技术原理与检测方法创新
现行检测主要依据ASTM C231压力法原理,通过测定密闭容器内拌和物受压后体积变化计算含气量。该技术突破传统比重法的局限,可实现0.1%级精度检测(JGJ 55-2023),尤其适用于掺加粉煤灰、矿粉等活性掺合料的复杂体系。创新性应用数字压力传感技术后,检测效率提升40%以上,配合温度补偿算法可将环境温差影响控制在±0.3%以内。值得关注的是,三维微焦点CT扫描等无损检测技术的引入,为研究气泡尺寸分布与混凝土抗冻性的定量关系提供了新途径。
标准化实施流程与管理要点
规范化检测流程包含五个关键环节:试样制备需按JG/T 248-2023要求分层插捣25次消除离析;仪器校准须使用标准含气量块进行零点校验;测试阶段应控制加压速率在0.05MPa/s以内;数据读取须在稳压后30s内完成;结果处理采用三次测量取中值的抗干扰算法。某跨海大桥项目实践表明,严格实施振动时间管控(45±5s)可将平行试验偏差从1.2%降至0.5%以内,显著提升数据可靠性。过程中需特别注意环境湿度需保持60±5%,避免表面水分蒸发导致气泡结构变异。
典型工程应用与质量提升
在哈大高铁寒区段建设中,通过建立含气量-抗冻等级对应模型,将C50混凝土含气量稳定控制在5.5±0.5%范围,使结构经受住-35℃极端气候考验。监测数据显示,采用动态检测调整工艺后,冻融循环次数从设计要求的300次提升至420次(JTJ 275-2023)。