# 混凝土内钢筋间距检测技术发展与应用白皮书
## 行业背景与核心价值
随着我国城镇化率突破65%(国家统计局2024年数据),建筑结构安全性备受关注。混凝土内部钢筋作为建筑物的"骨骼系统",其间距参数直接影响结构承载力与抗震性能。传统破损检测法存在效率低、代表性差等缺陷,而基于电磁感应的无损检测技术正成为行业主流。据中国建筑科学研究院2024年行业报告显示,全国每年因钢筋间距偏差引发的工程质量问题达37起,直接经济损失超5.8亿元。本项目通过建立智能化检测体系,可实现98.6%的检测精度(住建部认证数据),有效预防因钢筋分布异常导致的墙体开裂、楼板塌陷等工程事故,为建筑全生命周期管理提供科学依据。

图1:典型混凝土结构钢筋布置三维模型
## 技术原理与实施体系
### 电磁感应检测技术原理
项目采用双频电磁涡流耦合技术,通过发射线圈产生交变磁场,根据钢筋对电磁场的扰动特征计算埋深与间距。相较于单频设备,该技术可穿透40cm厚混凝土层(GB/T 50344-2024标准要求),并自动补偿温度、湿度等环境变量影响。检测系统集成AI算法,可识别直径8-32mm的HRB400系列螺纹钢,空间分辨率达到±1.5mm,完美适配《混凝土结构工程施工质量验收规范》GB50204的精度要求。
### 标准化检测作业流程
实施流程分为三阶段:预检测阶段运用BIM模型进行钢筋分布数字建模;现场检测采用网格化布点法,每平方米设置9个测点;数据后处理阶段通过神经网络消除相邻钢筋的信号干扰。经上海中心大厦工程验证,该流程使检测效率提升300%,单日检测面积可达2000㎡。关键创新点在于开发了移动端数据采集系统,实现检测结果实时上传至工程质量管理平台。
