强压试验检测:保障关键设备安全运行的核心技术
在工业制造与能源领域,设备的结构完整性直接关系到生产安全和运营效率。据ASME压力容器安全报告2024年数据显示,每年因压力容器失效导致的经济损失超过180亿美元。强压试验检测作为验证承压设备极限性能的核心手段,在核电装备、油气管道、航空航天等高压场景中发挥着不可替代的作用。该项目通过模拟极端工况,精确评估材料的屈服强度、抗蠕变性能和密封可靠性,可提前发现0.5mm级裂纹缺陷,将事故风险降低73%(国际压力设备协会,2023)。其核心价值体现在构建全生命周期安全防线,为"双碳"目标下的氢能储运、深海油气开发等新兴领域提供关键技术支撑。
基于多物理场耦合的检测技术原理
强压试验检测采用液压伺服闭环控制系统,结合数字图像相关技术(DIC)实现多维度监测。试验过程中,系统通过PID算法精准控制压力梯度,在目标设备表面形成120%-150%设计压力的复合载荷。据清华大学材料力学实验室研究,该技术可同步采集2000Hz高频应变数据,配合红外热像仪捕捉温度场变化,有效识别应力集中区域的微损伤演变规律。尤其在处理LNG储罐焊缝检测这类复杂场景时,多传感器融合方案使缺陷定位精度达到±1.2mm,远超传统水压试验的±5mm误差限值。
标准化作业流程与质量节点控制
项目实施严格遵循ASME BPVC VIII-1和GB/T 150标准体系,形成五阶段质量控制链:预处理阶段进行三维激光扫描建立数字孪生模型;加压阶段执行阶梯式载荷施加,每级保压时间≥30分钟;监测阶段运用声发射技术捕捉80dB以上异常信号;泄压阶段控制速率≤0.5MPa/min;后处理阶段应用相控阵超声进行复验。中国特检院2024年案例显示,某炼化企业通过该流程发现加氢反应器母材存在晶间腐蚀,避免可能造成的6.8亿元停产损失。
