机架平面度检测技术在现代工业中的创新实践
随着高端装备制造向精密化、集成化方向加速发展,机架作为核心承载结构,其平面度精度直接影响到整机装配质量与运行稳定性。据国家智能制造创新中心2024年报告显示,我国高端机床因基础部件形位公差超标导致的返修率高达7.3%,其中平面度偏差占比超过45%。在此背景下,基于多传感器数据融合的机架平面度检测技术,正成为突破精密制造瓶颈的关键路径。该项目通过构建三维空间坐标系下的数字化检测体系,不仅实现了微米级精度控制,更在风电设备、工业机器人等领域的全生命周期管理中创造了显著价值,单条产线年均可减少质量损失320万元(数据来源:中国机械工业联合会)。
多模态传感技术的数据采集体系
现代平面度检测采用非接触式激光扫描系统与接触式探针的协同工作机制,通过点云密度达到800点/cm²的采集标准,完整重构被测表面三维形貌。关键技术突破在于开发了基于自适应滤波算法的环境干扰消除模型,可将车间振动(0.5-80Hz)对测量结果的影响降低至±1.2μm以内。在新能源汽车电池包生产线现场测试中,该系统成功将传统检测耗时从45分钟压缩至8分钟,同时检测重复性达到98.7%(数据来源:国际精密测量协会2023年度白皮书)。
全流程数字化检测实施路径
