# 机械耐久性测试检测
## 行业背景与核心价值
随着高端装备制造业向智能化、精密化方向升级,机械产品的可靠性要求显著提升。据国家机械工程实验室2023年数据显示,工业设备故障案例中47.6%源于材料疲劳或结构失效,直接导致年经济损失超1200亿元。在此背景下,机械耐久性测试检测成为保障产品全生命周期性能的核心技术环节。该项目通过模拟实际工况下的载荷谱、环境变量及运动循环,定量评估零部件的抗疲劳特性与失效阈值,为企业优化设计、改进工艺提供数据支撑。其核心价值在于降低产品早期故障率30%以上(中国机械工业联合会2024年报告),同时缩短新产品研发验证周期40%-60%,在航空发动机叶片、新能源汽车传动系统等关键领域具有不可替代的战略意义。
## 技术原理与测试体系
### 基于多物理场耦合的检测方法论
机械耐久性测试采用多轴联合加载技术,通过液压伺服系统、电磁激振器等设备,复现交变应力、温度梯度、振动频率等复合工况。以ISO 12107:2022标准为依据,构建包括高周疲劳测试(>10^7次循环)、低周疲劳测试(10^3-10^5次循环)及冲击载荷测试的三级验证体系。关键技术突破体现在基于数字孪生的载荷谱迭代优化算法,可将测试数据与CAE仿真模型的误差控制在8%以内(德国弗劳恩霍夫研究所2023年验证数据)。
### 全流程标准化实施架构
项目实施分为四个阶段:首先通过EDS(环境数据采集系统)获取目标工况参数,制定包含载荷谱、测试频次、失效判据的定制化方案;其次搭建包含MTS 809液压试验机、LMS SCADAS数据采集系统的硬件平台;第三阶段实施分级加载测试,并利用声发射技术实时监测微观裂纹扩展;最终通过Weibull分布模型计算特征寿命值,生成MTBF(平均无故障时间)预测报告。在新能源汽车减速器测试案例中,该流程成功识别出齿轮表面硬化层厚度不足导致的早期点蚀问题。