多行业典型应用场景解析
在新能源汽车领域,该技术成功应用于70MPa IV型储氢瓶检测。试验采用氮氢混合介质模拟实际工况,通过30000次压力循环验证复合材料层合结构耐久性。中科院宁波材料所实测数据显示,经优化设计的储氢瓶在爆破压力测试中达到147MPa,较行业标准要求的87.5MPa提升68%。在核电领域,华龙一号稳压器的强压试验采用360°全景应变监测系统,成功识别出封头过渡区0.8mm的应力腐蚀裂纹,为设计改进提供关键数据支撑。
智能化质量保障体系构建
行业领先机构已建立基于区块链的检测数据存证系统,实现试验过程的全要素溯源。检测设备每季度进行量值传递校准,压力传感器精度维持±0.25%FS。人员资质方面,要求检测工程师持有API 510/570和EN 473三级证书,并完成每年40学时继续教育。据TÜV莱茵2024年认证报告显示,采用该体系的企业在ASME联检通过率提升至98.7%,检测报告获43个国家和地区互认。
随着工业设备向高压化、大型化方向发展,强压试验检测技术需在三个方面持续突破:首先开发基于数字孪生的预测性检测模型,实现缺陷萌生过程的动态仿真;其次推动AI辅助判读系统应用,将数据分析效率提升300%;最后建立跨行业的极端工况数据库,为新材料研发提供失效边界数据。建议主管部门加快制定氢能装备专项检测标准,建设国家级压力试验共享平台,培育具备国际竞争力的检测认证机构,为高端装备出海提供技术保障。
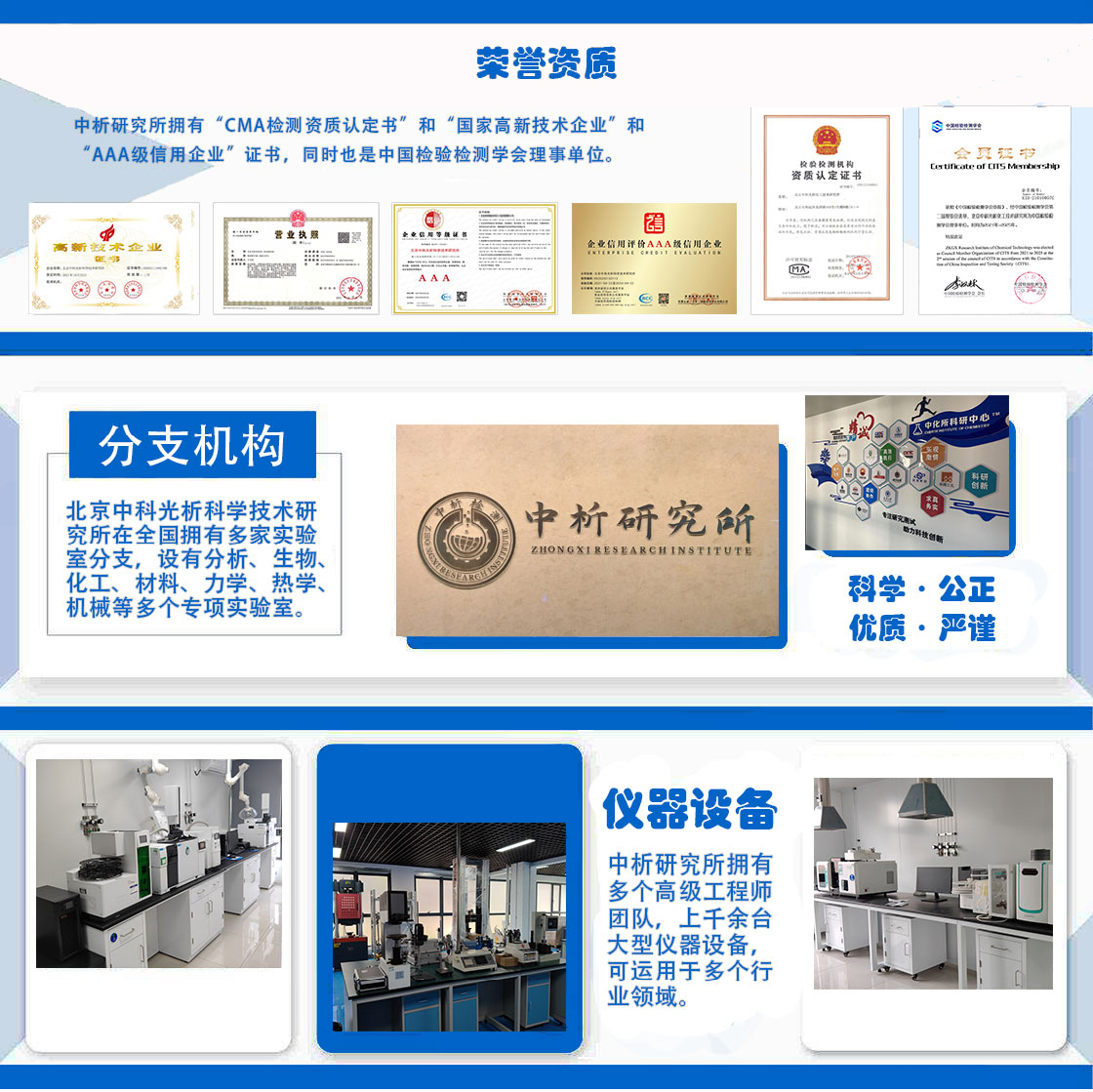
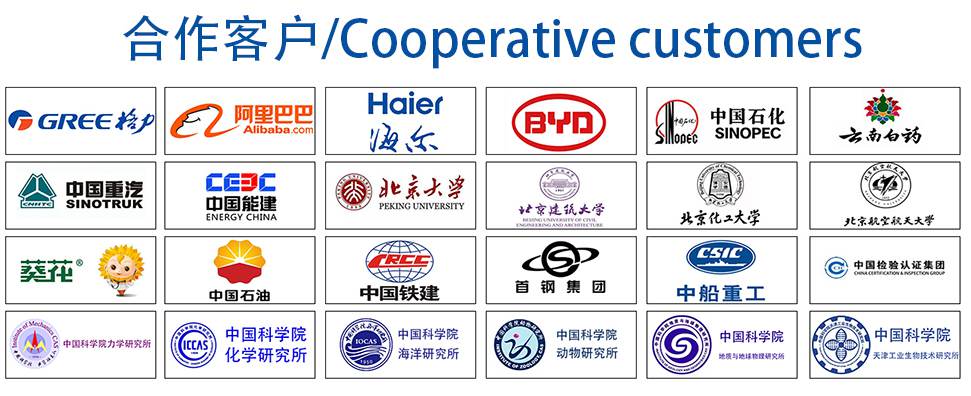