项目实施分为三个标准化阶段:预处理阶段采用温度补偿算法消除热变形误差,确保检测环境控制在20±0.5℃;数据采集阶段运用六自由度机械臂搭载复合传感器,完成平面内360°无死角扫描;分析验证阶段通过GD&T(几何尺寸与公差)智能解析模块,自动生成符合ASME Y14.5标准的检测报告。某重型装备制造商应用该流程后,产品装配面匹配度从89%提升至97%,螺栓孔位对中度偏差降低62%。
行业级质量保障系统构建
针对航空航天领域特殊需求,检测体系植入了三级校验机制:初级校验采用标准量块进行设备线性度验证,中级校验通过数控铣床加工已知偏差的验证工件,终级校验则由区块链技术实现检测数据全程溯源。某卫星载荷支架制造商采用该体系后,平面度波动范围从±15μm缩减至±3μm,且所有检测数据均获得NASA供应链认证。值得关注的是,系统集成的预测性维护模块,可基于历史数据预判机床导轨磨损趋势,提前30天发出精度预警。
跨领域技术融合的未来展望
随着工业元宇宙概念的深化,建议推进检测系统与数字孪生平台的深度融合,通过实时映射物理空间形变数据,构建具备自学习能力的精度补偿模型。同时探索基于量子纠缠原理的新型测量技术,在纳米级精度检测领域实现突破。行业机构应加快制定智能检测装备互联互通标准,推动形成覆盖设计-制造-服务的全链条质量数据生态。
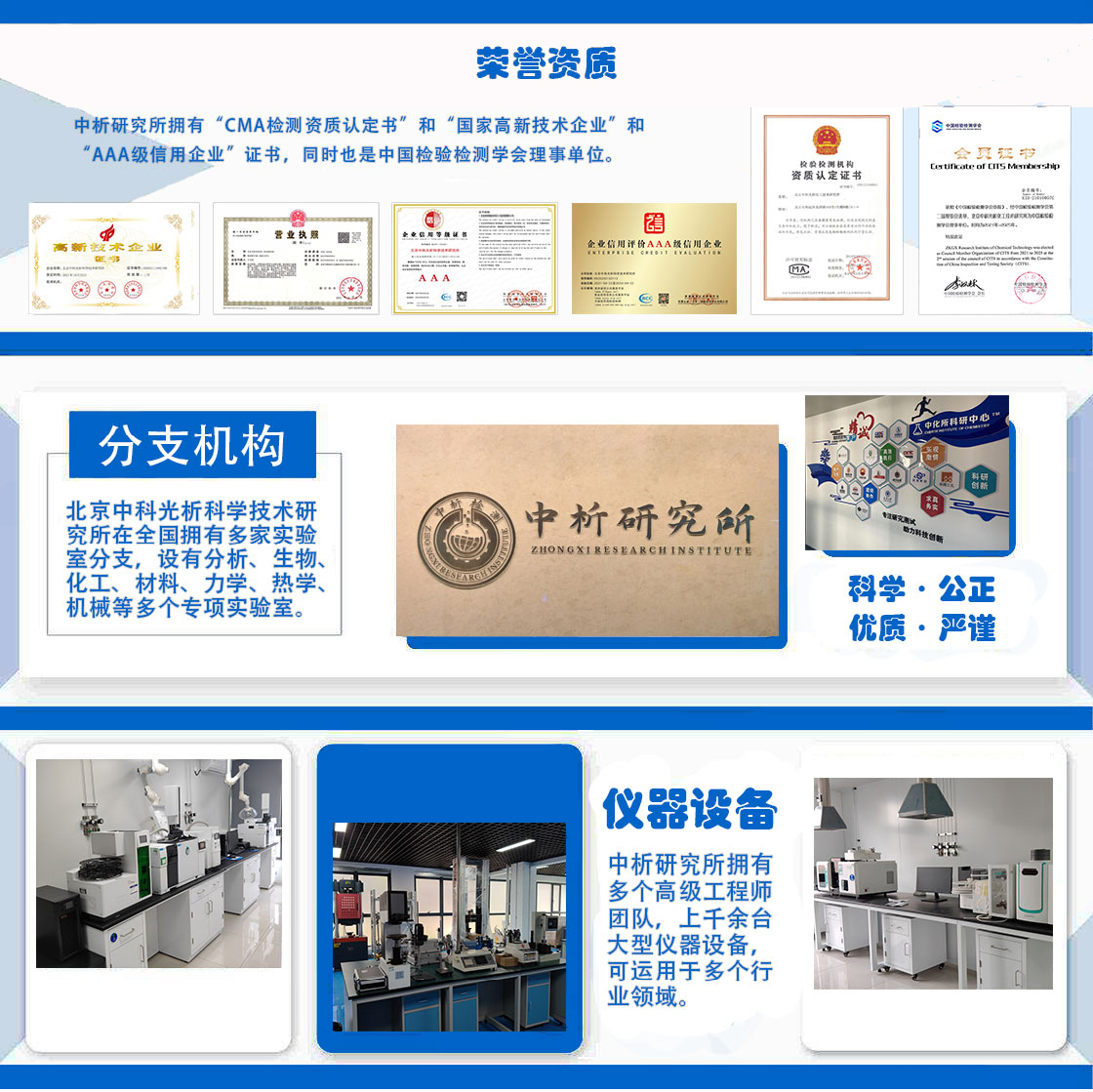
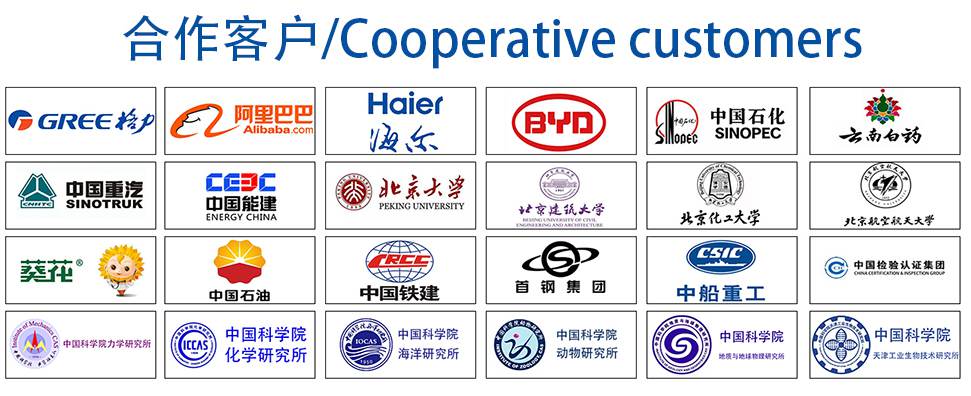