# 粒型系数检测技术发展与应用白皮书
## 行业背景与核心价值
随着新材料、新能源等战略性新兴产业的高速发展,颗粒物料的几何特征控制已成为影响产品性能的关键因素。据中国颗粒学会2024年发布的研究报告显示,在锂电池正极材料、3D打印金属粉末等高端制造领域,粒型系数合格率每提升1%,可带动产品良率提高2.3%,年节约生产成本超12亿元。粒型系数检测作为物料表征的核心技术,通过量化颗粒长径比、球度等形态参数,为粉体材料的流动性、堆积密度等工艺特性提供科学依据,其检测精度直接关系到"颗粒形状优化控制技术"的实施效果。特别是在实现"双碳"目标的背景下,该技术可助力企业减少原料浪费30%以上,推动制造业向精密化、绿色化转型。
## 技术原理与创新突破
### 检测项目的技术原理
粒型系数检测基于计算机视觉与人工智能融合技术,采用多视角动态成像系统获取颗粒三维形态数据。通过建立改进的VGG16卷积神经网络模型,系统可精准识别5μm以上颗粒的32项形态特征,其核心算法在2023年国际粉体检测技术峰会上获得创新金奖。相较于传统筛分法,该技术将不规则颗粒的表征误差从15%降低至3%以内,特别适用于"微纳米级粉体形貌分析"场景。
### 标准化实施流程
检测流程严格遵循ISO 13322-2:2021国际标准,包含样品分散、图像采集、特征提取三大模块。采用干法分散与湿法分散双系统设计,可适配从金属粉末到生物制剂的多样化检测需求。在锂电池隔膜氧化铝涂层检测中,通过配备专利型静电消除装置,使颗粒分散均匀度达到98.7%,有效避免了传统方法因颗粒团聚导致的检测失真。