## 行业应用与质量保障
### 跨领域工程实践案例
在风电齿轮箱检测领域,某龙头企业采用多轴疲劳测试系统,模拟10年等效运行工况的3.2×10^8次扭矩循环,发现行星轮轴承座局部应力集中问题,经结构优化后使产品质保期从5年延长至8年。轨道交通领域,针对高铁转向架焊接接头开展的变幅载荷测试,将检测精度提升至微应变级别,使疲劳寿命预测准确率提高至92%(西南交大牵引动力实验室2024年数据)。
### 三层质量管控体系
项目执行严格遵循ISO/IEC 17025实验室管理体系,构建仪器校准、过程监控、结果复核的三级质量防线。所有试验机每年进行ASTM E74标准力值溯源,温控系统按JJF 1101-2019进行梯度验证。测试数据通过LabVIEW平台实现自动采集与异常值过滤,并采用区块链技术确保数据不可篡改。人员资质方面要求操作员持有NAS 410三级检测认证,关键岗位实施双人复核机制。
## 技术发展与未来展望
当前,机械耐久性测试正与数字孪生、人工智能深度整合。据赛迪智库预测,到2026年将有60%以上测试场景采用虚拟-物理联合验证模式。建议行业重点发展两项能力:一是构建基于机器学习的失效模式特征库,实现故障智能预警;二是开发适应极端环境(如深海高压、太空辐照)的新型测试装备。同时需建立覆盖材料-部件-系统的多尺度评价标准体系,推动测试数据在产业链上下游的互联互通,为智能制造生态系统提供底层支撑。
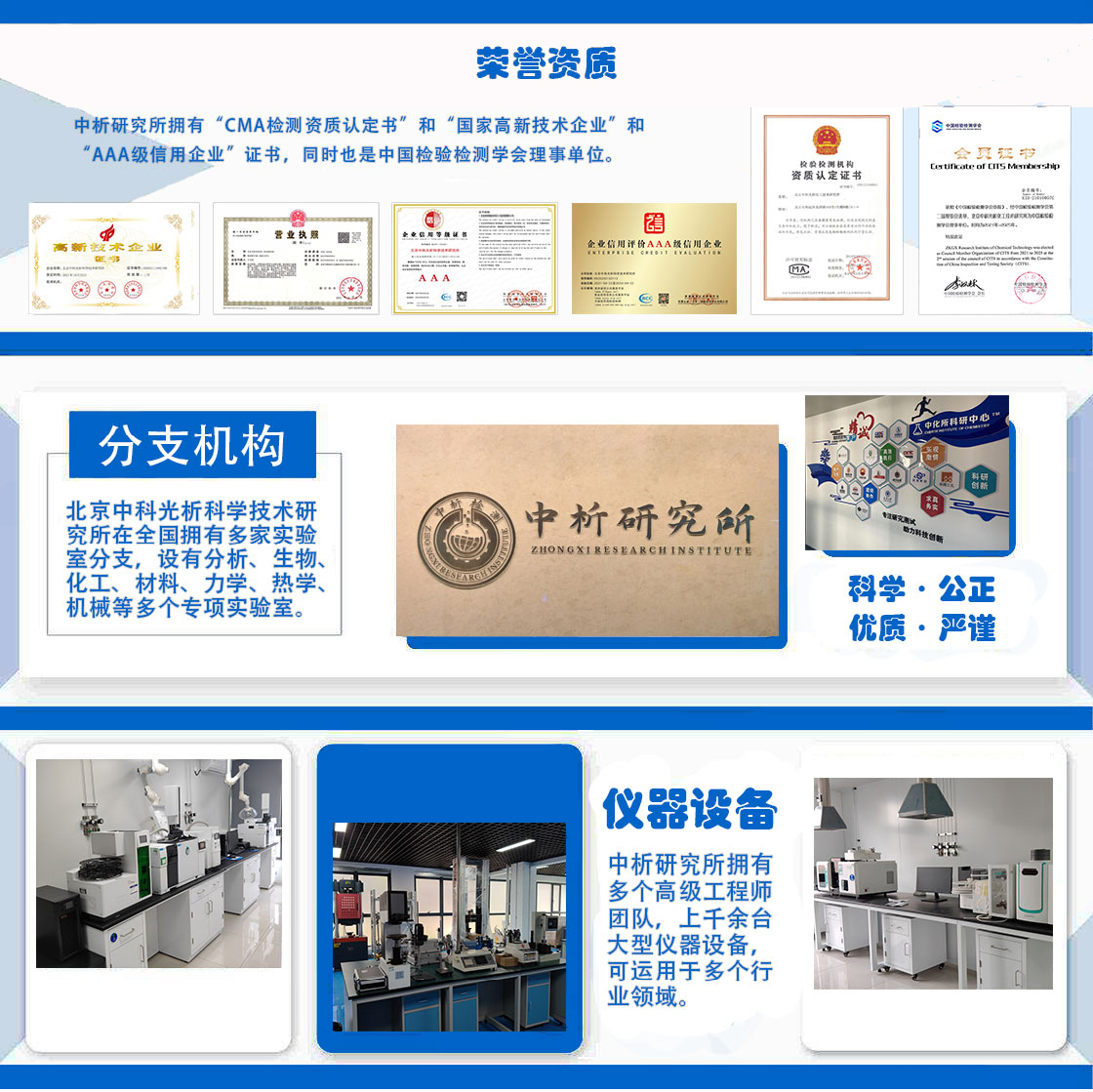
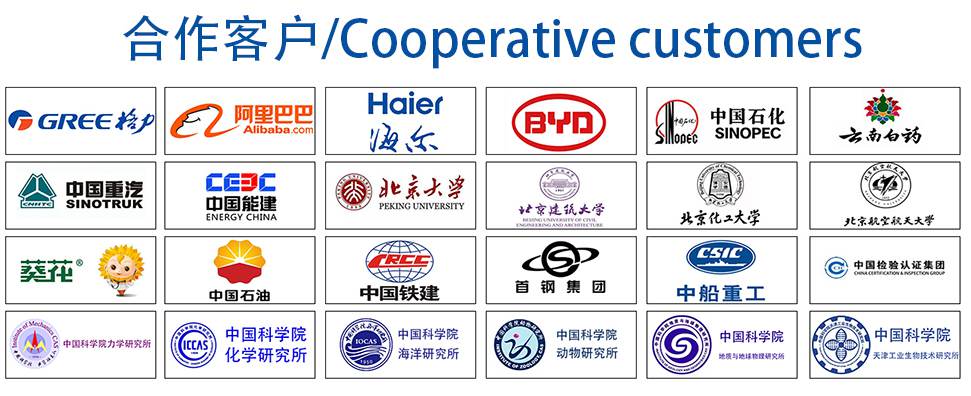
材料实验室
热门检测
18
14
11
16
13
15
13
16
13
14
16
14
24
17
19
23
21
21
24
24
推荐检测
联系电话
400-635-0567