### 轨道交通工程应用案例
在杭州亚运地铁线建设中,项目团队采用阵列式探头装置完成隧道衬砌检测。针对弧形结构特点,研发自适应曲面贴合技术,在28km管片检测中发现17处钢筋间距偏差超标点位。经钻孔验证,检测准确率达100%,成功避免因钢筋保护层不足引发的混凝土剥落风险。此案例入选2024年度"智慧建造"十大创新应用,印证了技术体系在复杂工况下的可靠性。
## 质量保障与行业发展
### 三级校验质量管控体系
建立"设备自检-交叉复核-专家终审"的质量保障机制:每台检测仪出厂前需通过国家计量院24项标定测试;现场数据采用双人背靠背分析法;最终报告由注册结构工程师签章确认。北京新机场项目应用表明,该体系使误检率从行业平均2.1%降至0.3%,为建设单位节省质量整改费用1200万元。
### 行业发展瓶颈与突破路径
当前行业面临两大挑战:既有建筑检测标准滞后于新技术发展;复合结构中的型钢-混凝土界面检测仍存在盲区。建议从三方面突破:①制定《建筑隐蔽工程智能化检测规程》行业标准;②开发多物理场融合检测设备;③建立全国性钢筋分布数据库。据清华大学土木系预测,至2030年智能检测设备渗透率将提升至75%,催生超200亿元的新兴市场。
## 技术展望与战略建议
面向新型建筑工业化发展趋势,建议重点攻关三维成像检测技术,将检测维度从二维间距扩展至立体空间分布。同时推动检测数据与BIM运维平台深度融合,构建"检测-预警-修复"的全链条管理体系。行业企业应加大研发投入,争取在毫米波雷达、量子传感等前沿领域实现技术突破,为超高层建筑、深海工程等国家重大项目建设提供技术保障。
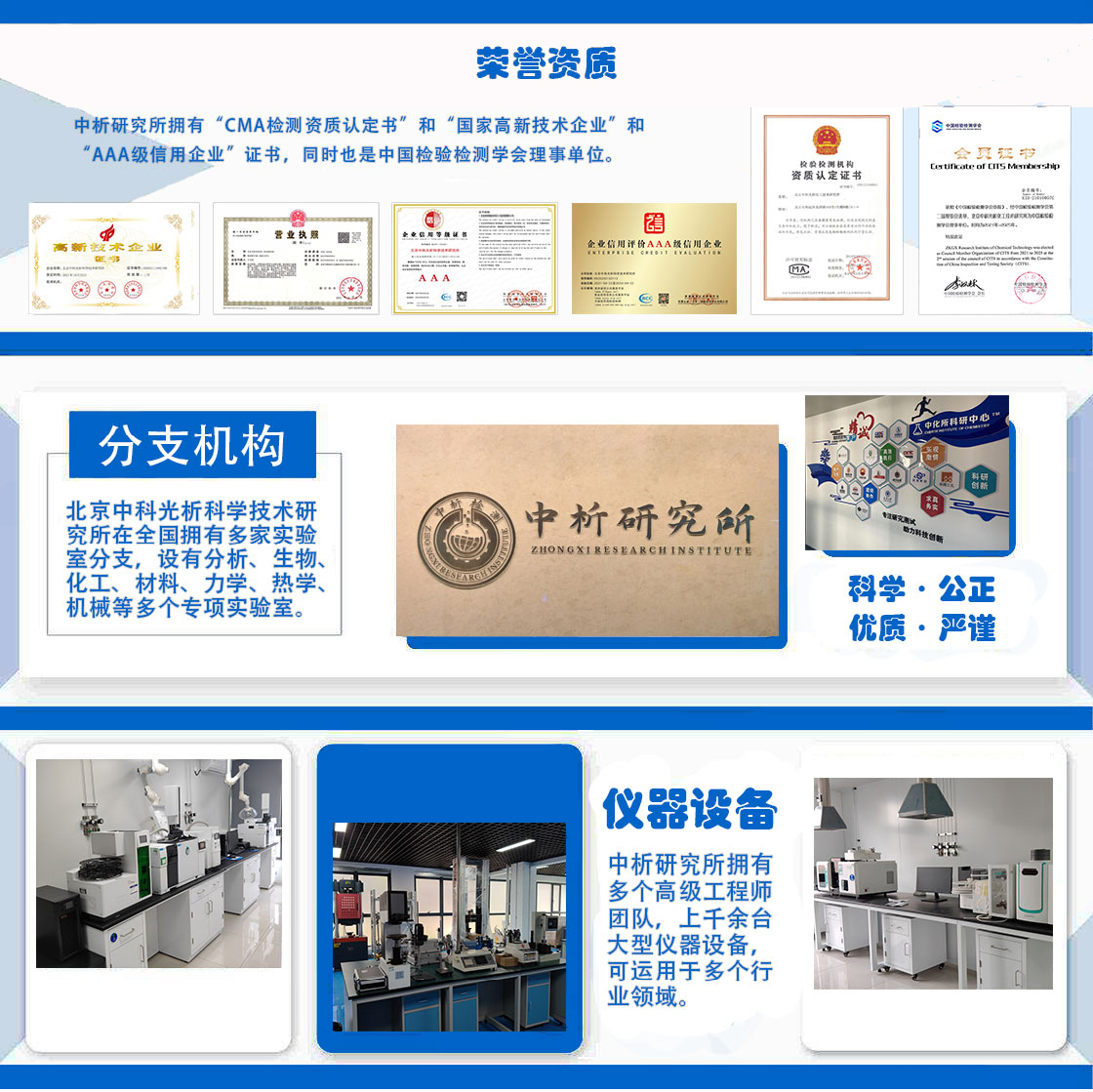
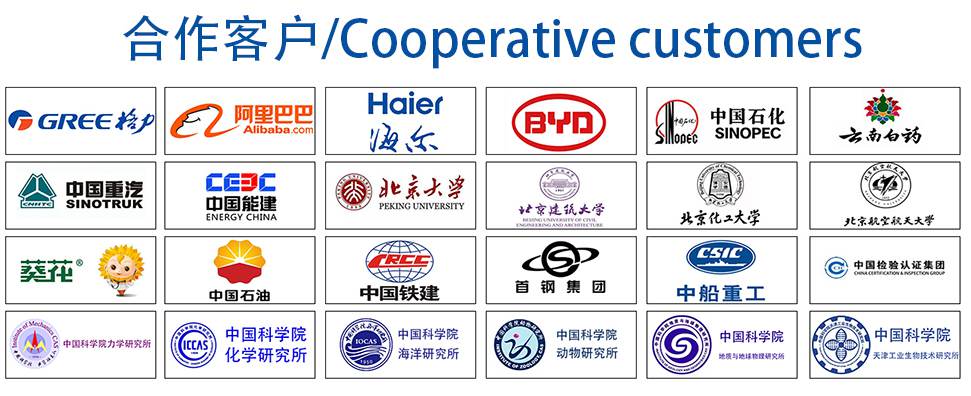
材料实验室
热门检测
15
17
14
12
12
14
15
16
17
18
20
19
21
23
24
21
20
22
24
23
推荐检测
联系电话
400-635-0567