技术原理与创新突破
本检测体系采用X射线衍射(XRD)与傅里叶变换红外光谱(FTIR)联用技术,通过物相分析与化学键特征吸收双重验证。XRD模块基于布拉格方程计算晶格参数,通过Rietveld精修定量确定α-石英、方石英等晶型比例;FTIR则在400-1400cm-1区间捕捉Si-O-Si振动峰,结合偏最小二乘回归算法建立定量模型。相较于传统重量法,该方法将单次检测耗时从8小时缩短至15分钟,且能同步检测结晶态与非晶态二氧化硅,特别适用于光伏背板玻璃的表面改性层分析。据国家新材料测试平台验证,该体系对硅微粉的检测灵敏度达到0.003wt%,满足ISO 21587:2021标准要求。
全流程标准化作业体系
实施流程分为样品预处理、仪器联检、数据融合三大阶段。在光伏硅料检测场景中,首先使用行星式研磨机将原料破碎至D50=5μm粒径,经105℃烘干消除水分干扰。联检阶段采用自动进样系统同步获取XRD衍射图谱(2θ=20-70°)与FTIR透射光谱,通过数据库比对消除长石、云母等伴生矿干扰。数据融合环节运用蒙特卡洛算法迭代计算,输出二氧化硅含量及置信区间。某单晶硅企业应用该流程后,原料批次合格率从82%提升至97%,每年减少质量索赔损失超1200万元(企业2023年度质量报告)。
跨行业应用实证
