超逊径颗粒含量检测技术规范
一、引言
二、检测项目及意义
1. 超径颗粒含量检测
- 定义:超径颗粒指粒径大于标准允许最大粒径(如骨料中的最大公称粒径)的颗粒。
- 检测目的: 判定材料中超标大颗粒的比例,避免因超径颗粒过多导致空隙率增大、施工性能下降(如混凝土离析)。
- 允许误差:根据标准(如GB/T 14685《建设用碎石、卵石》),超径含量通常要求≤5%。
2. 逊径颗粒含量检测
- 定义:逊径颗粒指粒径小于标准允许最小粒径的颗粒(如砂粒中小于0.075mm的泥粉)。
- 检测目的: 控制细粉含量,防止逊径颗粒过多影响材料结合能力(如混凝土需水性增加、强度降低)。
- 允许误差:逊径含量一般要求≤10%,具体依材料类型调整。
3. 级配连续性分析
- 检测内容: 通过筛分曲线评估颗粒分布的连续性,判断是否存在某一区间粒径过度缺失或富集。
- 异常影响:级配断档会导致材料密实度不足,降低整体结构稳定性。
4. 筛分效率验证
- 附加项目: 验证筛分设备精度是否符合标准(如方孔筛的孔径误差≤±1%),排除设备因素导致的检测偏差。
三、检测方法
1. 试验设备
- 标准方孔筛(符合GB/T 6003.1要求)
- 电子天平(精度0.1g)
- 振筛机(频率可调)
- 烘箱(105±5℃)
2. 操作流程
- 样品制备:
- 取代表性试样(如骨料按四分法缩分至3~5kg),烘干至恒重。
- 分级筛分:
- 自上而下按孔径由大到小叠加筛组,手动或机械振筛10~15分钟。
