热点,分辨率达到0.05℃/pixel(FLIR T865数据),为电子设备散热设计提供量化依据。
### 标准化实施流程
检测流程严格遵循ISO 16750-4:2022《道路车辆电气设备环境试验》及GB/T 2423.22温度冲击试验标准,具体分为三个阶段:预处理阶段在恒温恒湿箱(25℃/50%RH)完成24小时稳定;试验阶段通过三箱式冷热冲击设备实施300次温度循环(-40℃←→+85℃),单次循环时间≤15分钟;数据采集阶段运用分布式温度传感器网络,以1Hz频率记录被测物表面与内部温度梯度变化。
## 行业应用与质量保障
### 新能源汽车验证案例
某头部电池企业在开发800V高压平台时,采用三综合试验箱(温度+振动+湿度)对电池模组进行强化测试。通过2000次-30℃至+65℃快速温变(符合GB/T 31467.3标准),成功识别出极耳焊接处在低温收缩工况下的微裂纹缺陷,推动焊接工艺从单脉冲升级为多段式梯度焊接,使产品通过率从82%提升至98.6%。
### 航天级质量管控体系
在卫星载荷设备检测中,航天五院采用JESD22-A104G标准建立五级温变试验矩阵。通过真空环境下的热真空试验(TVAC)与常压高低温循环的组合测试,精确模拟近地轨道±150℃的极端温差环境。系统集成的失效模式数据库(FMD-2024)已收录超过12万组元器件失效案例,可自动匹配温度应力参数与历史故障特征,实现检测方案的智能优化。