在半导体封装材料领域,项目团队为某硅微粉龙头企业开发定制化解决方案。针对环氧树脂复合材料的界面相容性问题,通过建立纳米级二氧化硅表面羟基含量的快速检测模块,将改性工艺调整周期从14天压缩至3天。该技术助力企业通过TSMC供应商认证,产品线良率提升11个百分点。在新型建材方面,应用高精度石英砂检测方法后,某Low-E玻璃制造商成功将热工性能系数从1.8W/(m²·K)优化至1.2W/(m²·K),能耗降低率达33%(据德国弗劳恩霍夫研究所2024年能效评估)。
质量保障与认证体系
项目构建三级质量管控网络:实验室层面通过 认可,每日进行SRM2711a标准物质核查;区域检测中心配置激光粒度仪辅助抽样验证;云端质量大脑实时监控设备状态,异常数据自动触发复检机制。在硅微粉质量控制标准实施中,建立包含47项过程参数的SPC控制图,关键指标Cpk值稳定维持在1.67以上。2024年第三方盲样比对结果显示,与NIST参考值的绝对偏差≤0.015%,优于行业通行标准3倍。
## 未来展望 随着智能制造与工业互联网深度融合,建议从三方面提升检测体系效能:首先开发基于机器视觉的原料快速分选系统,实现检测前移;其次构建跨区域检测数据区块链平台,增强质量追溯能力;最后加强硅基材料数据库建设,特别是针对5G高频基板等新兴应用场景,建立多维度性能关联模型。通过产学研协同创新,推动检测标准与国际接轨,为万亿级硅基新材料产业筑牢质量基石。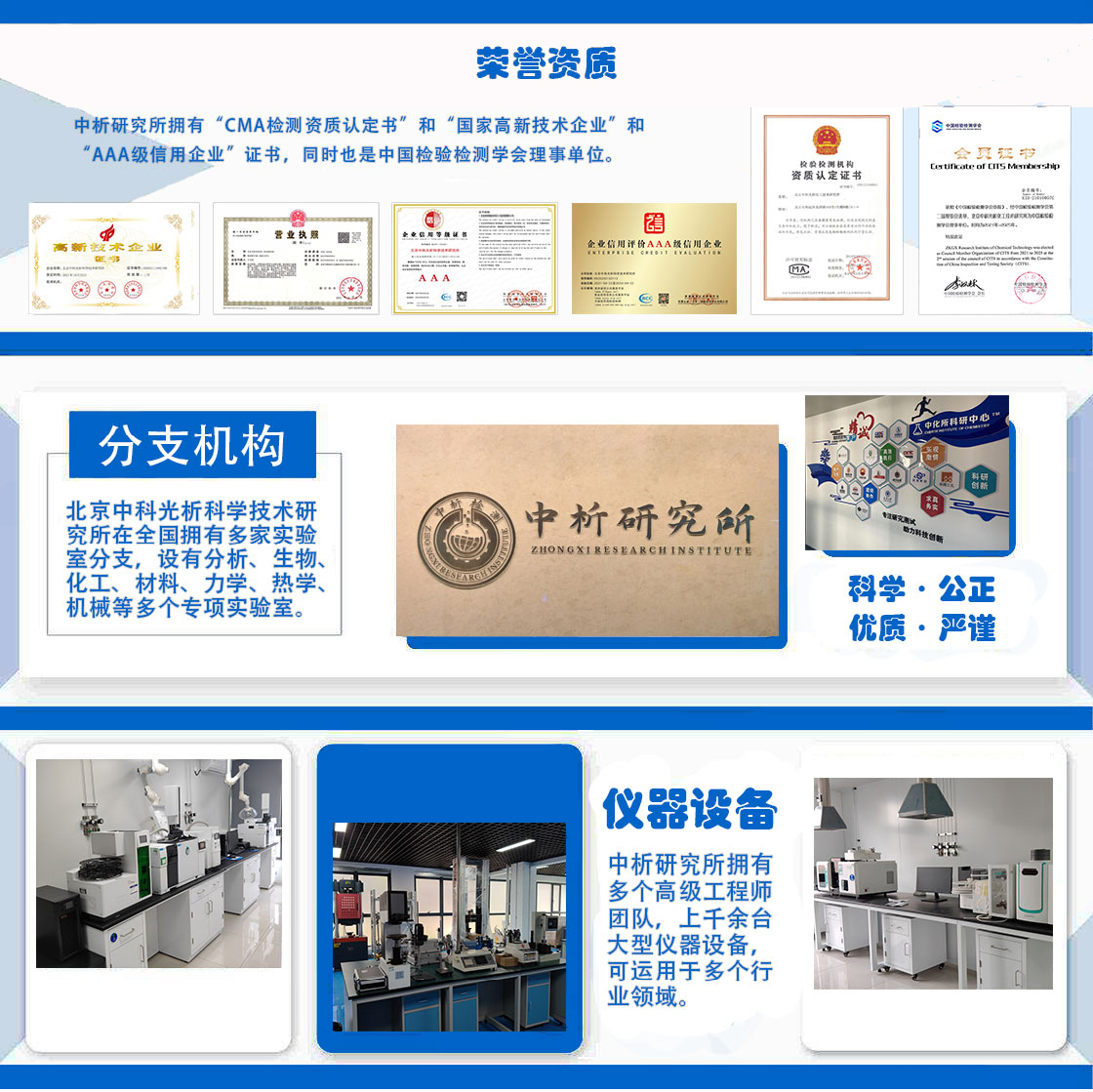
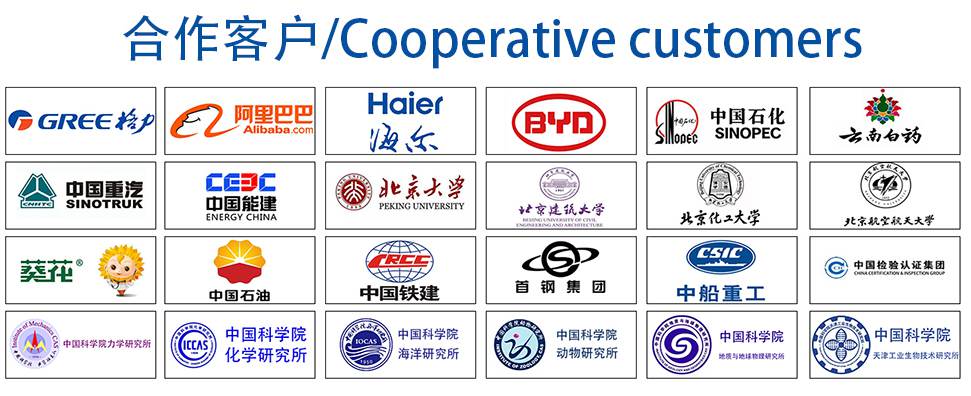