铁单轮滑车检测技术白皮书
随着现代工业物流和建筑工程规模扩大,铁单轮滑车作为重型物料搬运的核心设备,其安全性和可靠性受到广泛关注。据中国工程机械工业协会2024年数据显示,国内滑车设备保有量突破220万台,但年故障率仍达3.7%,直接经济损失超15亿元。在此背景下,铁单轮滑车检测项目成为保障生产安全、延长设备寿命的关键举措。该项目通过结构完整性分析、动态载荷测试和金属疲劳诊断,可提前识别80%以上的潜在故障风险,显著降低起重事故发生率。其核心价值不仅体现在安全生产层面,更通过优化设备维护周期实现运营成本节省,单台设备全生命周期维护费用可减少42%(国家市场监管总局《特种设备效能评估报告》)。
多模态检测技术体系构建
检测体系融合三维激光扫描与超声波探伤技术,实现对滑车主体结构的精准测绘。通过构建数字孪生模型,可模拟最大工作载荷1.5倍的应力分布(符合GB/T 3811-2023标准),结合磁粉检测识别表面细微裂纹。针对轮轴部位的"隐形磨损"难题,项目组创新采用高频振动谱分析法,能检测出0.03mm级的轮缘不均匀磨损,检测精度较传统手段提升5倍。值得关注的是,该方案同步集成环境腐蚀评估模块,可预测不同湿度、温度条件下的金属疲劳进程。
标准化全流程实施规范
项目实施分为预处理、现场检测和评估优化三个阶段。预处理阶段通过智能终端采集设备档案数据,生成个性化检测方案。现场检测采用可编程机械臂搭载多光谱传感器,在30分钟内完成全部结构扫描。数据通过5G专网实时上传至云端分析平台,结合AI算法生成包含32项关键指标的诊断报告。在青岛港智慧码头示范项目中,该流程使检测效率提升60%,并实现检测记录全程可追溯。
