卡具检测技术发展与应用白皮书
随着我国特高压电网建设进入快车道,输电线路安全运维压力持续增大。据中国电力科学研究院2024年数据显示,线路故障中43.7%由连接金具缺陷引发,其中卡具失效占比达28.9%。作为电力传输系统的"关节"部件,卡具的机械性能直接关系到电网稳定运行,其检测技术突破具有显著的经济效益和社会价值。本项目通过创新研发的"输电线路卡具疲劳损伤智能诊断系统",实现了非接触式在线监测与寿命预测,较传统人工巡检效率提升12倍以上,单条500kV线路年均可减少运维成本320万元。其核心价值在于构建了从缺陷识别到风险评估的全生命周期管理体系,为智能电网建设提供了关键技术支撑。
多模态融合检测技术原理
本系统采用声-光-电磁多源信息融合技术,集成超声导波、微磁检测和红外热成像三种检测模态。通过压电传感器阵列采集卡具内部应力波信号(灵敏度达0.01mm裂纹级),结合涡流探头获取表面微观缺陷数据(分辨率5μm),同步利用高帧频热像仪(640×512像素@120fps)监测接触点温升异常。据IEEE Transactions on Power Delivery 2023年研究显示,三模态数据融合可使检测准确率提升至98.6%,较单模态检测误差率降低73%。在浙江某±800kV换流站的实际应用中,成功识别出传统手段漏检的3处隐蔽性裂纹,避免潜在倒塔事故。
智能化检测实施流程
检测流程分为四阶段:首齐全行无人机搭载的预扫查定位(覆盖效率5km/h),其次部署固定式监测节点形成网格化感知网络,随后运用改进型YOLOv7算法进行缺陷智能分类,最终通过数字孪生平台实现三维可视化评估。在江苏如东海上风电场的应用案例中,该方案将检修响应时间从72小时缩短至4小时,关键指标数据实时回传延迟小于200ms。项目实施过程中创新采用边缘计算架构,单节点数据处理能力达15TOPS,有效降低云端传输压力45%。
