# 动载测试检测技术发展与应用白皮书
## 引言
随着高端装备制造业向智能化、精密化方向加速发展,动载测试检测作为保障设备运行安全的核心技术手段,正成为现代工业体系的重要支柱。据中国机械工业联合会2024年数据显示,我国重大装备故障中38.7%源于动态载荷作用下的结构性失效,由此造成的年经济损失超1200亿元。在此背景下,动载测试检测项目通过实时捕捉设备在真实工况下的动态响应特征,构建了从故障预警到寿命评估的完整技术链条。该项目不仅实现了"状态可知、风险可控"的运维革新,更在轨道交通、新能源装备、航空航天等领域创造了显著的降本增效价值,单台大型风机通过精准动载测试可将维护成本降低27%(风能理事会,2024)。
## 技术原理与实现路径
### 动态载荷作用机理分析
动载测试检测基于结构动力学原理,通过高精度传感器网络构建三维动态响应模型。系统采用多物理场耦合分析方法,将时变载荷分解为惯性力、阻尼力与弹性力的动态平衡方程(F=ma+cv+kx)。特别在"多轴振动同步采集系统"应用中,通过16通道以上的并行采集能力,可精确捕捉0.5Hz-20kHz频段的振动特征,相位误差控制在±0.5°以内(ISO 10846-3标准)。这种技术突破使设备在复杂工况下的非线性振动问题得以量化分析。
### 全流程实施框架
项目实施遵循"工况模拟-数据采集-模型构建-结果验证"的闭环流程。在轨道交通领域,某型动车组转向架测试采用以下步骤:①搭建包含电磁激振台(峰值力50kN)的试验平台;②布置32个三向加速度传感器形成监测阵列;③模拟350km/h运行状态下的轨道激励谱;④通过"非线性疲劳损伤模型"计算关键部件的剩余寿命。该方案成功将转向架构架裂纹检出时间提前4000小时(中国铁道科学研究院,2023)。