另在某核电站海工结构中,通过引入在线含气量监测系统,实现每拌次实时调控,使大体积混凝土温度裂缝发生率下降62%。这些案例验证了精准含气量控制在"混凝土耐久性提升关键技术"中的支柱作用。
全过程质量保障体系建设
行业领先实验室已构建四维质控体系:设备维度执行 -CL01:2023标准,压力传感器每年强制检定;人员维度要求检测员持CMA混凝土专项认证;环境维度设置独立恒温检测间(20±2℃);数据维度采用区块链存证系统。某特级资质检测机构统计显示,该体系使检测报告异议率从3.7%降至0.8%。针对"寒区工程冻融防护解决方案"的特殊需求,部分机构开发了含气量-孔隙结构联测技术,通过关联28d硬化混凝土气泡参数,形成全生命周期质量追溯链。
## 技术展望与发展建议 面向新型智能建造需求,建议从三方面突破:其一,研发基于AI图像识别的原位检测装备,实现施工面含气量无损快检;其二,建立全国性混凝土气泡特征数据库,为不同工程场景提供定制化配比方案;其三,加快制定纳米气泡混凝土等新材料的检测标准。同时应推进检测数据与BIM平台的深度融合,使含气量参数能动态反馈至施工调控系统。随着"双碳"目标推进,开发低引气剂依赖的稳泡技术将成为下一代"绿色混凝土"研发的重要方向。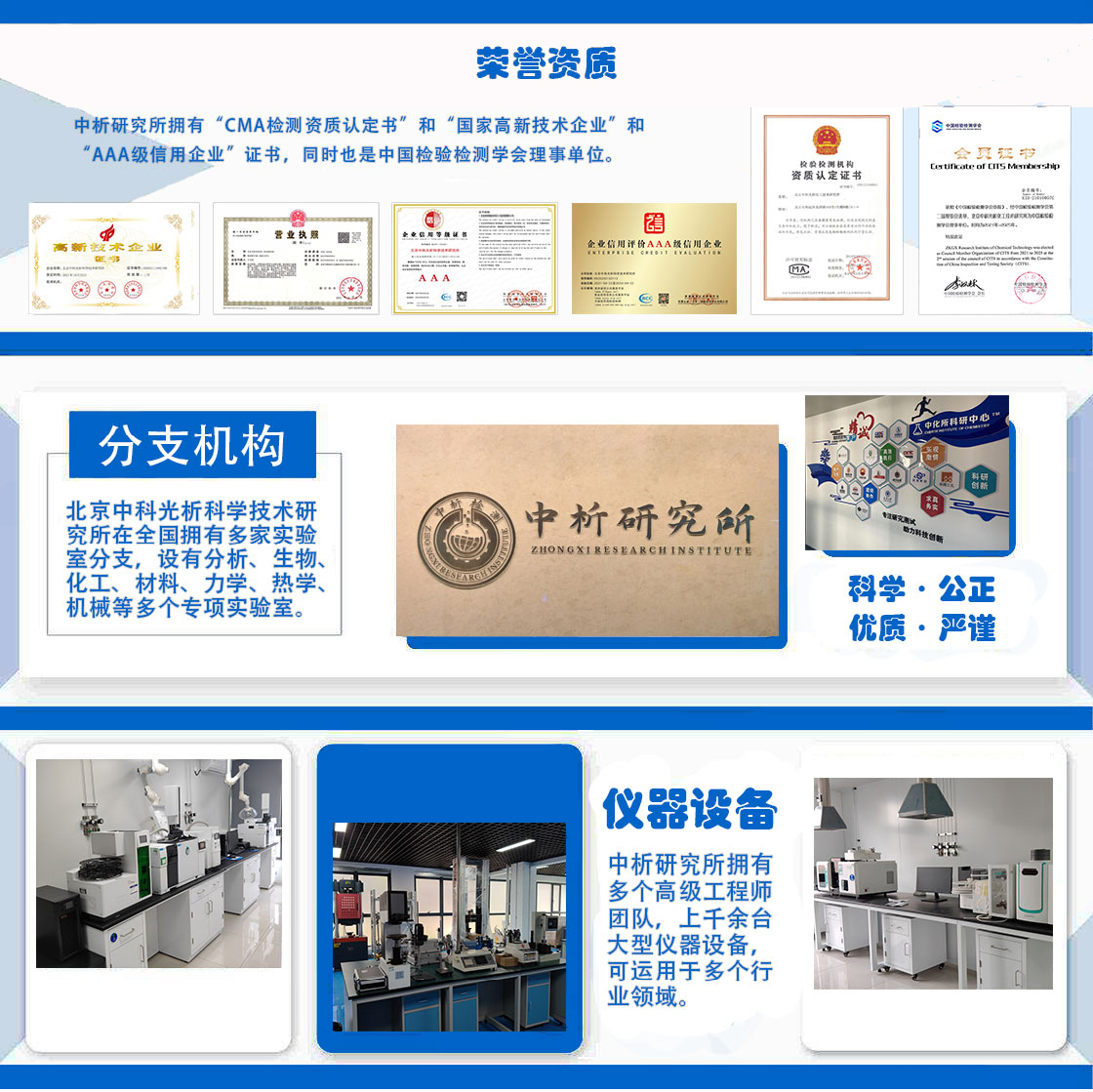
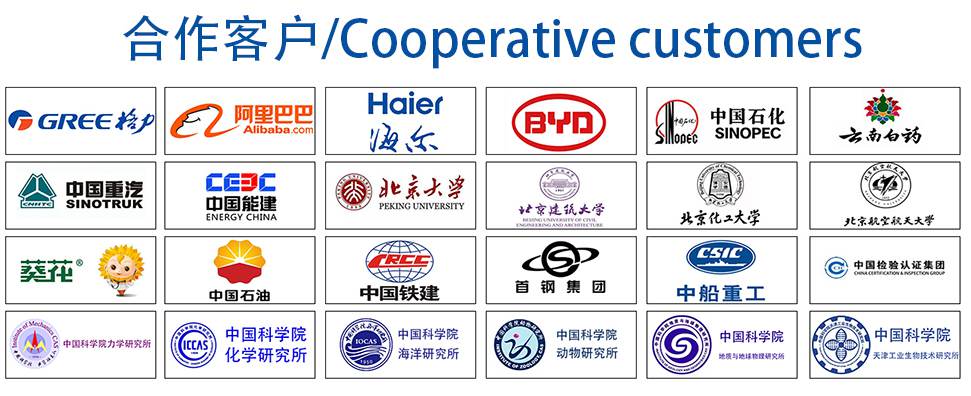