- 称量计算:
- 逐级称量各筛余质量,计算超径颗粒质量占比(超径率)和逊径颗粒质量占比(逊径率)。
3. 数据对比
- 将筛分结果与国家标准或行业规范(如JTGE42《公路工程集料试验规程》)中的级配范围对比,判定是否合格。
四、检测质量控制要点
- 取样代表性
- 避免在料堆顶部或底部取样,采用分层随机取点法减少偏差。
- 筛分操作规范
- 筛分时间不足会导致细颗粒残留,时间过长可能造成颗粒破碎。
- 环境因素控制
- 潮湿试样需预先烘干,防止细颗粒黏附影响精度。
五、应用案例(以混凝土粗骨料为例)
- 超径颗粒(>20mm)占比6.2%(超标),需增加二次筛分工序;
- 逊径颗粒(<5mm)占比3.5%(合格),可直接用于生产。
六、
- GB/T 14685-2022 建设用碎石、卵石
- ASTM C136/C136M-2014 细、粗骨料筛分试验方法
- JTG E42-2005 公路工程集料试验规程
上一篇:圆柱顶破强力检测下一篇:抑制骨料碱活性效能试验检测
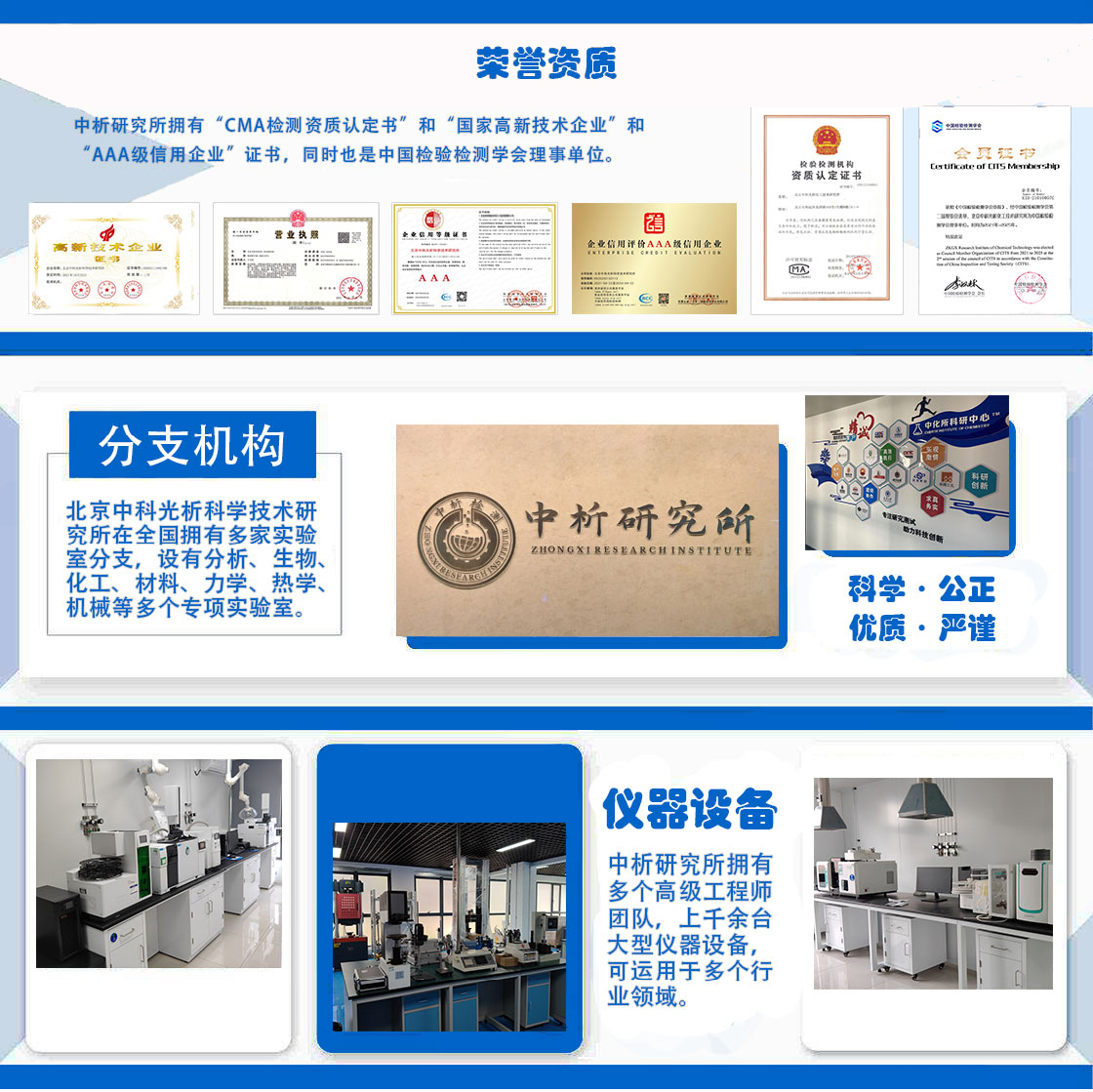
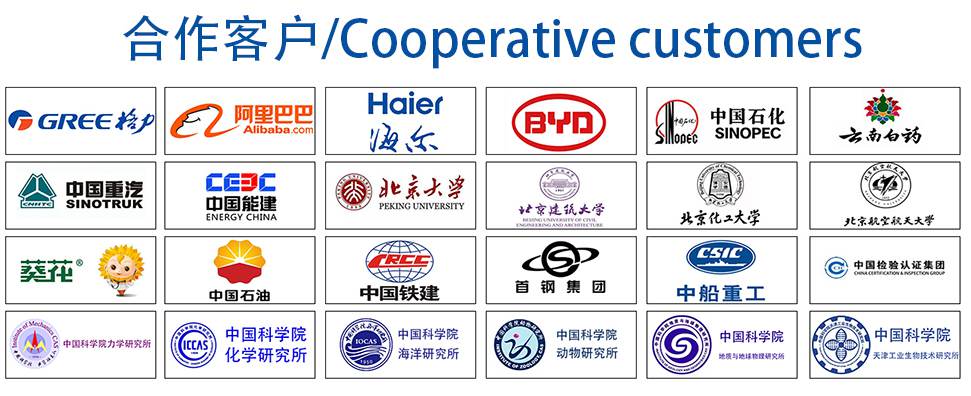
材料实验室
热门检测
202
171
152
174
165
167
178
174
167
182
174
163
170
166
159
161
169
162
174
172
推荐检测
联系电话
400-635-0567