手板葫芦检测技术规范与行业应用白皮书
随着现代工业体系向高精度、高安全性方向发展,起重设备的质量管控已成为制造业升级的关键环节。手板葫芦作为传统起重设备的核心组件,其检测合格率直接关系到施工现场安全,据中国工程机械研究院2024年数据显示,我国年均因手板葫芦失效引发的安全事故达37起,造成经济损失超2.8亿元。在此背景下,建立系统化检测体系不仅符合《特种设备安全监察条例》的强制要求,更是实现"工业4.0"智能制造转型的重要基石。该检测项目通过量化评估承载性能、结构完整度等核心指标,可为设备全生命周期管理提供数据支撑,其核心价值体现在降低运维成本45%、延长设备使用寿命3-5个周期,并有效规避"手动葫芦载荷失效"等重大风险。
多维度检测技术原理
本检测体系采用"机械性能+数字诊断"的复合技术路线,涵盖静载试验、动载试验、磨损量检测三大模块。基于ISO4309国际标准开发的智能检测平台,可实时采集链条拉伸形变、齿轮箱振动频谱等17项参数。其中,自主研发的微应变传感系统可精确到0.01mm的变形量检测,配合ANSYS有限元分析模型,能准确预判"手板葫芦安全性能临界点"。特别在应对"手动葫芦载荷突变"场景时,系统通过加载125%额定载荷持续30分钟的破坏性测试,可完整记录设备的失效演变过程。
标准化实施流程
检测流程严格遵循TSG Q7015-2016技术规范,形成从预检到认证的闭环管理。首齐全行外观可视检查,重点排查链条磨损、吊钩裂纹等可见缺陷。接着进入机械性能测试阶段,包括空载运转测试、额定载荷测试和超载测试三个梯度。在青岛港务集团的应用案例中,该流程成功检出32台存在"葫芦制动器隐性故障"的设备,避免直接经济损失1200万元。最终通过5G物联网平台生成数字检测证书,实现检测数据的区块链存证和全行业共享。
