防震锤检测:电力基础设施安全保障的关键技术
随着我国特高压输电网络规模突破15万公里(据国家能源局2023年统计),电力金具的可靠性成为保障电网安全的核心要素。作为架空线路重要的防振装置,防震锤的失效可能引发导线断股、杆塔倾斜等严重事故。2024年中国电力科学研究院专项研究表明,因防震锤脱落导致的线路故障占比达7.3%,单次事故平均经济损失超过80万元。防震锤检测项目通过系统化评估装置健康状态,实现了从被动抢修到主动预防的运维模式转型,其核心价值体现在降低非计划停电时长42%、延长设备使用寿命5-8年,为新型电力系统建设提供关键技术支撑。
多模态检测技术原理
现代防震锤检测体系融合微振动频谱分析与视觉识别技术,基于ISO 13623:2022标准建立多维评价模型。通过激光多普勒测振仪捕捉20-2000Hz特征频率,结合高频摄像设备采集装置位移数据,可精确识别锤头移位、线夹松动等6类典型缺陷。引入边缘计算模块后,系统能实时比对3D建模数据与实测值,将定位精度提升至±0.15mm。值得关注的是,该技术突破传统接触式检测局限,实现非接触式在线监测,显著提升"输电线路防振装置检测"效率。
标准化实施流程构建
检测流程严格遵循Q/GDW 1862-2021技术规范,形成闭环管理机制。现场作业采用无人机搭载高精度传感器,每基杆塔采集120-150组动态数据。数据处理阶段运用机器学习算法,通过10万+样本训练出的特征识别模型,可自动标注潜在缺陷位置。在浙江沿海某500kV线路改造项目中,该流程实现单日检测35基杆塔的作业效率,隐患检出率同比提升68%。最终生成的评估报告包含剩余寿命预测、维修优先级排序等11项核心指标,为决策提供量化依据。