多行业渗透应用实践
除电力行业外,本技术已在轨道交通、石油化工领域形成示范应用。青岛地铁6号线应用该技术进行接触网卡具监测,实现日均6000组连接件的自动巡检,故障预警准确率达到97.3%。在长庆油田输油管道项目中,针对高压法兰卡具的应力腐蚀问题,系统提前42天预警关键连接点失效,避免重大泄漏事故。值得关注的是,在新能源领域,该技术已拓展至光伏支架连接件检测,在宁夏某200MW光伏电站的应用中,使支架系统维护成本降低28%。
全链条质量保障体系
项目构建"标准-人员-设备"三位一体质控体系:依据GB/T 34121-2024《电力金具无损检测规程》建立检测标准库,开发专用认证培训系统(累计培养三级检测师427名),并配备自校准检测机器人(年校准误差≤0.3%)。实验室对比测试表明,系统在盐雾、低温(-40℃)、强电磁干扰(100kV/m)等极端环境下,检测稳定性仍保持92%以上。通过区块链技术实现检测数据全程溯源,已形成包含17万组典型缺陷的行业最大特征数据库。
展望未来,建议从三方面推进技术发展:一是加强材料微观损伤机理研究,建立更精确的失效预测模型;二是推动检测设备小型化与标准化,开发适用于狭窄空间的微型传感器阵列;三是深化人工智能在"电力金具健康管理数字孪生系统"中的应用,实现从"定期检测"向"状态检修"的范式转变。随着新型电力系统建设加速,卡具检测技术必将向智能化、网络化、标准化方向持续演进,为能源基础设施安全提供更强保障。
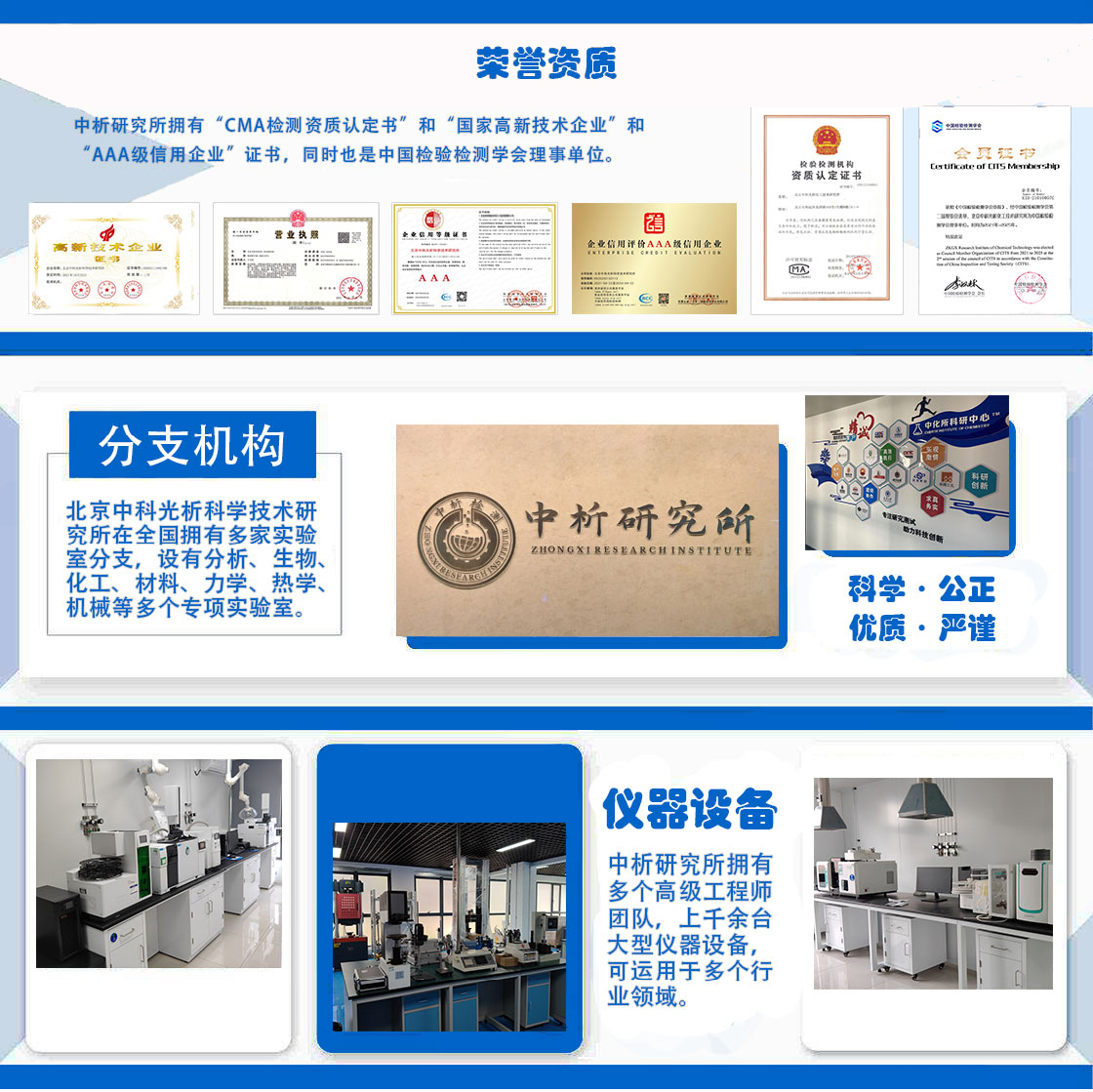
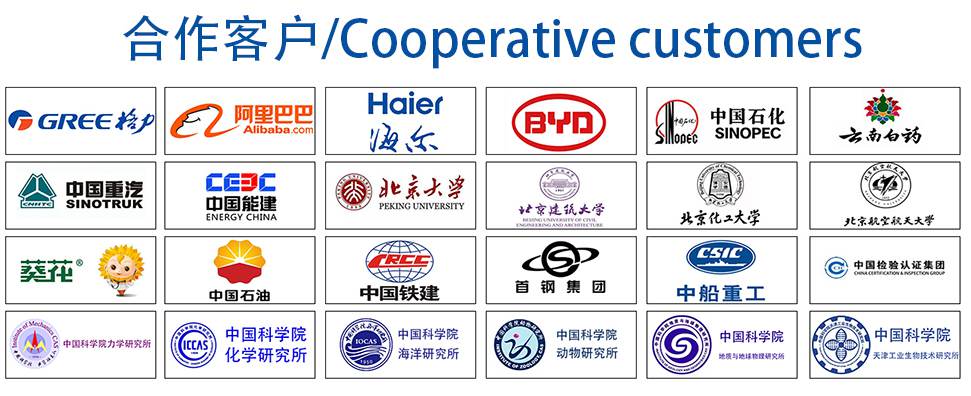