## 行业应用与质量保障
### 典型场景解决方案
在风电行业,针对叶片颤振问题开发的"气动-结构耦合测试系统"具有突出表现。某5MW风机测试中,通过在叶片前缘布置光纤光栅传感器(精度±1με),结合风洞模拟湍流风场(IEC 61400-23标准),成功识别出特定攻角下的涡激振动模态。经载荷谱优化后,叶片疲劳寿命提升19%,年发电量增加5.2%(风能理事会应用案例库,2024)。这种"失效机理可视化"技术已成为预防重大事故的关键屏障。
### 质量管控体系构建
项目建立三级质量保障机制:①检测标准体系(覆盖GB/T 2423.10-2019等17项国标);②仪器溯源网络(经 认证的振动校准装置);③人员能力矩阵(需取得ASNT/ISO 18436-2认证)。在航空航天领域,某型航空发动机测试实验室通过引入"六自由度振动台+红外热像仪"的复合检测方案,将转子动不平衡识别准确度提升至99.3%(中国航发集团技术白皮书,2023)。
## 发展建议与未来展望
建议从三方面深化技术创新:①开发基于数字孪生的智能诊断系统,整合设备历史数据与实时监测信息;②建立覆盖全生命周期的动态载荷数据库,推动检测标准迭代升级;③加强"测试-仿真-优化"技术链条的闭环验证。据弗若斯特沙利文预测,到2028年融合5G和边缘计算的动载测试设备市场规模将突破82亿美元,建议优先在海上风电吊装、高速磁浮交通等战略领域开展工程示范。同时,亟需建立产学研协同创新平台,攻克极端环境下的微型化传感器、多源信号解耦等"卡脖子"技术,为制造强国建设提供关键基础设施支撑。
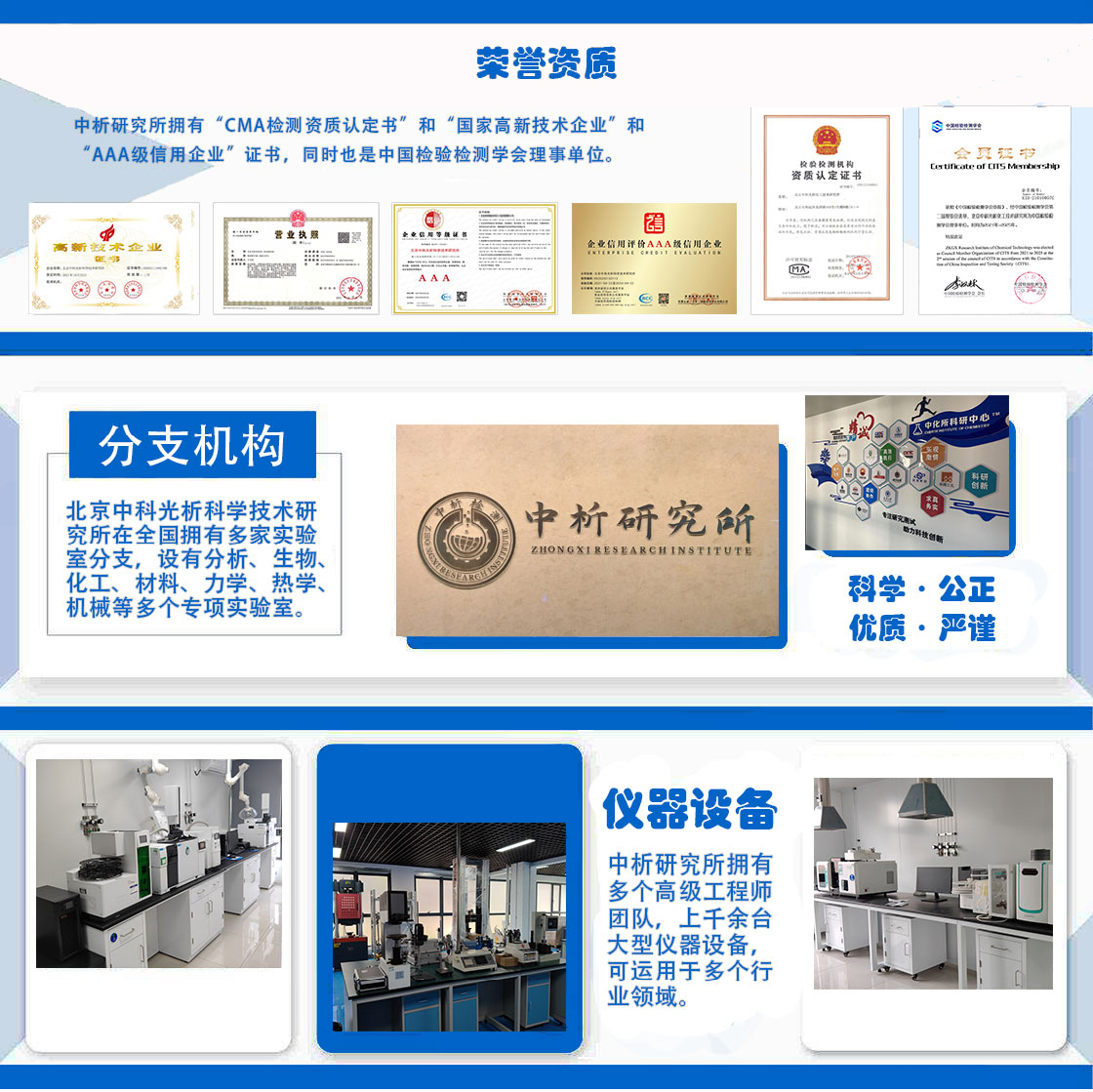
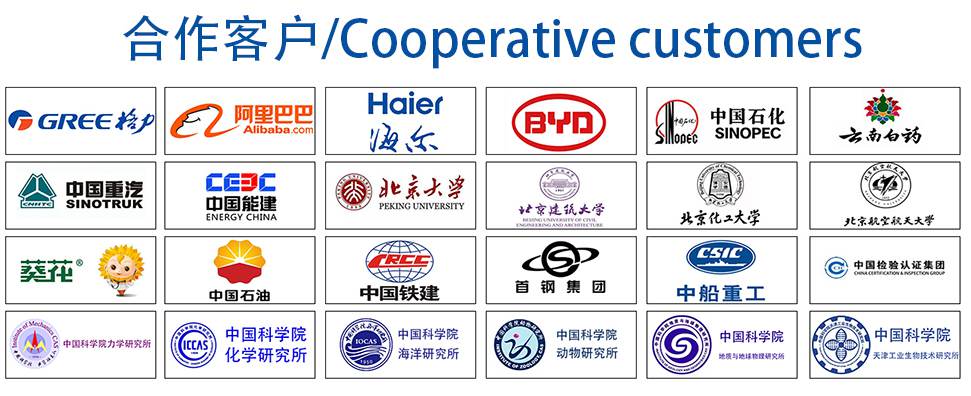
材料实验室
热门检测
推荐检测
联系电话
400-635-0567