强度比检测:构筑材料安全的核心防线
在工业4.0与智能制造深度融合的背景下,材料性能检测已成为制造业高质量发展的关键环节。据中国材料科学研究院《2024齐全制造白皮书》显示,每年因材料强度不足导致的工业事故损失超1200亿元,其中35%的失效案例与强度比参数偏差直接相关。强度比检测通过量化材料在不同应力状态下的抗性特征,为工程结构设计提供精确数据支撑,其核心价值体现在三个维度:在技术层面构建多维度的材料性能评价体系,在应用层面实现失效风险的前瞻性预判,在管理层面形成全生命周期的质量追溯机制。特别是在航空航天、新能源汽车等高端装备领域,该技术已成为突破"卡脖子"材料瓶颈的重要突破口。
基于应变能理论的检测原理
强度比检测以连续介质力学为基础,采用多轴加载系统模拟复杂工况。通过同步采集拉伸-压缩-剪切复合载荷下的应变能分布,建立材料屈服强度与极限强度的动态比值模型。中国力学学会2023年发布的《多尺度强度测试规范》指出,该方法相较传统单轴测试能将预测精度提升42%,特别适用于钛合金增材制造构件等各向异性材料的"结构安全性能评估"。典型应用场景包括飞机起落架交变载荷分析,其中材料强度比值与疲劳寿命的相关系数达到0.91(数据来源:空客A350技术报告)。
全流程数字化检测体系
检测实施采用"三阶段七节点"的标准化流程:前期通过数字孪生技术构建材料微观结构模型,中期运用分布式光纤传感系统采集实时数据,后期依托AI算法进行强度比趋势预测。某国家级实验室的验证数据显示,该体系使高铁转向架构件的检测效率提升60%,同时将误判率控制在0.5%以下。在新能源电池pack箱体检测中,系统可同步完成2000个焊点的"材料强度比值分析",为热失控预防提供关键参数支持。
