(一)常规检测项目
-
- 表面腐蚀:检查导线表面氧化、锈蚀、镀层脱落等现象,需记录腐蚀面积与深度。
- 断股与磨损:利用目视或高倍放大镜观察单股线断裂情况,重点检测悬垂线夹、耐张线夹等易磨损部位。
- 异物缠绕:排查鸟类筑巢、塑料薄膜等异物引发的短路或机械损伤风险。
-
- 直径与节距:使用卡尺或激光测距仪测量绞线整体直径及绞合节距,判断是否符合设计要求。
- 绞合均匀性:分析各层绞线的排列是否紧密,是否存在松散或跳股现象。
-
- 拉伸强度:通过拉力试验机抽样测试绞线的抗拉强度,验证其承受设计荷载的能力。
- 扭转性能:模拟绞线在风振或覆冰荷载下的扭转疲劳特性。
-
- 直流电阻:测量单位长度导线的电阻值,判断导体材料是否劣化。
- 绝缘电阻(若适用):针对带绝缘层的架空绞线,检测绝缘性能是否达标。
(二)专项检测项目
-
- 超声波检测:利用超声波探伤仪检测绞线内部断股、裂纹等隐蔽缺陷,适用于钢芯铝绞线(ACSR)的钢芯检测。
- 红外热成像:通过红外测温仪监测导线连接点、线夹等部位的异常温升,识别接触不良或过载热点。
- 紫外成像技术:检测电晕放电现象,定位绝缘子或导线表面因损伤导致的局部放电。
-
- 金相显微镜检测:截取腐蚀样本,观察金属微观组织变化,评估腐蚀对材料强度的影响。
- 化学元素分析:采用X射线荧光光谱(XRF)或能谱分析(EDS),确定腐蚀产物的成分及来源。
-
- 长期应变监测:安装光纤传感器或应变片,实时监测绞线在长期荷载下的蠕变变形。
