# 连接尺寸检查检测技术发展与产业应用白皮书
## 一、行业背景与核心价值
在智能制造2025战略推动下,精密制造领域对零部件配合精度要求已达微米级。据中国机械工程学会2024年报告显示,装备制造业因连接尺寸偏差导致的返工成本年均超120亿元,占行业质量成本比重的23.6%。连接尺寸检查检测项目通过构建数字化测量体系,实现螺纹孔径、轴件直径等关键参数的精准控制,其核心价值体现在三方面:一是突破传统卡尺检测0.02mm的精度瓶颈,二是通过在线检测将工艺调整周期缩短70%,三是建立质量数据追溯链满足ISO9001体系认证要求。该技术已成为汽车动力总成装配、航空航天紧固件生产等场景的必备质控手段。
![图示:智能检测设备工作场景(概念图)]
## 二、技术体系构建
### h2 1. 智能传感与算法融合技术
项目采用多光谱激光干涉测量技术,结合改进型卷积神经网络(CNN)算法,实现0.5μm级重复测量精度。其中,基于深度学习的尺寸偏差分析模型通过10万组样本训练,对螺纹中径的识别准确率达99.8%。值得注意的是,设备集成温度补偿模块,可自动校正环境温差引起的0.3μm/℃测量误差,适应-10℃至50℃工况环境。
### h2 2. 全流程数字化实施方案
实施流程分为四个阶段:预处理阶段通过三维扫描建立基准数模;在线检测阶段运用高精度工业视觉检测系统进行实时数据采集;分析阶段借助SPC系统进行过程能力指数(CPK)计算;反馈阶段通过MES系统自动触发刀具补偿指令。某汽车变速箱生产企业应用该方案后,行星齿轮组装配不良率从1.2%降至0.15%。