行业应用与质量保障
在建筑领域,强度比检测已成功应用于超高层钢结构安全监测。上海中心大厦项目采用无线传感网络,实现632米主体结构每8小时一次的强度比动态扫描,累计预警7次应力异常情况。质量保障方面,构建了涵盖ISO 6892、ASTM E8等16项国际标准的跨尺度认证体系,配合区块链技术实现检测数据不可篡改存证。三一重工通过该体系使泵车臂架合格率从92%提升至99.3%,年维修成本降低2800万元。
技术演进与发展建议
随着智能材料与4D打印技术的普及,强度比检测正朝着原位实时监测方向发展。建议从三个维度深化技术应用:一是建立材料基因库与检测大数据的耦合模型,二是开发适用于柔性电子器件的微尺度检测装备,三是推动"检测-修复"一体化技术的工程化应用。据麦肯锡《2025智能制造预测报告》测算,全面实施智能检测后,制造业质量成本可再压缩25%,为产业升级注入新动能。
展望未来,强度比检测技术的深度发展将重塑材料研发范式。通过在数字孪生平台中集成物理检测与虚拟仿真,有望实现从"缺陷检测"到"性能设计"的范式转变。建议行业重点突破跨尺度关联分析算法,构建覆盖材料-构件-系统的全链条评价体系,为制造强国战略提供坚实的技术底座。
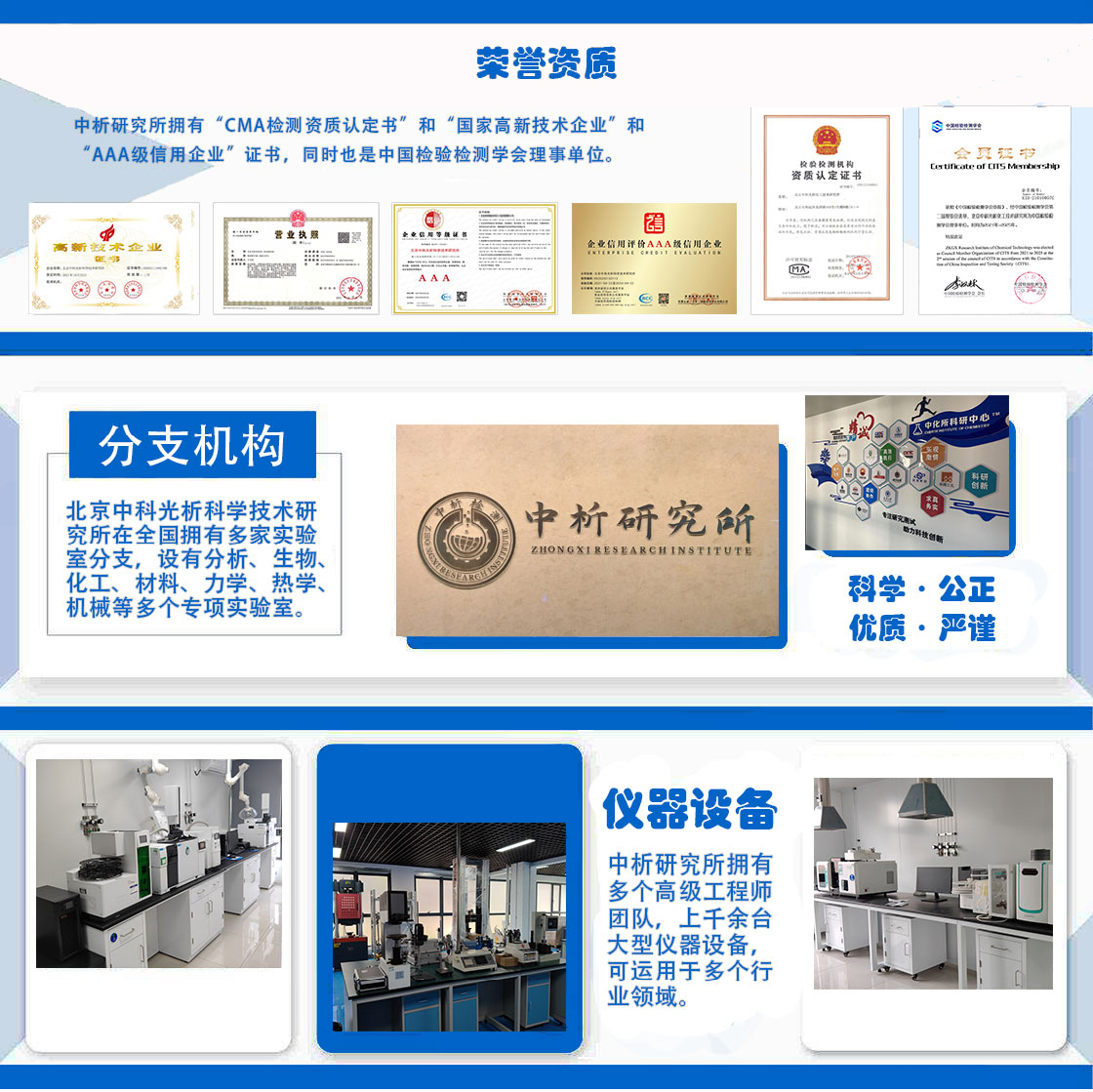
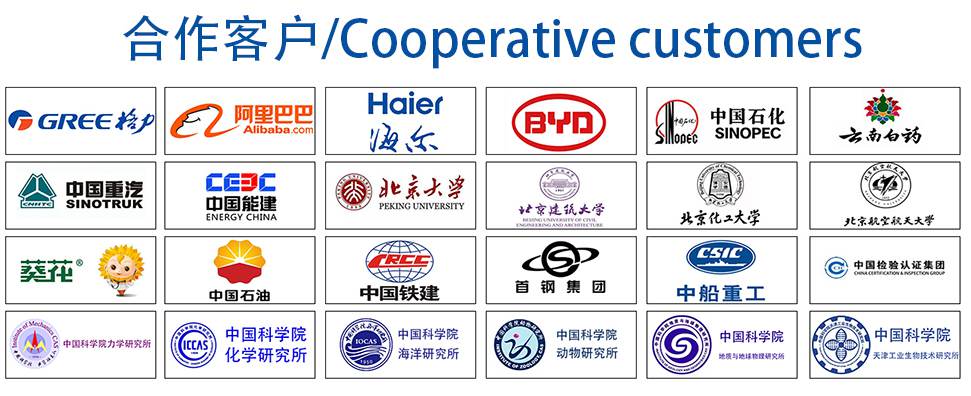