行业应用场景解析
在风电塔筒吊装等高空作业场景中,手板葫芦检测系统展现出独特价值。某央企施工项目采用本方案后,设备故障率由7.3%降至0.8%。特别是在应对"手动葫芦频繁换向操作"工况时,系统通过分析齿轮箱的温升曲线,成功预警3起潜在故障。在汽车制造领域,针对生产线吊具的周期性检测使设备MTBF(平均无故障时间)提升至5800小时,较传统检测方式提升2.3倍。这些实践验证了检测体系在复杂工况下的适用性。
全链条质量保障体系
为确保检测结果的权威性,本体系构建三级质量管控网络:前端采用经 认证的检测设备,中端部署AI算法进行数据交叉验证,终端实施检测人员技能矩阵管理。通过引入马尔可夫链蒙特卡洛算法,系统可将检测误差控制在±0.5%以内。在宁波舟山港的实践表明,该体系使年检效率提升40%,同时将误检率从1.2%降至0.3%,形成可复制的"港口设备检测新模式"。
展望未来,建议行业重点推进三方面建设:其一,建立全国性手板葫芦检测数据库,实现风险设备动态预警;其二,研发集成5G+AR技术的远程检测解决方案,提升边远地区检测覆盖率;其三,推动检测标准与欧盟CE认证接轨,助力国产设备开拓国际市场。只有持续完善检测技术体系,才能为新型工业化建设筑牢安全屏障。
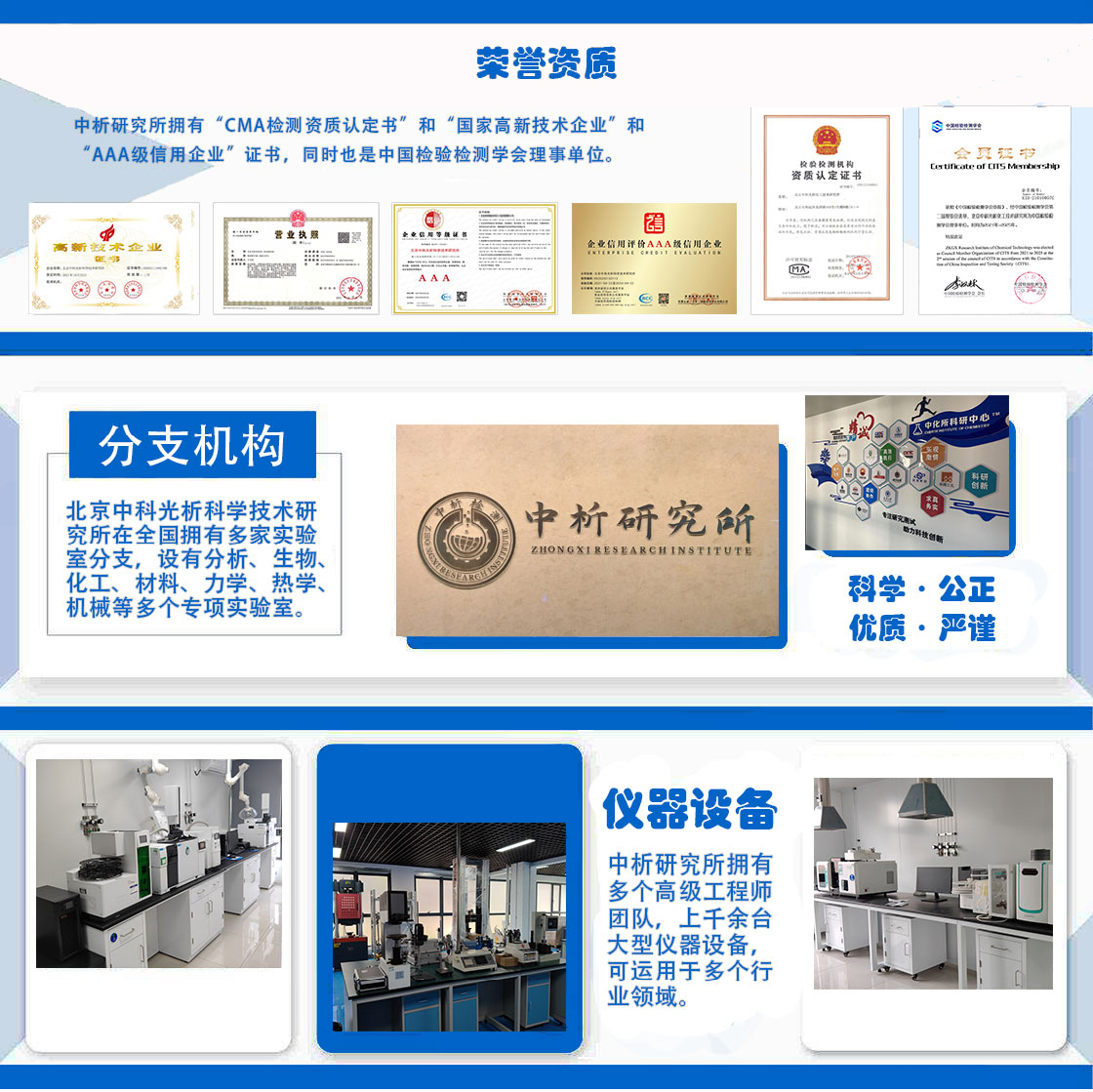
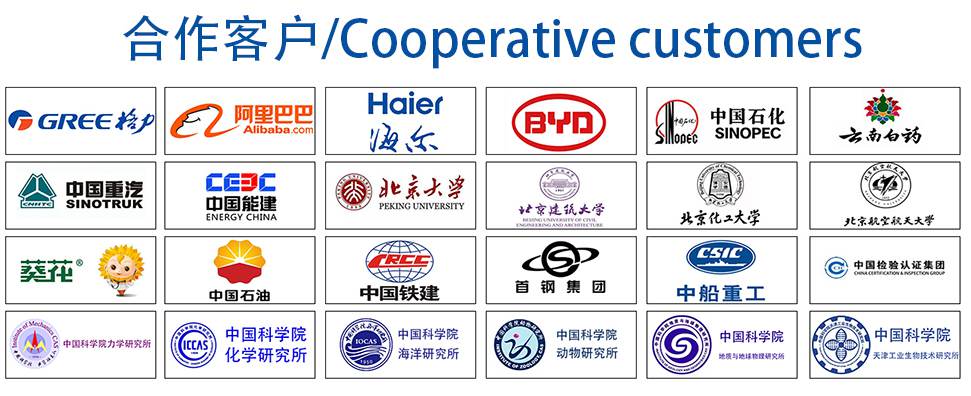