- 振动疲劳试验:模拟风振条件下绞线的疲劳寿命,预测断股风险。
-
- 盐雾试验:评估沿海或工业污染区域绞线的耐盐雾腐蚀能力。
- 低温脆性试验:针对高寒地区应用场景,测试材料在低温下的韧性。
-
- 现象:某500kV输电线路因覆冰导致钢芯铝绞线断股。
- 检测:无人机巡检发现断股点,超声波检测确认钢芯未受损。
- 措施:采用预绞式修补条进行局部加固,避免导线截面积损失。
-
- 现象:化工园区架空线表面出现点状腐蚀。
- 检测:化学分析显示腐蚀产物含硫化合物,判定为工业废气侵蚀。
- 措施:喷涂防腐涂层并加装耐酸雨绝缘护套。
-
- 现象:导线接头处温度异常升高。
- 检测:红外热成像显示局部温度达120℃,远超安全阈值。
- 措施:更换螺栓型线夹为液压型,降低接触电阻。
- 智能化监测:集成物联网(IoT)传感器,实现绞线应力、温度、振动的实时在线监测。
- 无人机与AI结合:利用无人机搭载高分辨率相机与AI算法,自动识别断股、腐蚀等缺陷。
- 材料寿命预测:基于大数据建立绞线老化模型,精准评估剩余使用寿命。
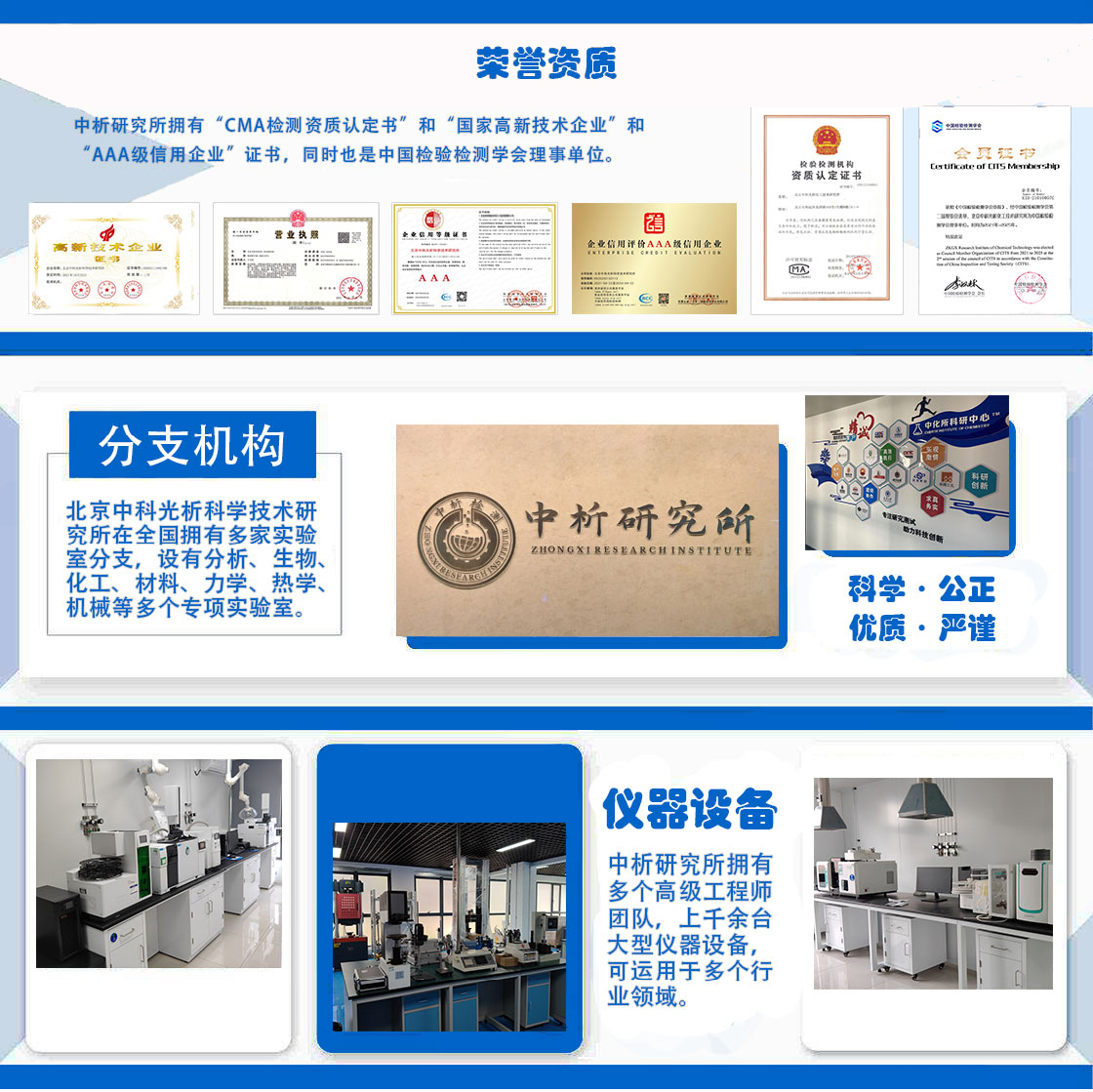
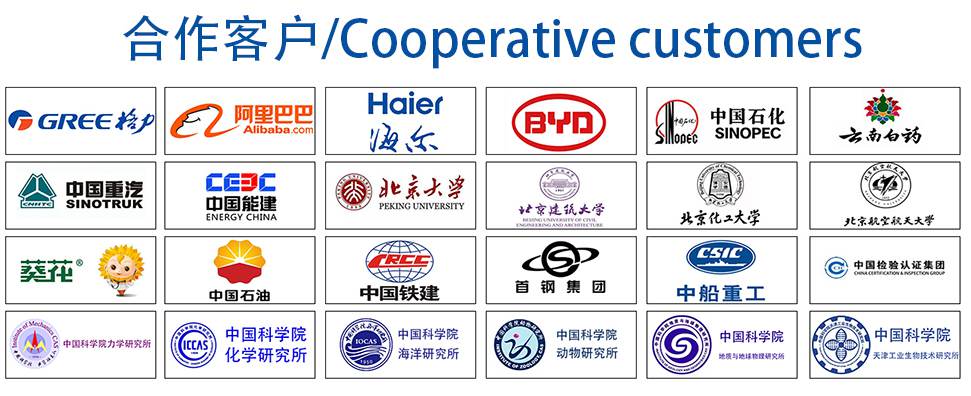
材料实验室
热门检测
207
172
154
176
169
171
179
175
170
185
179
167
172
170
161
163
172
166
175
174
推荐检测
联系电话
400-635-0567