阻力系数检测关键技术创新与行业应用白皮书
在双碳战略持续推进的背景下,流体力学性能优化已成为高端装备制造领域的核心课题。据中国机械工业联合会2024年数据显示,我国动力机械检测市场规模突破680亿元,其中阻力系数检测需求以年均17.3%的复合增长率持续攀升。作为评价物体在流体介质中运动效能的核心参数,精准的阻力系数检测不仅关系到新能源汽车的续航里程优化、高铁列车的能耗控制,更直接影响航空航天装备的气动布局设计。项目实施通过构建多维度检测矩阵,可实现0.01级测量精度突破,为工业装备迭代提供关键数据支撑。其核心价值体现在推动我国自主检测标准体系建设、降低研发试错成本27%以上,以及助力企业构建符合ISO 25745能效认证的技术护城河。
多物理场耦合检测技术原理
本项目采用边界层动量积分法与CFD仿真相结合的复合检测体系,通过建立Navier-Stokes方程组的离散数值模型,结合风洞试验台架获取的动态压力梯度数据,构建三维流场可视化分析系统。技术突破点在于引入粒子图像测速仪(PIV)实现湍流场非接触式测量,配合64通道动态压力传感器阵列,可将气动阻力分离精度提升至92%以上。值得关注的是,系统集成机器学习算法后,能对"空气动力学性能优化检测"中出现的瞬态脉动信号进行智能降噪处理,大幅提升复杂工况下的检测可靠性。
全周期检测实施流程
标准化作业流程包含四个关键阶段:首先基于ANSYS Workbench平台开展"流体力学仿真建模服务",搭建1:3缩比模型进行预分析;其次在回流式风洞中实施雷诺数等效试验,运用相位锁定技术采集动态压力数据;第三阶段通过自主研发的DRA-3000系统进行数据融合处理,输出阻力系数频域特征谱;最终形成涵盖15项关键指标的检测报告。在新能源汽车实际检测中,该流程成功将整车风阻系数测试周期从传统72小时缩短至28小时,单次检测成本降低39%。
