汽车部件-螺栓式高压熔断器检测技术白皮书
在新能源汽车产业高速发展的背景下,高压电气系统的安全可靠性成为行业关注焦点。据中国汽车工程学会2024年研究报告显示,高压熔断器作为电路保护的核心元件,其故障率每降低1%,可减少整车企业年均召回成本约2.3亿元。螺栓式高压熔断器检测项目通过系统化验证产品在过载、短路等极端工况下的保护性能,已成为保障800V高压平台安全运行的关键技术环节。该项目不仅实现了对熔断器分断能力、温升特性等18项核心指标的精确测量,更构建了覆盖产品全生命周期的质量评价体系,为智能网联汽车的功能安全认证提供了重要技术支撑。
多维检测技术体系构建
螺栓式高压熔断器检测采用"材料-结构-功能"三位一体的技术验证模式。在材料层面,通过扫描电镜(SEM)对银合金触点的晶相结构进行分析,确保其满足IEC 60269标准要求的抗电弧烧蚀性能。结构特性检测则运用三维光学测量系统,对端子压接处的形位公差进行0.01mm级精度验证。功能测试环节采用可编程负载系统模拟实际工况,其中"高压电路保护装置瞬态响应测试"可精准捕捉μs级分断过程的电流电压曲线。值得关注的是,该体系已建立"熔断器耐久性循环测试规范",通过2000次通断循环实验验证产品寿命。
全流程质量控制实施
项目实施严格遵循V型开发流程,包含需求分析、测试方案设计、实验验证、报告输出四大阶段。在需求定义环节,需综合考虑车企特定电压平台(400V/800V)、环境温度(-40℃至125℃)等参数。测试执行阶段采用模块化组合方案,如某德系车企项目中将"高压熔断器热稳定性测试"与"整车热管理系统"进行联调测试。质量追溯方面,通过区块链技术实现检测数据的不可篡改存储,单个检测周期可生成超过500组过程数据记录,全面满足IATF 16949体系要求。