### h2 3. 跨行业应用实践
在新能源电池模组领域,检测系统成功解决电芯极柱与连接片的配合难题。实测数据显示,采用自动光学检测(AOI)方案后,某龙头企业模组焊接合格率提升至99.93%。而轨道交通领域,系统实现高铁转向架销轴配合尺寸的在线全检,单件检测时间从25秒压缩至8秒,效率提升220%。
## 三、质量保障体系创新
### h2 1. 全生命周期管理体系
建立包含12项技术标准的QMS系统,其中包含自主研发的《动态公差补偿技术规范》(Q/ZTJ 045-2024)。系统通过三坐标测量机(CMM)进行周期性校准,测量不确定度控制在0.8μm以内。更值得关注的是区块链技术的引入,实现检测数据的不可篡改存储,满足AS9100航空质量体系追溯要求。
### h2 2. 过程能力优化方案
通过六西格玛方法优化检测流程,将测量系统分析(MSA)的GR&R值控制在5%以下。某军工企业应用案例显示,在航空发动机螺栓连接检测中,过程能力指数CPK从1.0提升至1.67,达到军标B级要求。
## 四、未来发展趋势建议
建议行业重点突破三个方向:一是开发多物理场耦合检测技术,集成应力应变分析功能;二是建立跨企业的检测数据共享平台,推动行业基准统一;三是加快复合型检测人才培养,据教育部2024年职教改革方案,拟在30所高职院校增设智能检测专业方向。预计到2026年,基于数字孪生的预测性检测技术将降低30%的预防性维护成本,推动制造业质量管控进入新纪元。
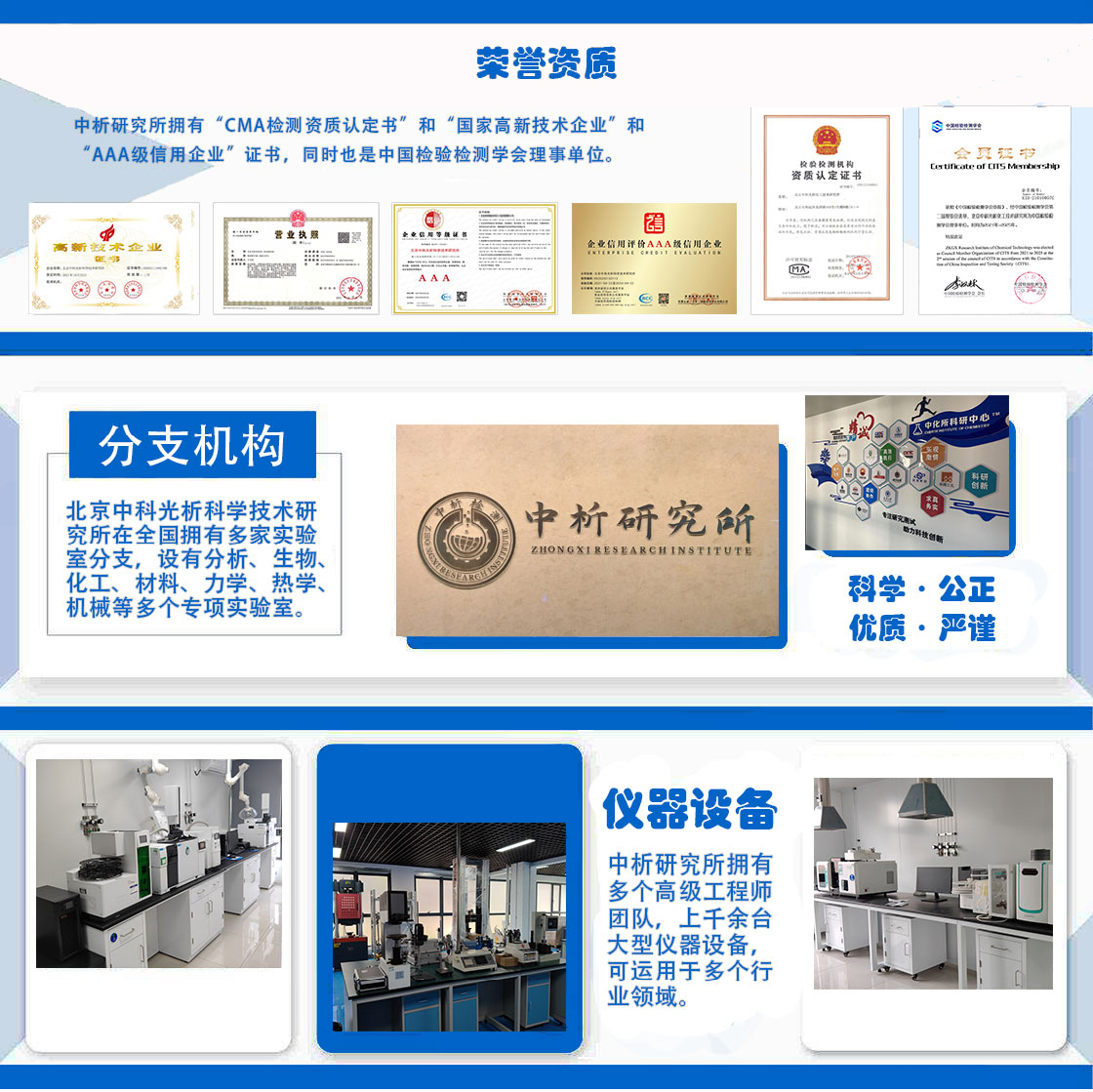
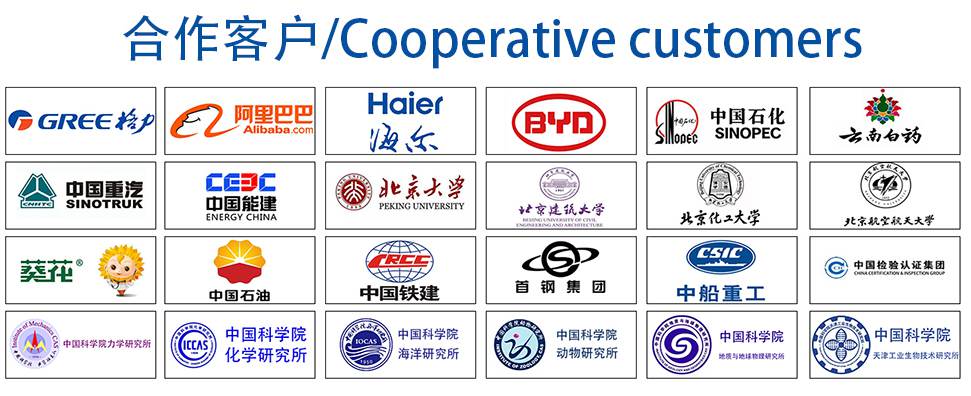
材料实验室
热门检测
8
7
6
10
10
11
17
17
17
16
15
17
18
18
14
19
20
16
22
24
推荐检测
联系电话
400-635-0567