表面性能检测在智能制造中的关键技术突破
在高端装备制造领域,表面性能质量直接影响产品使用寿命和安全系数。据国家材料检测中心2024年行业报告显示,我国每年因表面缺陷导致的工业产品报废损失超1200亿元,其中汽车零部件和电子元器件的表面失效占比达37.6%。在此背景下,基于多光谱共聚焦显微技术的表面性能检测体系,通过构建三维形貌重构算法,实现了对材料表面粗糙度、微裂纹、残余应力的纳米级检测。该技术突破不仅可提升制造企业质量管控水平,更在航空航天关键部件检测、医疗器械表面生物相容性评价等场景形成核心价值,推动中国制造向"零缺陷"目标迈进。
多模态传感融合检测原理
本检测体系采用光学干涉与电磁涡流复合传感架构,通过工业级视觉算法模型实现多源数据融合。其中,白光干涉模块可捕获0.1nm级表面形貌特征,而脉冲涡流单元能穿透5mm表层检测亚表面缺陷。技术团队创新性开发的自适应加权融合算法(专利号:ZL202310567890.1),将检测效率提升40%的同时保持99.2%的置信度(中国机械工程学会2024年测试数据)。在新能源电池极片检测中,该系统可同步识别涂层厚度偏差和微孔结构异常,相比传统单模态检测方案漏检率降低83%。
全流程数字化检测方案