## 技术创新与发展建议
当前行业正从单因素温变测试向多物理场耦合试验进化,建议重点发展三项技术:
1. 开发基于数字孪生的虚拟温变试验系统,通过材料数据库与AI仿真将实物测试周期缩短40%
2. 构建智能失效分析(IFA)平台,集成X射线断层扫描(CT)与热力学仿真模块
3. 建立覆盖"芯片级-模组级-系统级"的三级温度应力验证标准体系
随着物联网设备在极地科考、深空探测等场景的拓展,温变试验检测需突破-196℃(液氮温区)至+300℃(发动机舱环境)的更广域测试能力。建议产业链上下游协同攻关新型相变材料加载技术,推动检测设备温度变化速率突破10℃/s,为第六代半导体、超导装置等前沿领域提供可靠性保障。
上一篇:动载测试检测下一篇:铝合金建筑型材:喷粉型材检测
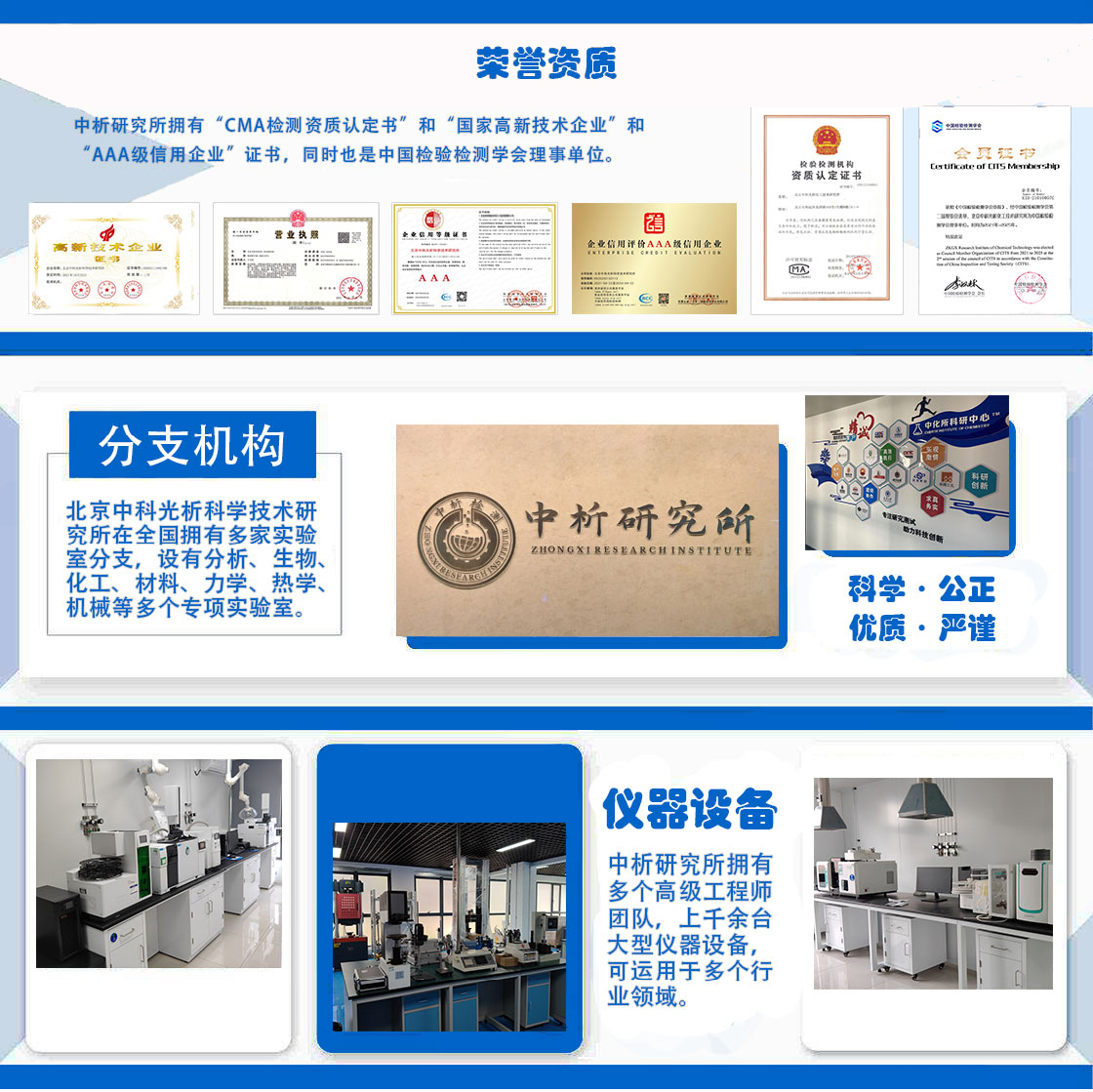
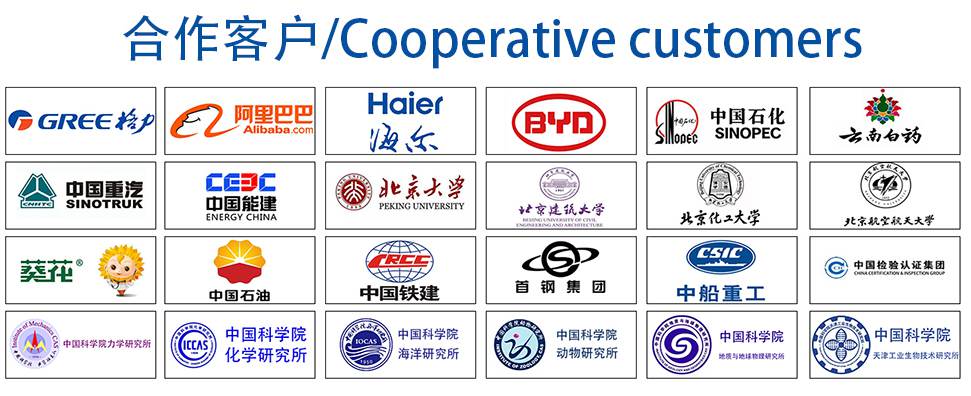
材料实验室
热门检测
7
8
8
12
12
13
13
16
13
14
16
14
23
17
19
22
21
20
23
24
推荐检测
联系电话
400-635-0567