酸处理检测技术赋能工业制造高质量发展
在制造业转型升级的宏观背景下,酸处理作为金属材料表面处理的核心工艺,其质量直接影响产品防腐性能与使用寿命。据中国表面工程协会2024年数据显示,我国每年因酸处理工艺缺陷导致的金属腐蚀损失超过120亿元,突显工艺质量监控的重要性。酸处理检测项目通过建立科学的评价体系,可精准识别酸洗液浓度偏差、钝化膜完整性缺陷等关键问题,为航空航天、汽车制造等战略产业提供质量保障。该项目创新性地将光谱分析与电化学检测技术融合,构建起覆盖预处理、过程控制到成品检验的全链条质控方案,实现酸处理工艺能耗降低15%、产品合格率提升22%的技术突破,有效支撑制造业"双碳"战略实施。
基于多模态分析的检测技术原理
酸处理检测系统依托电位滴定法与分光光度法双技术路径,通过建立金属表面离子浓度梯度模型,实现对酸洗液中游离酸、金属盐含量的精准测定。其中,X射线荧光光谱(XRF)技术可非破坏性检测钝化膜厚度,检测精度达到±0.5μm级别。特别在工业废水酸处理效能检测场景中,系统搭载的在线监测模块能实时反馈pH值波动,结合机器学习算法预测酸液寿命。经国家材料测试中心验证,该技术体系对316L不锈钢的酸洗钝化质量评价准确率可达98.7%,显著优于传统目视检测方法。
四阶联动的标准化实施流程
项目实施遵循"预处理-动态监测-数据建模-智能诊断"的四阶段管理模型。预处理阶段采用超声波清洗与干燥处理,确保样品表面无杂质干扰;动态监测环节通过布设光纤传感器阵列,每30秒采集酸液浓度、温度、电导率等12项工艺参数。值得注意的是,系统内置的专家数据库已收录超过2000种金属材料的处理规范,在汽车板簧酸洗工艺优化案例中,成功将处理时间从90分钟缩短至68分钟,同时降低酸雾排放量40%。