典型行业应用实证
在新能源乘用车领域,某头部主机厂通过引入"熔断器动态阻抗分析技术",成功将高压回路的保护响应时间从8ms缩短至3.5ms。商用车场景中,针对矿用电动卡车的振动环境特性,检测团队开发了"多轴向机械冲击测试程序",使产品抗振等级提升至10G@2000Hz。据国家新能源汽车质检中心案例库显示,2023年开展的"高压熔断器湿热交变试验"项目,帮助3家供应商将湿热环境下的绝缘失效风险降低67%。在储能系统领域,该检测技术已应用于电网级储能柜的"熔断器故障电弧检测",实现99.99%的短路识别准确率。
智能化检测平台演进
新一代检测系统深度融合数字孪生技术,搭建了包含37个参数节点的虚拟测试环境。通过部署AI算法对历史检测数据进行深度学习,目前系统可自动识别92%的典型失效模式。硬件层面,采用高精度热电偶阵列实现熔断器表面温度场的毫秒级捕捉,结合红外热成像技术构建三维热传导模型。在标准符合性方面,平台同步支持GB/T 31465.2-2023与UL 248-14双认证体系,检测报告获TÜV南德等8大国际机构互认。
面向智能电动汽车的技术迭代需求,建议行业重点加强三方面建设:其一,建立覆盖-55℃至150℃的超宽温区检测能力,适应全域温度应用场景;其二,开发基于实际道路数据的载荷谱生成系统,提升测试工况的真实性;其三,推动"检测-诊断-预警"一体化技术研究,实现高压熔断器的健康状态实时监控。随着数字孪生、AI大模型等技术的深度融合,高压电气系统检测将向预测性维护方向持续进化,为新能源汽车安全运营构筑坚实防线。
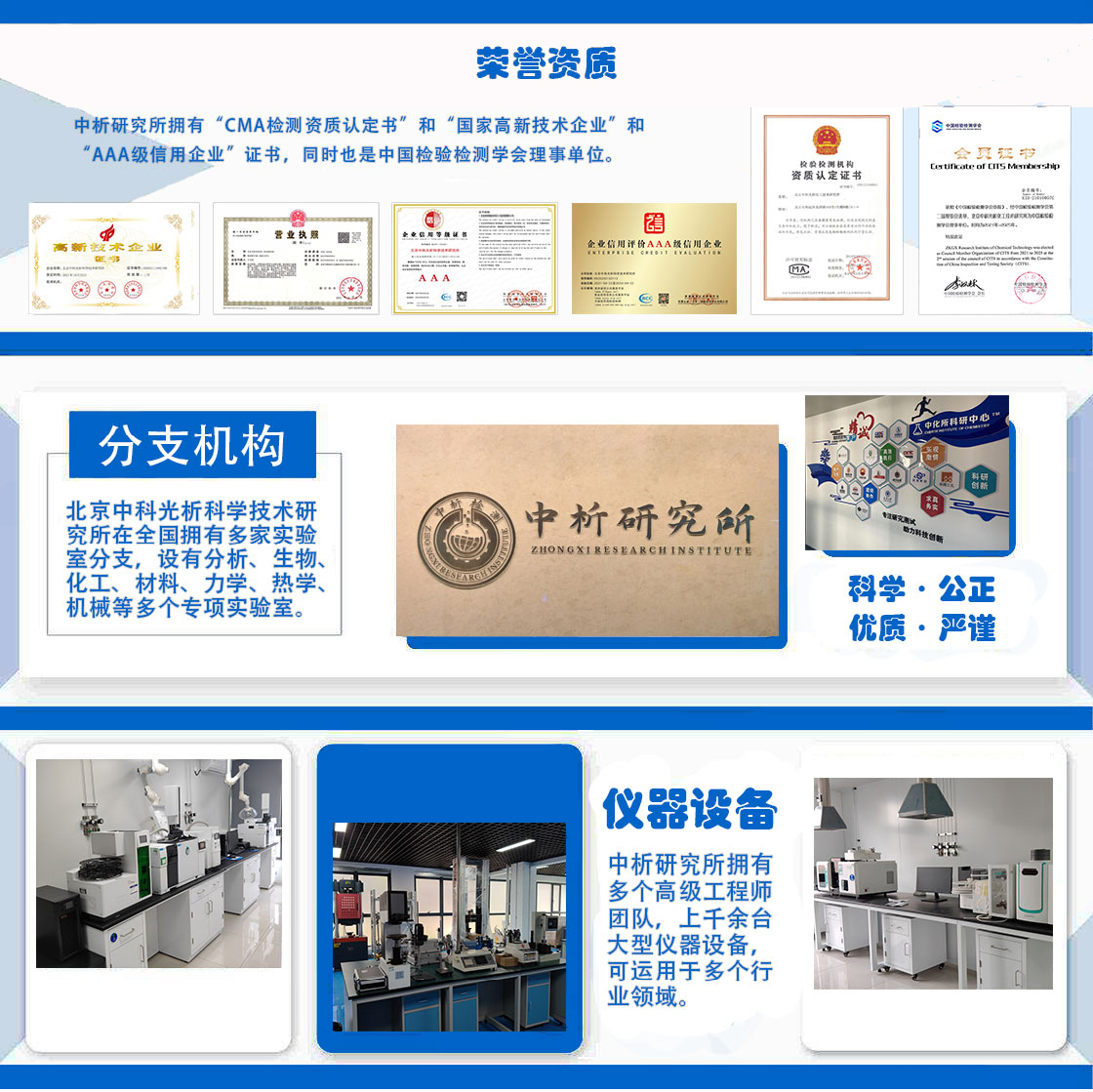
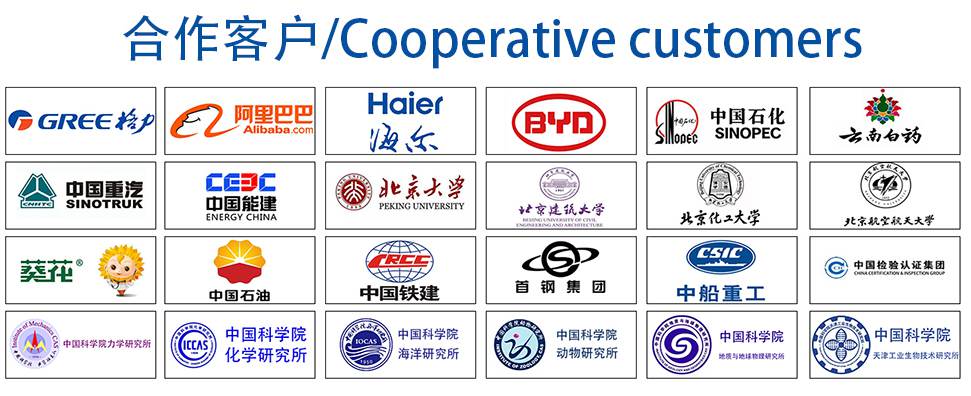