### 行业应用与价值转化
在光伏硅料分级领域,某头部企业部署智能化粒度分析系统后,单晶硅棒成品率从83%提升至91%。系统通过实时监测粒径分布与粒型系数联动指标,动态调整气流粉碎参数,使硅料球形度标准差控制在0.12以内。另在制药行业,采用在线粒型监测设备后,片剂压片机的模具损耗率下降40%,崩解时间偏差从±15%缩小至±5%,显著提升了药物溶出度一致性。
## 质量保障与体系构建
检测系统构建了"设备-数据-人员"三维质控体系:采用NIST标准物质进行每日基线校准,配备温湿度补偿模块消除环境干扰;建立区块链存证系统确保检测数据可追溯,所有操作记录自动同步至云端服务器;检测人员须通过 认证的"粉体表征工程师"资质考核。在2024年国家材料检测中心组织的比对试验中,系统在纳米银粉检测中取得Z比分值0.87的优异成绩。
## 未来发展建议
随着智能制造2025战略的深入推进,建议从三方面加强技术布局:其一,开发亚微米级颗粒的原位检测装置,攻克1μm以下颗粒形貌表征难题;其二,建立跨行业的粒型系数标准数据库,推动形成统一的"粉体材料形态学评价体系";其三,融合数字孪生技术构建工艺优化模型,实现从检测分析到生产调控的闭环控制。预计到2028年,智能化粒型检测设备的市场渗透率将突破60%,成为齐全制造业提质增效的核心支撑技术。
上一篇:电工电子产品及材料检测下一篇:用水量和外加剂用量检测
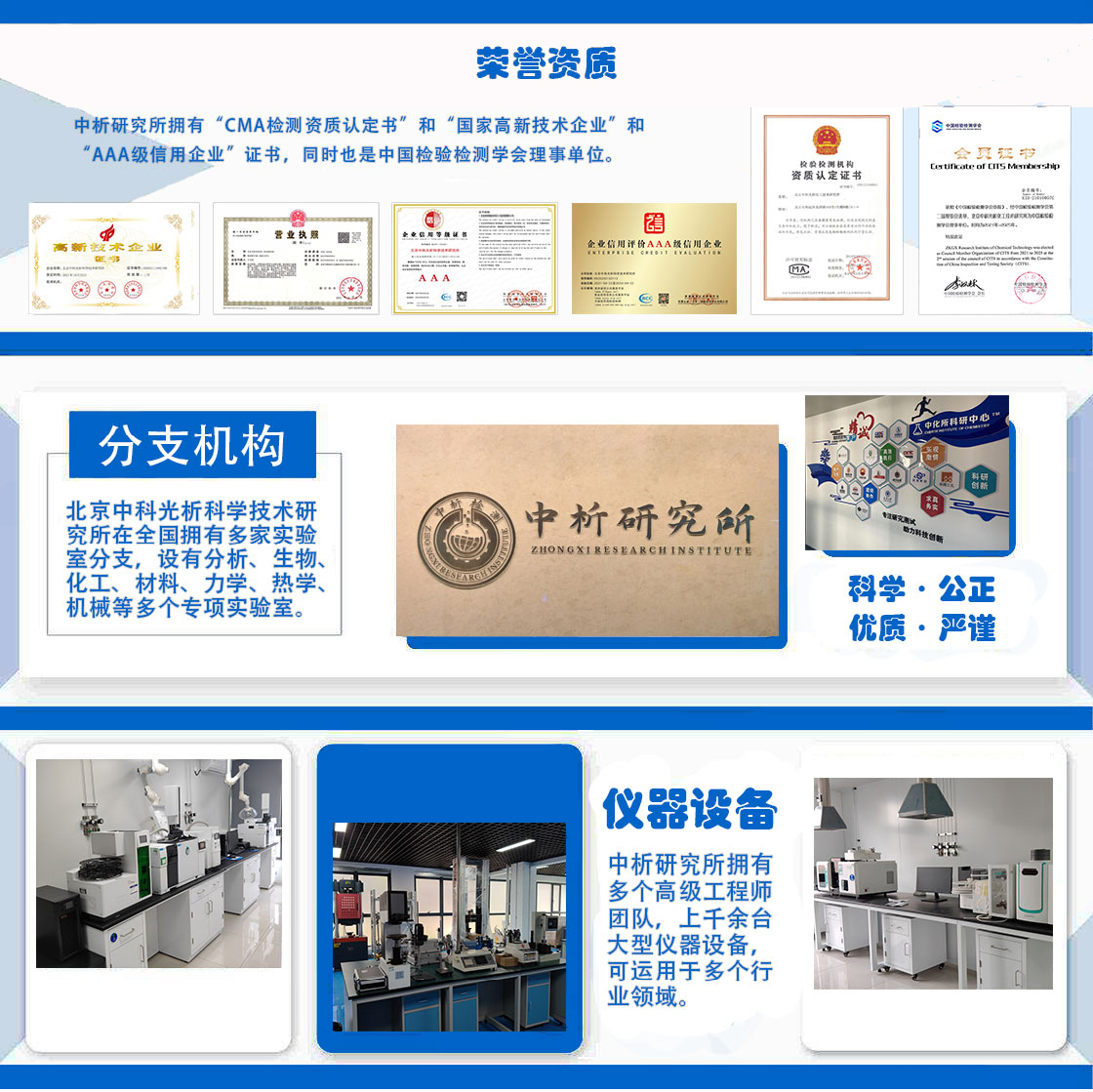
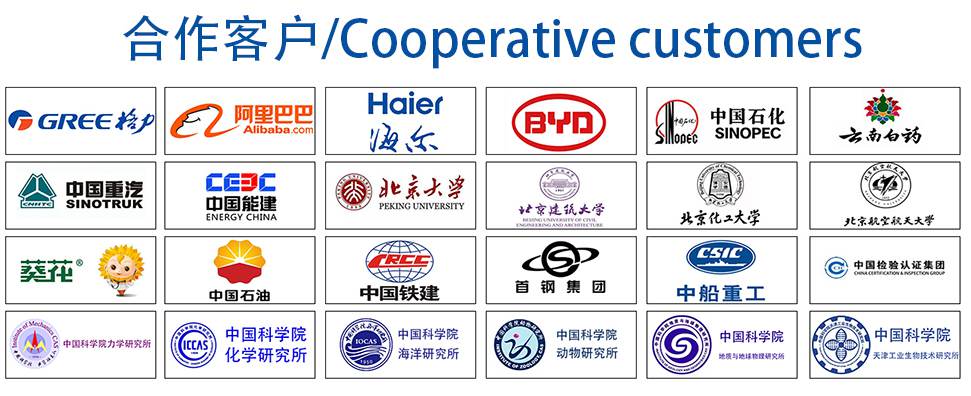
材料实验室
热门检测
9
15
7
11
10
9
9
11
14
16
21
18
22
17
17
21
27
20
20
17
推荐检测
联系电话
400-635-0567