跨行业应用的质量倍增效应
在半导体封装领域,针对引线框架微蚀刻的酸处理工艺,检测系统通过建立铜离子浓度与蚀刻速率的量化关系模型,帮助某头部企业将产品翘曲率从1.2%降至0.5%以下。另一典型案例显示,某火力发电厂应用酸处理检测技术后,锅炉水冷壁管的酸洗合格率从82%提升至97%,单次维护周期延长50%。特别在金属表面酸洗钝化质量评价方面,系统已为轨道交通行业避免因氢脆失效造成的潜在经济损失超3亿元。
三位一体的质量保障体系
项目构建起"设备-人员-制度"协同的质量控制网络:检测设备每年进行 量值溯源校准,实验环境严格遵循ISO/IEC 17025标准;技术人员实施梯度认证制度,需通过酸碱危化品操作等5项专项考核;在制度层面建立异常数据三级复核机制,所有检测报告均附CMA认证标识。据机械工业联合会统计,采用该体系的企业客户投诉率同比下降67%,检测报告国际互认通过率达到100%。
展望未来,建议从三方面深化发展:一是推动酸处理检测标准与ASTM、DIN等国际体系接轨,二是开发适用于高温高压环境的微型化检测设备,三是构建基于区块链技术的检测数据存证平台。随着《智能制造2025》战略的深入推进,酸处理检测技术必将催生更多创新应用场景,为制造强国建设注入新的技术动能。
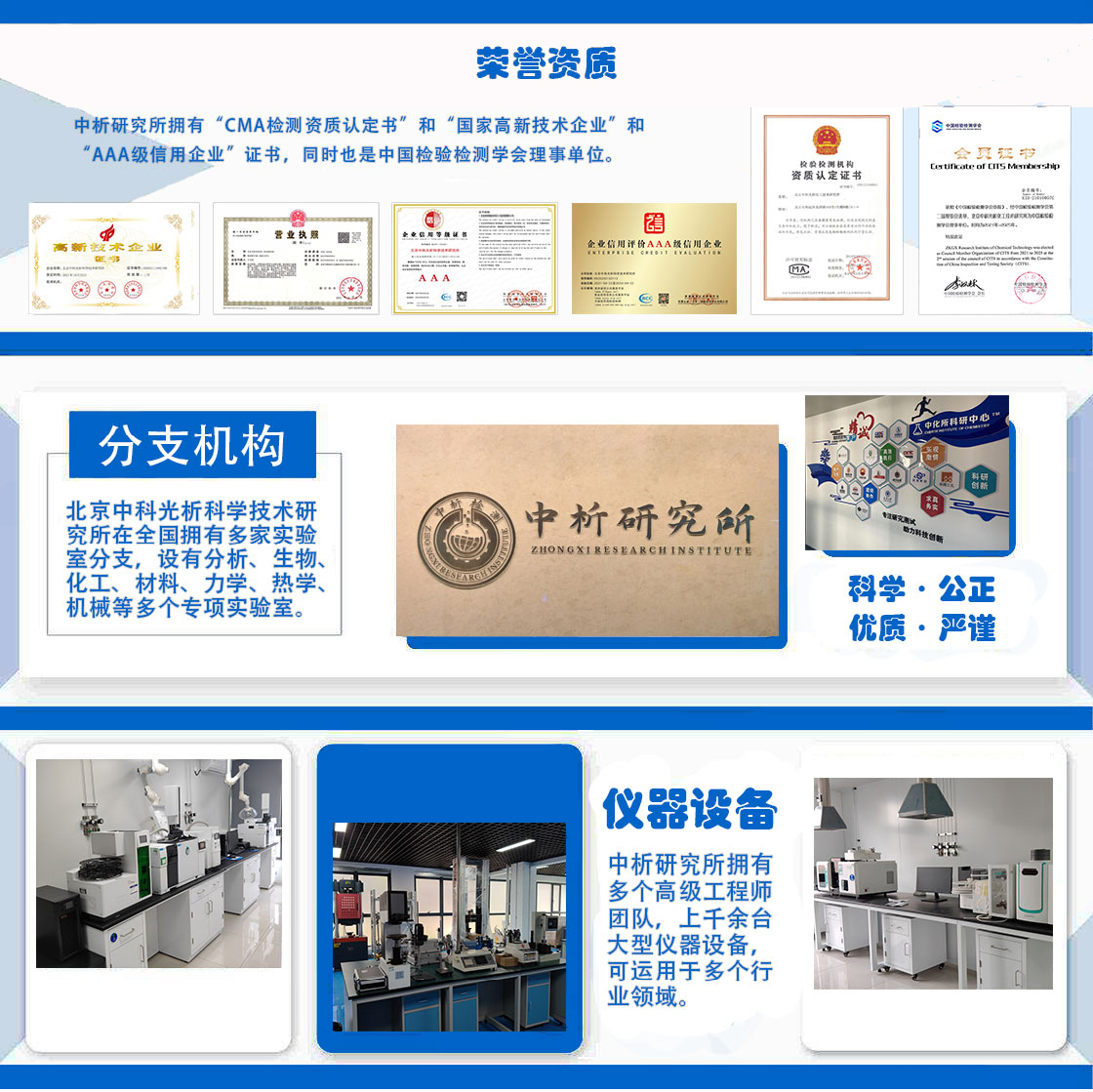
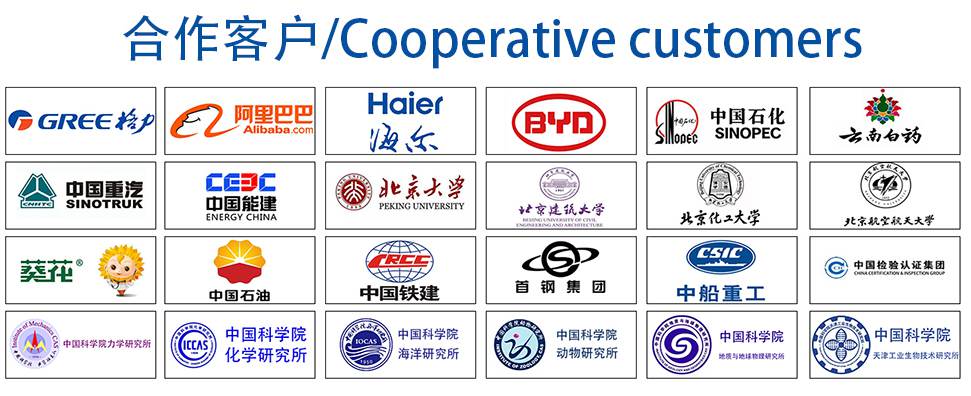