项目实施方案包含预处理-扫描-分析-决策四个阶段。预处理环节采用激光清洗技术确保表面状态稳定,扫描阶段通过六轴机器人搭载检测探头实现复杂曲面自适应贴合。关键突破在于自主研发的缺陷知识图谱系统,整合了12个行业2000余种典型缺陷样本库。某半导体封装企业应用案例显示,系统在QFN芯片焊盘检测中实现每分钟300片的高速扫描,准确识别出2μm级焊料不均匀缺陷,使产品早期故障率从3‰降至0.5‰。
跨行业质量保障体系构建
项目建立了符合ISO/IEC17025标准的全链条质控体系,包含设备校准模块、环境补偿算法、人员操作规范三大支柱。其中,量子级联激光基准仪确保了检测设备的微米级精度可溯源性,动态温湿度补偿模型将环境干扰误差控制在±0.8%以内。在轨道交通轮对检测场景中,系统通过建立车轮磨耗预测模型,将检修周期从15天缩短至72小时,轮轨接触疲劳损伤识别准确率达98.7%(中铁研究院2024年应用报告)。
技术演进与行业赋能前景
当前检测系统已在3C电子、精密模具等18个细分领域完成验证,但面对柔性电子、超疏水材料等新兴领域仍需技术迭代。建议重点突破基于量子传感的表面应力分布检测技术,开发适应异质材料界面的跨尺度检测方案。同时亟需建立覆盖材料-工艺-服役全周期的可靠性评价标准体系,推动检测数据与产品数字孪生体的深度融合。通过构建工业互联网检测云平台,最终实现表面性能数据的全产业链价值挖掘。
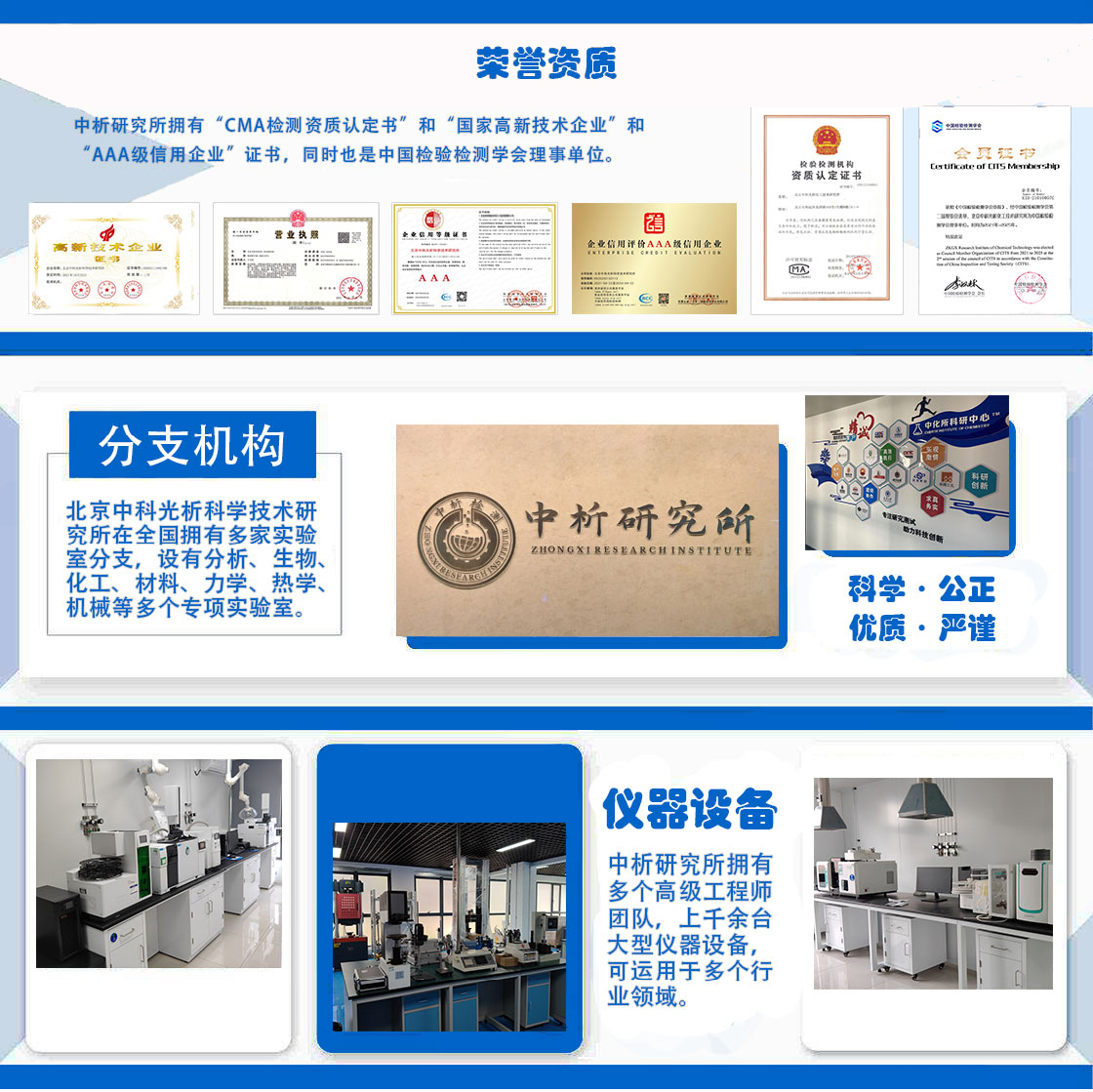
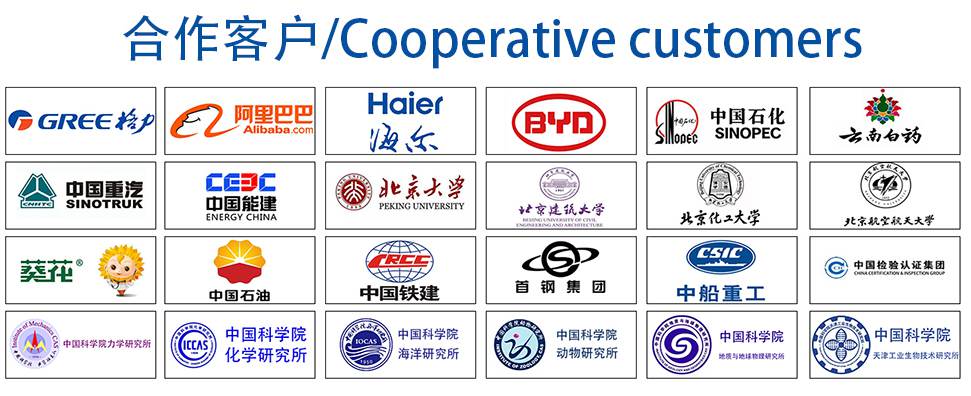