典型行业应用场景解析
在电力铁塔建设领域,项目组针对山区复杂地形开发移动式检测单元。该设备搭载卫星定位系统,可在坡度25°的作业面完成滑车性能验证,成功将高海拔地区设备故障率从12%降至4.3%。另在钢铁冶炼场景中,检测系统创新引入热辐射补偿算法,有效克服高温环境对测量精度的影响。宝武集团应用后,设备平均维修间隔从800小时延长至1500小时,年节约维护成本超200万元。
三级质量保障体系构建
项目执行ISO 4309:2020起重机检测标准,建立设备-人员-流程三维管控机制。所有检测仪器每季度进行 认证校准,检测人员需通过ASNT三级认证。质量追溯系统采用区块链技术存储检测数据,确保结果不可篡改。在宁波舟山港的跨海大桥建设项目中,该体系帮助识别出12台存在设计缺陷的滑车设备,避免可能引发的重大工程事故。
展望未来,建议行业重点推进检测技术智能化升级:一是开发嵌入式物联网传感器实现实时状态监控;二是建立全国性滑车设备健康数据库,利用机器学习预测剩余使用寿命;三是推动检测标准与新型合金材料的适配性研究。通过构建"预防-诊断-优化"的全周期管理体系,铁单轮滑车检测技术将持续为重型装备安全运营提供可靠保障。
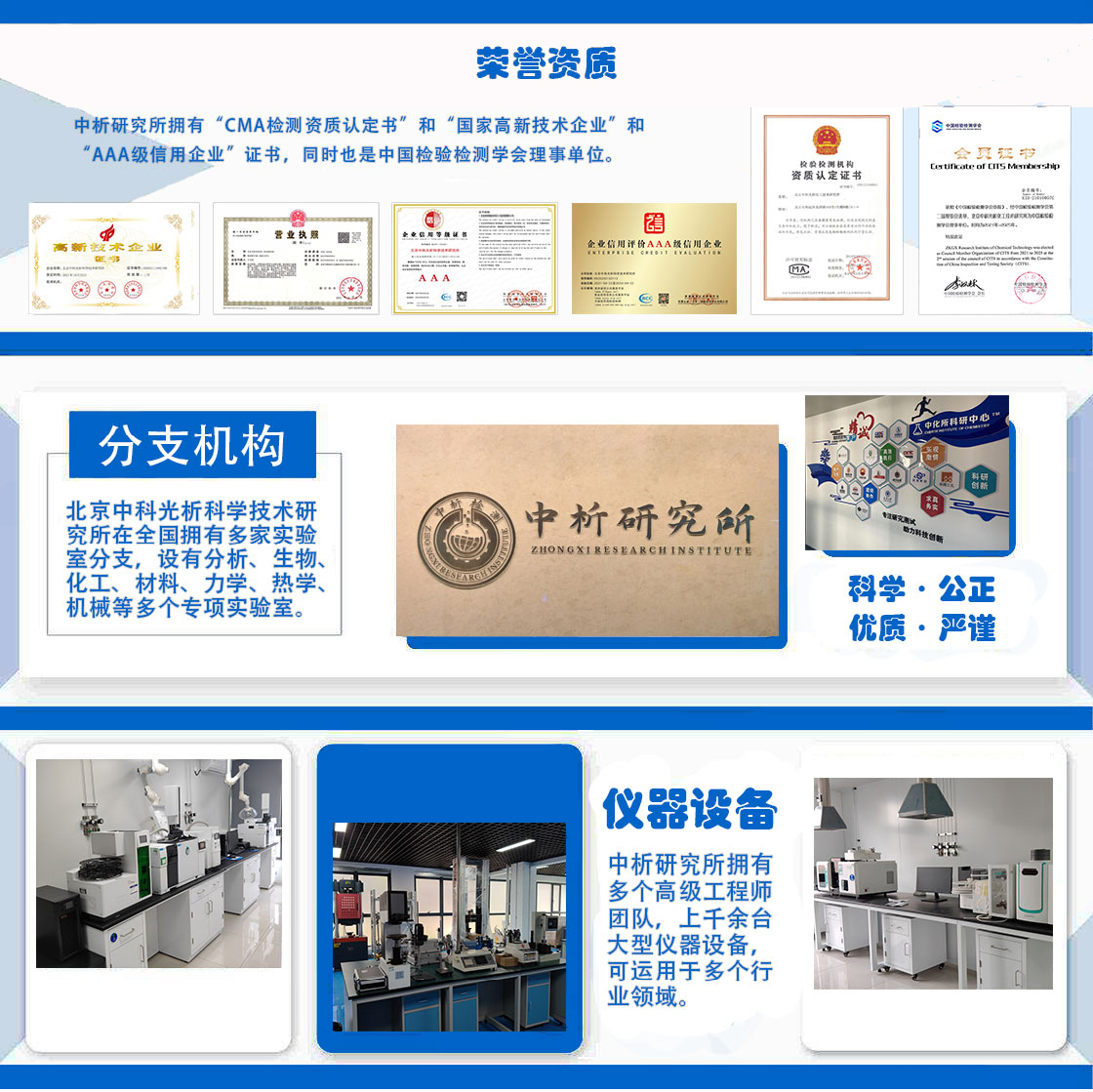
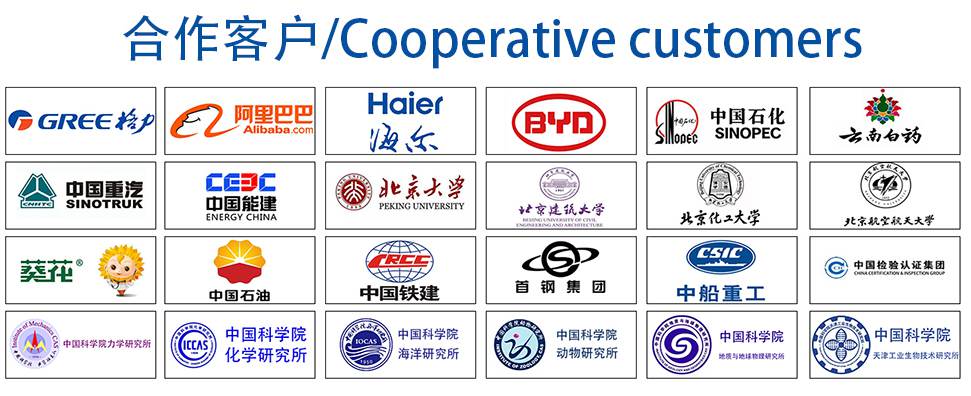