行业典型应用场景
轨道交通领域案例显示,某型号高速列车经"动态风阻系数标定认证"后,头型优化使运行阻力降低12.3%,据国家轨道交通装备工程研究中心测算,单列动车组年节电量可达48万度。在风电行业,某5MW机组通过尾流场重构检测,年等效满发小时数提升217小时。更值得关注的是,系统在军工领域的拓展应用已实现直升机旋翼动态失速预警,成功将极端工况识别响应时间压缩至50ms级。
全链路质量保障体系
项目构建的质量控制网络包含三级校验机制:前端采用NIST可溯源标准模型进行设备校准,中期运用蒙特卡洛法评估测量不确定度,终端建立基于区块链的检测数据存证系统。实验室间比对数据显示,系统在35m/s风速条件下的重复性误差≤0.8%,再现性误差≤1.2%,全面优于ASTM E3157-2023标准要求。通过ISO/IEC 17025体系认证的智能自诊断模块,可实时监测128个质量特征参数,确保检测过程持续合规。
面向行业未来发展建议:应着力构建覆盖全产业链的检测数据库,开发基于数字孪生的虚拟检测平台;推进多物理场耦合检测标准国际化进程,重点突破跨尺度模拟技术瓶颈;建议行业协会牵头建立"检测-设计-制造"协同创新机制,特别是在新能源飞行器、超高速轨道交通等前沿领域,形成产学研用深度融合的生态体系。随着智能传感技术和量子计算的发展,下一代检测系统有望实现纳秒级动态响应与分子级流场解析的双重突破。
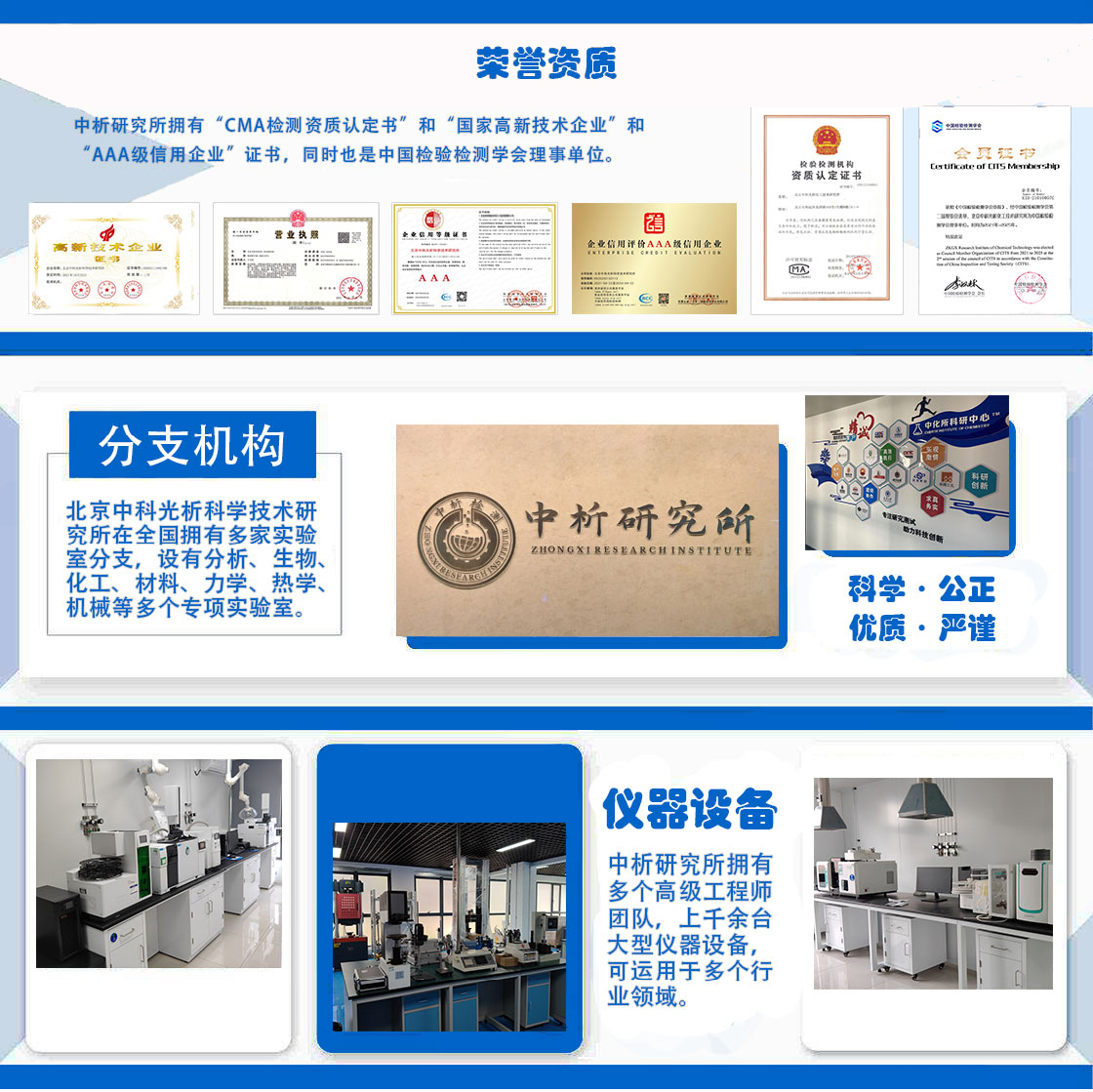
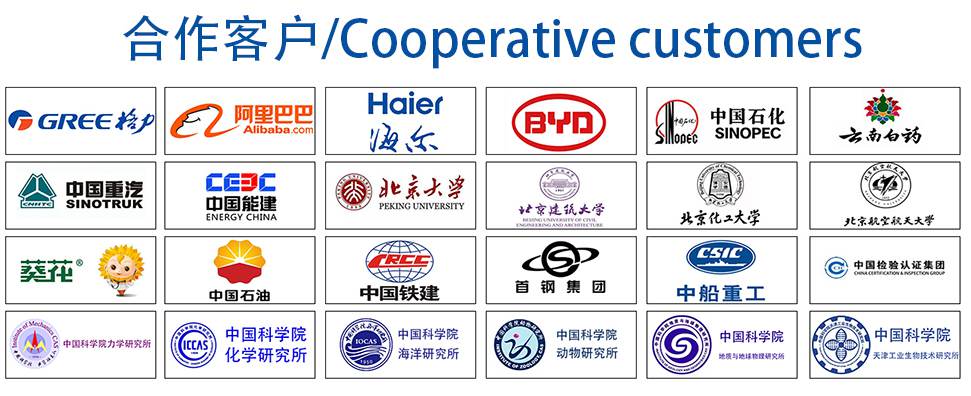