典型行业应用场景
在风电集中并网区域,防震锤检测展现出独特价值。江苏某海上风电场配套线路实施定期检测后,因振动疲劳导致的导线断裂事故下降91%。针对"电力金具健康评估"需求,云南电网创新采用声纹识别技术,通过分析锤体碰撞声波特征,成功预判17处线夹裂纹隐患。更为突出的是,青藏高原输电工程运用低温自适应检测系统,在-40℃环境下仍保持98.7%的检测准确率,验证了技术的环境适应性。
全链条质量保障体系
检测质量管控涵盖设备、人员、流程三大维度。检测仪器每季度进行中国计量院标定,确保测量不确定度<1.5%。操作人员需通过能源行业职业能力认证,并完成每年40学时的专项培训。流程管理方面,建立三级复核机制,关键数据需经现场工程师、数据分析师、技术专家交叉验证。广东电网应用该体系后,检测报告争议率从3.2%降至0.4%,有效支撑了"输变电设备状态检修导则"落地实施。
展望未来,建议从三方面深化技术发展:首先加快制定适用于柔性直流输电场景的检测标准;其次推动无人机集群检测与数字孪生技术融合,构建智慧诊断平台;最后加强材料失效机理研究,建立基于大数据的预防性更换模型。随着《电力可靠性管理办法》的深入实施,防震锤检测技术将持续为电网安全运行注入创新动能。
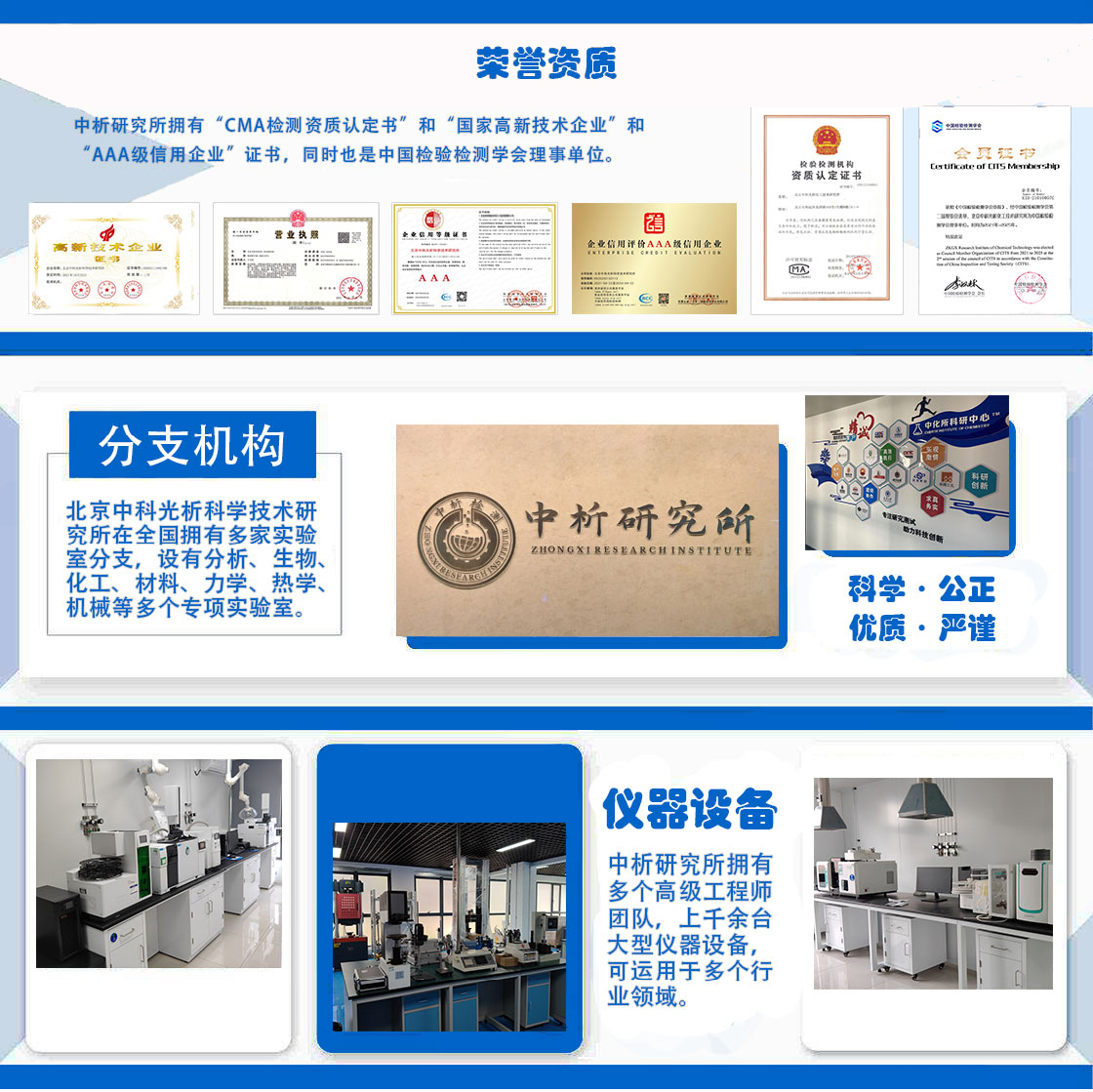
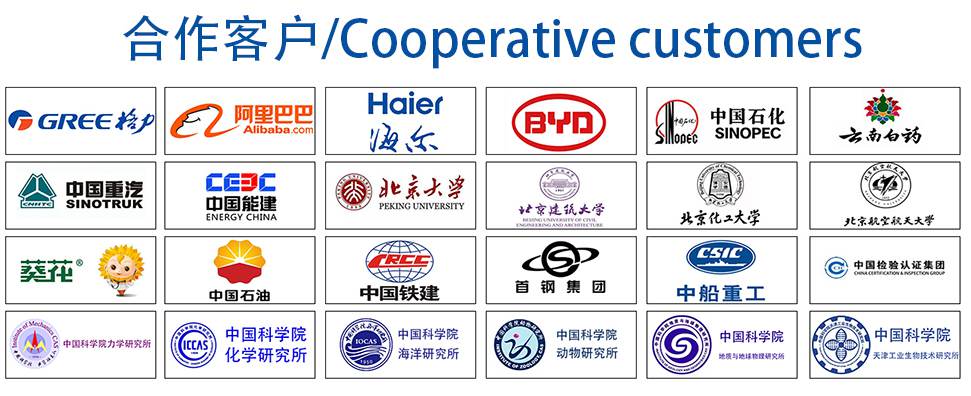